15 Cold Milling Machines Take On One of the World’s Biggest Ever Milling Projects
The renovation of the Leipzig/Halle Airport required the complete removal of more than 2 miles of runway as well as the connecting taxiways in under 30 days. 350,000 metric tons of extremely hard concrete reinforced with rebar mats (Continuously Reinforced Concrete Pavement – CRCP) were removed in the course of the cutting process. To complete such a large project, the contracting company used powerful machines from Wirtgen’s W 250 Fi class with special modified milling drums.
It was necessary to completely remove the north-side runway due to “concrete cancer,” an alkali-silica reaction also found in older concrete-paved highways, which irreparably destroys the concrete from within.
A project of this magnitude requires high-performance machines and optimal cutting tools for the milling drum. With over 1,000 hp, the Wirtgen W 250 Fi class always has sufficient power reserves. The large milling machines were equipped with additional ballast weights in order to exploit their full performance potential in the cutting process. The greater operating weight leads to greater traction of the track units and optimal cutting performance by the milling drum. The large milling machines for the Leipzig Airport project were also fitted with ECO milling drums and special picks. ECO milling drums have up to 50% fewer picks at larger tool spacings than standard milling drums. Using fewer cutting tools reduces cutting resistance, which also makes it possible to mill harder concrete pavements.
The powerful milling fleet removed 350,000 metric tons of concrete within just 30 days. This means that each machine had to mill off an average of over 1,100 tonnes of concrete a day. The first step was to remove the concrete surface in layers as quickly as possible. Once this was done, machines with extremely precise 3D leveling technology on-board were used to create an optimal base for the subsequent resurfacing.
CONCRETE MILLING
Concrete milling is an established technology worldwide and Wirtgen has successfully applied it in many projects. It can also remove reinforced concrete containing tie bars, dowel bars, and steel mesh. Additionally, selective removal enables the separation of concrete layers with different properties, thereby reducing contaminated material. A further benefit: In most cases, milled concrete can be recycled without any further treatment.
MINIMAL CARBON FOOTPRINT
Even the granulated concrete generated by the airport project in Leipzig was 100% reused as valuable recycled building material. After being stored temporarily near the building site, it was used in later renovation stages for the roadbed of the new runway. The short transport route and minimal need for new material left a very small carbon footprint.
On top of this, the Wirtgen cold milling machines themselves offered a broad spectrum of environmentally-friendly machine technologies. Fuel-optimized speed ranges in milling mode controlled by Wirtgen Mill Assist and engine-temperature-controlled fan speeds, for example, help protect the environment and conserve valuable resources. Automatic activation and deactivation of the water spraying system and water metering dependent on milling performance considerably reduce water consumption.
PLANNING AHEAD IS KEY
To ensure a smooth process, project planning began far in advance. Practical use tests started as early as 8 months before the job began. This enabled precise consumption estimates for picks and other wear parts and the procurement of sufficient replacement stock that was stored at the site, minimizing machine downtimes for pick replacement and maintenance and assuring maximum productivity.
Thus, the large-scale runway rehabilitation project at Leipzig/Halle Airport was successfully completed within the allotted timeframe, and the groundwork for this success was the timely removal of the concrete as well as the optimal milling results.
CLOSING THOUGHT
Project and branch manager Bernhard Fischer from Kutter, the construction company leading the project, expressed his satisfaction with its successful completion: “In contrast to milling in asphalt, the extreme hardness of this concrete meant that we had to use slower milling speeds. The wear on the milling tools was also significantly higher. The additional costs of increased wear on material were more than compensated for by the rapid progress we made and the precision of the results. The removal of the concrete by cold milling was the ideal method for this project.”
For More Information:
For more about Wirtgen’s equipment, visit www.wirtgen-group.com.
Modern Contractor Solutions, June 2023
Did you enjoy this article?
Subscribe to the FREE Digital Edition of Modern Contractor Solutions magazine.
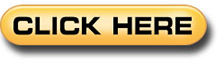