Concrete is the foundation of most of our infrastructure. However, the process of concrete production has remained relatively unchanged for decades. From creating and transporting concrete to eventually dealing with concrete being returned to the plant, there are opportunities to help ready-mix producers improve efficiency and reduce material waste, thus becoming more sustainable in addition to reducing their costs.
Two of the toughest challenges for ready-mix producers are the lack of information available to make informed decisions and the automation of the systems needed to reduce process variability and waste.
THE PROBLEMS
Ready-mix producers interact with multiple individuals every day who have different perspectives of how the final product should look and how it should perform. During the process some people do tasks or make decisions that they are not trained to do which can compromise the integrity of the final product. For example, drivers and site teams can make decisions about water addition in fresh concrete. The largest reason for rejected loads and defects in finished structures in the industry is uncontrolled water additions. In many cases, the impact of uncontrolled water addition is not visible until after the concrete is in place. Another key issue is when concrete is in transit. When concrete is being delivered there is little to no monitoring of the mix and the slump can fall out of the range it was designed for. Because of these issues the National Ready Mix Concrete Association (NRMCA) estimates 3-5% of ready-mix concrete deliveries in the U.S. are rejected at the jobsite for various reasons, such as not meeting specifications. This concrete is oftentimes dumped into landfills, which is expensive and a waste of resources for the producer, and impacts customer satisfaction and the environment.
To mitigate inconsistencies, the ready-mix producer is required to increase the amount of overdesign (safety factor) of the concrete mix design, often by adding additional cement to the mix. This increases the cost and the carbon footprint of the mix.
SOLUTION: EMBRACE AUTOMATION
In transit concrete management (ITCM) is the final piece of the puzzle in terms of process visibility and automation in the manufacturing of fresh concrete. The VERIFI® in-transit concrete management system from GCP uses over 10 years of continuous research and development data, from more than 20 different truck types and hundreds of types of concrete, to collect over 90 billion rheological data points to deliver over 100 million yards of concrete. The system uses sensors installed on ready-mix trucks to collect real-time data that enables producers to monitor, measure, and manage concrete properties while the concrete is in transit to the jobsite. The data transmits a status from on-board computers to the cloud every 15 seconds, making the data accessible to the producers and contractors’ teams on phones, tablets, and laptops.
By controlling water additions and giving visibility to site behavior, VERIFI enables the production process to be brought under control. Benefits include limiting concrete being rejected for being too wet or segregating and its associated impact, improving contractor satisfaction and reducing the carbon footprint of the process as less concrete is sent to landfills. Samples taken for cylinder tests will show improved strength results over time as they become less and less likely to have been taken from loads that have had uncontrolled water addition, and therefore more likely to hit their design strength. This in turn will positively impact mix designs as standard deviations reduce, allowing reduction in cement contents. Shifting the average delivered slump closer to the specified slump by 1 inch can reduce cement content of the design mix by 25 pounds and save more than 21 pounds of CO2 from being emitted.
BENEFITS ADD UP
Time efficiency on the jobsite can be improved by ensuring that loads show up ready to pour. The collected data shows that there is on average a 10% reduction in cycle time on loads that have used ITMS water addition only to keep the concrete at the specified slump versus loads that have manual water additions. When there is a manual water addition, the driver has to spend more time on site mixing water in. This not only increases cycle time, but also increases fuel usage and emissions at the jobsite. Reducing cycle times by 10% means that trucks can be utilized more effectively and projects can place more concrete per shift.
An added benefit that the VERIFI system provides is increased fuel efficiency. In ready-mix concrete delivery, fuel use is a significant source of cost. The ability to track truck locations and truck routes allows for shippers to find when drivers have taken a less than optimal route and correct that on their next delivery. In addition, approximately 23% of fuel in a concrete delivery is used for high-speed drum rotations that mix the concrete. Traditionally, the truck driver has to determine the timing of rotations, using minimal information about concrete consistency or fuel efficiency. In contrast, real-time data from the VERIFI system gives the driver instructions on the optimal number and timing of rotations. Data suggests that the number of high-speed revolutions can be reduced by 10%, representing significant cost reductions.
CLOSING THOUGHT
The VERIFI system is the critical missing link in optimizing and increasing efficiency in concrete production. It provides never before available data on fresh concrete throughout the delivery cycle that can be instantly shared within the producer’s organization and across the supply chain. The overall impact of addressing this gap with the VERIFI system is a smaller carbon footprint with less waste and the associated benefits throughout the process for the producer and the contractor placing concrete.
About the Authors:
With GCP, Angie Khaw is a North American product manager for concrete admixtures; Helen Frape is business analyst innovation and change; and Jason Straka is a VERIFIˇ product manager. GCP is a construction products technologies company with concrete and cement additives, building materials, and technologies that ensure specified quality and enhance business productivity. For more, visit gcpat.com.
Modern Contractor Solutions, February 2022
Did you enjoy this article?
Subscribe to the FREE Digital Edition of Modern Contractor Solutions magazine.
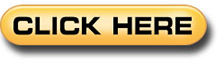