Considerations for specifying the right plywood for the job
Concrete formwork may represent close to half the cost of a concrete structure. For cost-effective building, contractors select forming panels that will stand up to the job and to multiple uses. Member manufacturers of APA – The Engineered Wood Association produce a variety of plywood form panel products called Plyform® designed for most general concrete forming applications. Plyform panels are usually pretreated with a release agent to facilitate stripping and are available in many grades from basic B-B Plyform panels to panels with overlays such as “Medium Density Overlay” (MDO) and “High Density Overlay” (HDO) Plyform panels. The overlays add stability, resist abrasions, and provide a smoother and more durable forming surface.
Each producer of overlaid concrete forming panels offers proprietary products with a variety of different features and benefits.
CHOOSING PANELS
When planning multiple reuses, it is best to use plywood with more durable construction. All Plyform panels have more solid and stronger veneers than traditional sheathing panels, offered in a range of durability. All Plyform panels produced are rated as Class I, which means that they are manufactured with the strongest and stiffest veneers. The grades of veneer used in Plyform panels are indicated in the APA trademark.
MDO and HDO overlaid panels have resin-impregnated cellulose fiber sheets laminated to their faces and can have either single-sided or double-sided faces. With careful handling and maintenance, any double-faced forming panel, from B-B Plyform to the overlaid panels, can be poured against on both sides.
HDO forming panels have a greater amount of resin in the overlay and their surfaces are harder and more impervious to water and impacts than MDO forming panels. A greater number of uses and smoother finish on the surface of the concrete can be expected when using HDO Plyform.
Forming panels with MDO faces are often only overlaid on one side, but may have pourable faces on both sides of the panels. While MDO surfaces are not as smooth and durable as HDO panels, a contractor should expect to get more pours from them than the panels without overlay or other surface treatment. The finish of the concrete from an MDO surface is “softer” and not as “slick” as that formed against HDO panels.
There are many different types of overlays and treatments for Plyform panels that can be used to maximize durability. B-B and B-C Plyform panels can be made more durable and resistant to moisture with a coating such as polyurethane or other type of liquid surface treatment. One of the newer, high performance overlays is phenolic surface film.
Bonus tip: Not all MDO and HDO overlaid panels are designed for concrete formwork. Note that there are High Density Overlay, Industrial, and Medium Density Overlay General panels that are manufactured for applications other than concrete forming. So take care when specifying and purchasing concrete forming panels and look for the APA trademarks that clearly identify the panel grade and type, which are your assurance of quality and reliable performance.
HOW MANY POURS?
The amount of pours you can get from one form panel depends on the type of form panels used, as well as their care and maintenance. Nearly all types of plywood panels can be used in concrete forming, from common roof and wall sheathing to sanded panels. APA Plyform panels, however, are specifically designed to withstand the wear-and-tear of repeated concrete pours, as well as to provide a more smooth and consistent finish to the concrete’s surface.
Many factors affect the number of pours anticipated from concrete-forming plywood, including the desired finish on the concrete; durability of the panel’s surface, including overlays; the types of concrete formulation; and which release agents are used. The most critical factor is the handling and care of the form panels.
With reasonable maintenance, more than five pours can be expected from a B-B grade Plyform, while HDO panels can withstand up to 20–50 reuses or more, and somewhere in between with MDO Plyform. In fact, with proper care, some proprietary concrete-forming panels can achieve 100 or more reuses.
Bonus tip: Because panels absorb water, and the increase in moisture content usually causes the panels to expand and move, it is important to adequately fasten the form panels to the framing and to leave space between the panels that allows for their flatwise movement within the formwork.
CARE FOR YOUR PANELS
Optimize the life and performance of forming panels by applying a release agent prior to every pour. Use only non-ferrous wedges and tools, such as wood or softer plastics, to remove excess concrete from the faces and edges of the panels. Store the panels face-to-face to protect cleaned surfaces. Protect panel corners and edges, both which are vulnerable during removal and handling. If form panels are cut, reseal the ends and edges to protect them from excessive moisture. Consideration should be given to the admixes in concrete formulations when choosing a type of forming panel, understanding that overlaid panels provide greater resistance to chemicals.
For more information:
To find concrete-forming panel manufacturers, APA’s Concrete Forming Design/Construction Guide, and more detailed information on concrete forming materials, visit www.performancepanels.com.
Modern Contractor Solutions, February 2019
Did you enjoy this article?
Subscribe to the FREE Digital Edition of Modern Contractor Solutions magazine.
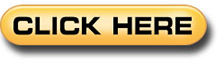