It is time to reconsider light gauge steel (LGS) framing. The methods and economics of LGS have been changed by the power of the computer.
LGS framing began as a kind of alternative version of wood lumber framing. Until recently, both have always been labor-intensive processes of measuring and hand-cutting each stud to the length needed in the specific location, and adding holes for utilities, notches for unusual connections, etc., before frames could be assembled. In the case of LGS, the two main profiles, C-shaped studs and U-shaped rails, were roll-formed by the mile in steel mills, chopped to standard lengths, and shipped to the jobsite as “blanks” for all that hand-work.
Digital fabrication is changing all that. A computer-numerically-controlled (CNC) smart roll-former does all the customization as the steel is being formed into the stud shape, before human hands ever touch it. A CNC-LGS system uses data from the designer’s computer files to engineer frame panels, and instructs the roll-former to customize each element for its specific position and functions in the wall, floor, or truss. It spits out a virtual framing kit. The pieces are even numbered for assembly.
Many systems are compact enough to operate out of a standard shipping container. Digitally fabricating on the jobsite increases construction speed, lowers labor, materials, and transportation costs. Forming and panelizing off-site in a factory setting yields even more dramatic savings.
This updated method lowers the cost of steel framing, and changes the calculation of wood vs. steel. It produces better walls than conventional methods, and it makes them faster to build. It also offers performance and environmental benefits to the owner.
The range of buildings that can be produced by these systems is expanding. While the first machines were only capable of 2×4 or 2×6 members, the range of current machines can form from 2.5 inch 27-gauge studs up to 14-inch beams in up to 12-gauge steel, capable of making buildings up to 8 stories. Machines capable of even bigger elements—16-inch and 8-gauge steel—are expected soon.
This 14-inch wide member is formed in 12-gauge steel, and includes an additional 12-gauge steel stiffening insert. These systems can produce framing good up to six stories. Machines with even larger capacity are expected soon. Image courtesy of Pinnacle LGS.
DIGITAL FABRICATION
Digital fabrication is the science of using computer-based 3D design information to drive real-world fabricating machinery. In the case of CNC-LGS, a smart roll-former can not only bend a stud or rail profile, but can also punch holes and notches, and do special crimping.
“CNC-LGS makes beautiful steel,” explains Eoin Madden, who is general manager, sales, North and South America with Pinnacle LGS, a leading manufacturer of CNC-LGS systems. “With computer control, there’s no difference between ‘standard’ and ‘custom.’ Every piece is formed to its precise length, and fully detailed for all its functions and attachment points. Every screw-hole and utility access is punched. The screw-holes are also dimpled, so screw-heads lay flush—no more bumps in the drywall. Stud-ends are swaged, allowing them fit inside a rail that is the same width as the rest of the stud. That also makes the wall flatter, and the studs bear squarely the bottom of the rail, not just on the curved edges. Notches for fitting cross pieces are made. And everything fits properly. The frames are gorgeous.”
The newest CNC-LGS systems include both powerful structural analysis and the ability to build a wide range of different sizes of structure. It can make them fast, too, up to 3,000 linear feet per hour for standard studs and rails. (Trusses take a little longer.)
MAKING WALLS
CNC-LGS is a collaboration of software and hardware. The software provides basic engineering of code-approved structures, including the abilty to add regional code factors such as wind, seismic, snow-load, and similar customizations. Based on that design, it instructs the hardware and makes the steel.
The heart of it is a 3D computer model, derived from the designers CAD or BIM files, that knows all the building’s details and how they fit together.
The hardware portion is a miniaturized, automated assembly line in one compact machine. Flat coil steel is fed into one end and through a series of forming stations where it’s cut to length, punched, notched, dimpled, and crimped as needed, and then bent into studs or rails and spit out the other end. Then there are assembled simply on a flat table with a screw-gun.
ADVANTAGES OF CNC-LGS
A contractor with his own CNC-LGS system can potentially be more competitive on price, and can turn over work faster, enabling him to do more business. The walls will also be higher in quality, another competitive edge.
Savings on materials come by buying flat coil steel direct from the mill, saving up to 40 percent on materials. CNC-LGS also eliminates cutting waste, which is generally estimated at about 10 percent of materials. It can also reduce transportation of frames by up to 90 percent.
Fabrication and construction of frame panels can be done faster with less labor, either at the jobsite or off-site in a factory setting. Off-site assembly with lower-skilled labor can offer significant savings, and allows year-round work in a controlled environment. A contractor can build walls at the same time as digging the foundation and waiting for the concrete. This ramps up the schedule and makes more business possible in the course of a year. ■
About the Author Steven H. Miller, CDT, is an award-winning writer and photographer, and a marketing communications consultant specializing in issues of the construction industry. He can be contacted at steve@metaphorce.com.
Modern Contractor Solutions, August 2014
Did you enjoy this article?
Subscribe to the FREE Digital Edition of Modern Contractor Solutions Magazine!
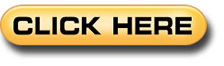