By Jeff Winke
The history of the construction excavator goes back quite some time. The very first excavator is said to have been built in 1882 by Sir W. G. Armstrong & Company in England, where it was used in the construction of Port of Hull docks. Unlike today’s excavators that use hydraulic fluid, water was used to operate the hydraulic functions back then. It was not a true hydraulic machine, but an approximation that used cables to operate the bucket, and with a hydraulic cylinder operating a set of multiplying sheaves. The idea on Sir W. G. Armstrong’s machine was not successful, nor were machines of somewhat similar design, which followed and were built into the start of the 20th century.
INNOVATION IN DESIGN
These first excavators and successors that were developed and evolved well into the 1990’s are virtual dinosaurs when compared to the sophisticated machines available for the mining, construction, and utility markets today. Today, construction equipment manufacturers have an emphasis on developing technologically advanced and efficient excavators that are designed to be more productive. Manufacturers are also trying to meet the propelling growth of the global excavator market.
From large construction areas to small jobs in tight areas, there are a wide range of excavators to meet the needs of any construction job. Conventional tail swing models are designed to offer increased side and lifting stability, while the minimum tail swing models are designed for jobs in tight quarters, with no room for wasted movement. All technologically-advanced excavators are designed to optimize the material moving process in the construction industry.
AUTOMATED CONTROL
There have also been developments in how heavy equipment is controlled. Automated control has changed the earthmoving process with GPS machine control systems governing motor graders and dozers.
Automatic excavator technology is now available with the intent of contributing to higher productivity, just as the earthmoving systems have proven. Automatic excavator systems are designed to control depth of excavation automatically, as well as the angle of the boom, stick, and bucket at all times, while following the site plan.
The Topcon X-53x Automatic Excavator System is a 3D modular system that provides automated depth control, which enables it to dig to grade in flat, stepped, or sloped applications. The machine learning-based calibration system is designed to be easier, faster, and less error prone—resulting in better outcomes on projects.
With an automatic excavator system, any design-grade surface can be dug once a grade or trench design is loaded onto the machine’s onboard Windows-based computer display. Alternatively, the operator can build their own design in the field. The system is designed so that as the operator begins digging within a chosen “working window” or depth range, the machine will, if preset, take control and dig to the design grade. The customizable joysticks are designed to work as the primary interface for the system, reducing the need to refer back and forth to the display. Cycle times are expected to be faster and more accurate.
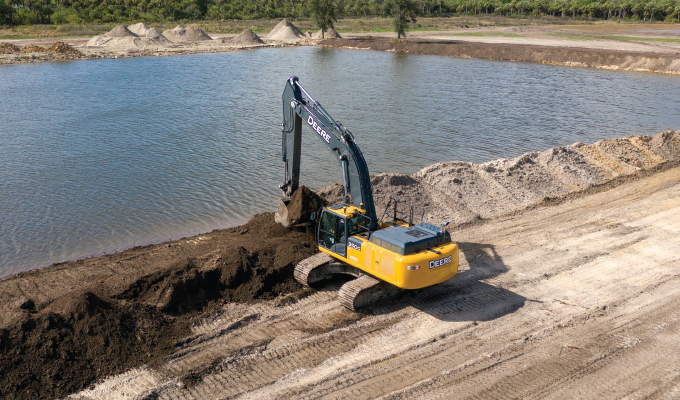
GAME-CHANGER SYSTEM
According to Al Ruiz, superintendent, Tomahawk Construction, Fort Myers, Florida, the Automatic Excavator system has been a “game changer” for a project constructing 24 lakes in a residential construction site called Brentwood Lakes in Naples Florida.
“In the old way of digging a lake—when you thought you had the slope pretty close, you’d get out of the machine and checked it with a story pole and then got back in and realized you were two tenths off and then cut two more tenths off and then checked it again. So, every time you had to get out of your machine and check it, you were stopping your work flow. With the Topcon system, we don’t need to stop production and can keep producing as we move on.”
Andrew Montgomery, foreman, Tomahawk Construction, adds that it makes seasoned operators even more productive. He says, “It’s a great tool—it makes you better. I’m pretty good I think, but I can’t build as fast as what the GPS can. It definitely helps speed up our process. It won’t let you dig past grade—it will stop you. You can actually let go with one hand and you can pull with your left hand with the automatics on. It’ll lock the bucket in place.”
OPERATING ON GRADE
The intent with the automatic excavation system is to keep the operator on grade, even when working on complex jobs, while saving time and reducing costs.
An advanced tilt-rotator functionality is designed to allow operators to swivel or tilt the bucket with automatic boom control for faster and more efficient excavation. If excavator operators are in situations such as at the top of the slope, grading a long incline and not totally perpendicularly lined up, positioning the cutting edge of the bucket to the surface is expected to be easier. It is designed to allow operators to excavate more quickly, moving the machine fewer times, with less wear and tear on the chassis.
CLOSING THOUGHT
The industry has seen how much automated control changed the earthmoving process and now the expectations are to see similar benefits with an automated excavator system. With the technology, complex grade surfaces are expected to be achieved faster and more productively, with the intent that novice machine operators can dig and achieve results like a seasoned experienced professional—which could be seen as another step showing how technology is helping to fill the skilled labor gap.
Ruiz concludes, “There’s an old saying, ‘if you’re not moving forward, you’re moving backwards.’ And you know, in this day and age, if you’re not using a system, like an automatic excavator system, you’re behind the eight ball and there’s absolutely no way that you can be competitive with contractors that are. It’s that simple. It’s a horse and buggy versus a Corvette. And that’s the best analogy I can give you—Topcon is the Corvette, the old ways, horse and buggy.”
About the author:
Jeff Winke is a business and construction writer based in Milwaukee, Wisconsin. He can be reached through jeff_winke@yahoo.com.
Modern Contractor Solutions, August 2020
Did you enjoy this article?
Subscribe to the FREE Digital Edition of Modern Contractor Solutions magazine.
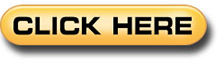