By Andrew Mayer
Chipping hammers are small in nature but can be incredibly impactful on the jobsite. An economical tool that gives contractors a bang for their buck, chipping hammers can take operators a long way if used on the appropriate applications and properly maintained.
The general application for chipping hammers is strictly light demolition, such as chipping out an old brick wall or mortar, etc. Operators should never use a chipping hammer on concrete too thick or in larger-scale jobs like parking garage surface demolition. This results in a short lifespan of the tool. Instead, the use of rivet busters is a great alternative for bigger jobs.
CHIPPING HAMMERS VARIATIONS
There are a large variety of chipping hammers on the market. The options include the style of hammer, cylinder length, and design.
Style. There is a four-bolt unit, which holds the hammer together by the bolts, or a screw-on chipping hammer, on which the handle screws onto the barrel.
Cylinder length. The standard cylinder lengths range from 3 to 4 inches. While not as common, some manufacturers also feature a 2-inch cylinder configuration.
Design. While the principle of chipping hammers is the same, the design of hammers can be different. And, some manufacturers feature more variations than others.
Typically, the most prominent design change from one to the other is the handle and trigger positions, based on user preference. There is the “D” handle or an open handle, which appears more like a gooseneck or pistol grip and can offer the user more flexibility. Additionally, there is either an outside or inside trigger.
Chipping hammers have multiple retainers, but this does not detract from their hitting power. They all offer about the same power and blows per minute. Rather, it is a matter of different features matching up to the user’s application or whichever user-preference they have.
AIR COMPRESSOR MATCH
Chipping hammers require minimal air pressure at 90 psi. This makes it easy to run a gang of hammers off of the common 185 cubic feet per minute (CFM) air compressor. CFM ranges from the smallest hammer taking 20 CFM up to the biggest hammer at 35 CFM (hammers typically do not exceed 35 CFM).
TOOL MAINTENANCE
Daily Use
- Tightness of the tool
- On a four-bolt unit, always ensure handle is tight and still has all four bolts and nuts
- For a screw-on, check to see the handle is screwed on all the way and is not backing off
- If the chipping hammer has a spring retainer, check the integrity of the spring. If it is bent or has lost its integrity and starts to trend to a more oval shape, change it
Monthly
- Take the tool apart
- Clean it out
- Lubricate
- Put the chipping hammer back together
Oiler. To increase the lifespan, it is crucial to always run an oiler. Chipping hammers do not have any onboard oilers, so run an inline oiler to consistently lubricate the tool. The oiler should be placed about 6 to 10 feet in line from the tool.
Retainers. There are different types of retainers throughout the industry, which can be confusing. Quick-change retainers are one style that has become much more common. For quick-change retainers, pull back the sleeve and insert the steel. This uses a round collar steel.
Operators have moved away from spring retainers because the spring is a wear item. With a quick-change retainer, operators do not have to worry about the spring, which makes it easier to change out the tools.
If the tool does have a spring retainer, pull the spring out, remove the retainer, put the steel shank into the cylinder, then the retainer will go over the steel and the spring should be inserted to hold the retainer on. Be sure to use an oval collar for spring retainers.
Chipping hammers are simple to maintain, but providing daily and monthly checks will ensure a longer lifespan of the tool.
BAD PRACTICES
Like any air tool, avoiding dry firings is crucial. This will wear down the components and it will rapidly exhaust the hammers that feature spring-on retainers.
A common bad practice is using the tool on larger applications. Operators use the smaller tool because it is lighter and easier on them. But, by doing so, they are rapidly wearing out the chipping hammer, breaking the retainer and damaging the springs.
Other bad practices to avoid are putting in 18-inch chisels and prying with them. This action places a lot of stress on the retainer and chuck of the tool, ultimately resulting in breaking the hammer.
CLOSING THOUGHT
Chipping hammers may be small, but by performing proactive maintenance and utilizing them in the right applications, they will quickly maximize the return on investment.
Editors Note: Having the right tool for the job is of vital importance. As a business owner, what is your tool of choice for leadership expertise? Let me know what’s in your master toolbox for safety talks, jobsite trailer meetings, and project inspections. Email donna@mcsmag.com.
About the author:
Andrew Mayer is the business development manager, light equipment at Chicago Pneumatic Power Technique (CP). CP’s goal is to deliver best-in-class global service and local support to industrial customers through a network of authorized distributors. For more, visit www.cp.com/en-us.
Modern Contractor Solutions, June 2020
Did you enjoy this article?
Subscribe to the FREE Digital Edition of Modern Contractor Solutions magazine.
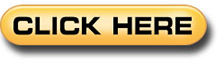