Galvanic corrosion frequently afflicts structures such as commercial roofing, infrastructure elements and facades, and is also common in the restoration of existing structural steel and concrete reinforcement.
By understanding the root causes and manifestations of galvanic corrosion and adopting appropriate mitigation strategies, contractors, property owners and managers can safeguard their investments and ensure the longevity of their buildings.
Galvanic corrosion occurs when two uniquely different metals, such as copper and steel, are physically in contact with each other and immersed in a common electrolyte, such as water/moisture or when the same metal is exposed to an electrolyte with different concentrations. In a galvanic couple, the more active metal (the anode) corrodes at an accelerated rate, and the more noble metal (the cathode) corrodes at a slower rate.
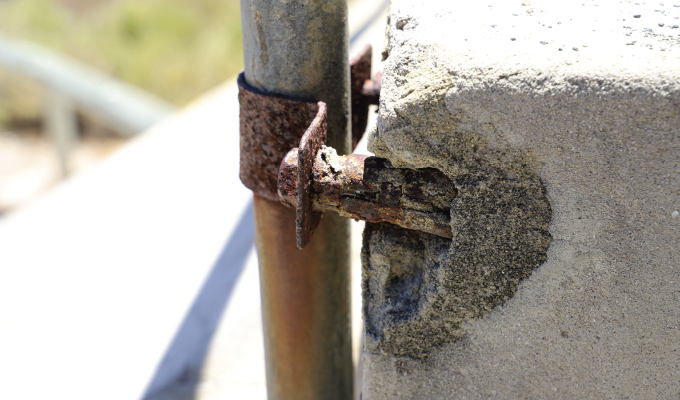
“In the presence of moisture or grime, metals with varying electrochemical potentials encounter each other, setting off electrochemical reactions that lead to the deterioration of one or both metals. You are quite literally creating a battery with the movement of electrons; that’s when the corrosion begins,” says Rod O’Bannon, manager of Western Specialty Contractor’s Sheet Metal Division. “The combination of dissimilar metals will either accelerate the corrosion process or do nothing, but it’s important to understand which combinations of metals will work against you.”
Galvanic corrosion often manifests as chalky mineral deposits, sometimes tinged with a rusty-orange hue (ferrous corrosion). These clusters usually accumulate in concealed areas of a building, such as behind panel systems or under parapet caps. This corrosion may remain undetected until it causes interior water leaks or fosters mold growth, underscoring the importance of proactive assistance and scheduled condition and maintenance. Identifying dissimilar metals quickly and making corrections before damage is noticed is key to preventing future problems.
“Always be proactive and not reactive. Routine inspections to detect and address galvanic corrosion before it escalates into severe structural issues are always recommended. Partnering with a seasoned specialty contractor for annual roof, parking garage, and façade inspections will facilitate early detection and mitigate corrosion-related concerns,” says Rod O’Bannon, an expert in galvanic corrosion and Western Specialty Contractors region manager for the New York and Washington DC Metro Areas.
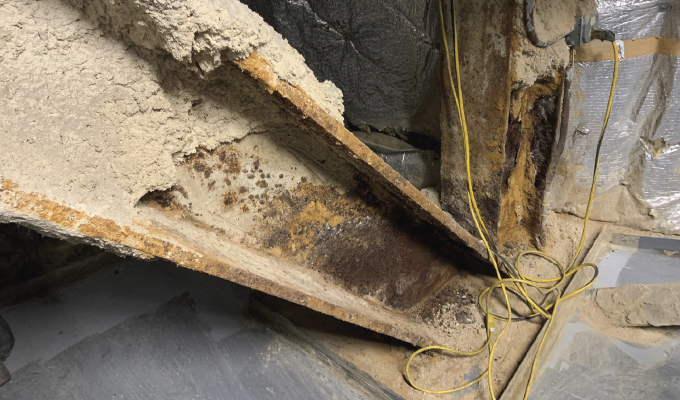
TIPS FOR PREVENTION
The separation of dissimilar metals should be the first step whenever possible between bolts, fasteners, and materials in general.
- Spacer materials like rubber, plastic, nylon, or neoprene can be interposed between metals to provide electrical insulation and minimize corrosion risk.
- Coating materials such as bituminous coatings, zinc-rich primers, epoxies, etc. may also be used to prevent or slow the galvanic corrosion process.
- The inclusion of zinc anodes within concrete repairs will serve as sacrificial anodes and take the brunt of the corrosion instead of the structural steel or reinforcement.
- Waterproofing systems are another great way to eliminate the intrusion of water and close the circuit required to induce galvanic corrosion.
- Installing induced current systems is also an option to help slow or halt the corrosion process.
- The use of stainless fasteners as a compatible alternative to traditional metal fastenings can halt the process.
Galvanic corrosion poses a substantial threat to the structural integrity of buildings; being aware of this during and after construction is key to avoiding future issues. Taking proactive maintenance and preventive measures is advised for any contractor, property manager, and/or owner to protect the integrity of their buildings and structures.
about the author
Rob Caputo is Western Specialty Contractors region manager for the New York and Washington DC metro areas. For more, visit www.westernspecialtycontractors.com.