The Sault Locks, in Sault Ste. Marie, Michigan, provide passage for an average of 10,000 ships per year, only shutting down during the winter months of January through March. Winters tend to be long and hard in the northern United States, so special consideration needs to be given to weather-related conditions. To help break up the ice that inevitably builds up on and in the locks, a set of air compressors are used to bubble up the water to break the ice. However, the existing air compressors needed to be upgraded.
Enter Brix Corporation, General Contractors and Construction Managers based in Livonia, Michigan, (Metro Detroit) the winner of the $12+ million project to build and house the new Sault Locks Air Distribution System. This system consist of three 800 hp air compressors capable of producing 6,500 cubic feet per minute of air velocity to create bubbles that break up the buildup of ice in the locks. The project takes place between the Poe and Davis locks (locks number two and three), which provide some unique jobsite conditions. Equipment that cannot be carried to the jobsite by hand needs to be barged through the locks to the site.
THE JOB
To perform the work needed for the new air distribution system, an excavation to a depth of 22 feet was needed. Tasked with this part of the project was Bacco Construction Company, based out of Iron Mountain Michigan, on the southern edge of Michigan’s Upper Peninsula. They called Pro-Tec Equipment looking for practical shoring solution for their task.
“When Bruce Nygrad [project estimator] from Bacco called, we set up an initial layout and design.” Recalls Josh Brown, Pro-Tec Equipment’s inside sales and Slide Rail Shoring specialist. “Through multiple conversations and design revisions, a final layout of the project was agreed upon. It was decided that Bacco would rent the Pro-Tec Equipment Slide Rail System, installing it in two distinct phases.”
Phase one would be a combination of two pits, a large cross brace pit, measuring 22 feet deep by 38.5 feet wide by 44.5 feet long and a multiple bay pit measuring 22 feet deep by 20 feet wide by 24 feet long, using the Pro-Tec Equipment Utility Panel Guide. Phase two would be a small pit, 22 feet deep by 20 feet wide by 15 feet long, again using the Utility Panel Guide.
THE RIGHT SYSTEM
The Pro-Tec Equipment Slide Rail System is a dig and push style system. With its modular, flexible design, the system can comply with a wide variety of shapes and sizes. Installed from the top down and removed from the bottom up, minimizing size of excavations, soil disturbances, restoration time, and cost. The installation is done with low vibration, providing soil support for excavations, adjacent structures, and existing utilities.
A cross brace system is a Slide Rail System that is multiple bays of panels wide by multiple bays of panels long. This space between them is spanned by using multiple roller beam assemblies that cross over and under each in the pit.
The Utility Panel Guide System, with its guide panels, allow existing utilities and structures to remain in place, while providing a safe and secure working environment for workers within the excavation.
THE PROBLEM
After having hauled and barged over 393,000 pounds of equipment to the jobsite. The crew for Bacco began to start the pilot cut for the Slide Rail System with their Cat 345 excavator. That is when the problem occurred.
“On the site plans, where we began digging, showed an electrical cable,” comments Matt Carpenter, project foremen for Bacco. “What we found was a concrete duct bank housing multiple, large electrical lines. Having this not show up on the plans not only changed how we would need to install the [Slide Rail] system, but we now had to come up with a way to support the duct bank that spans the entire width of the planned excavation. I called Pro-Tec Equipment right way and got on a conference call to discuss our options.”
THE SOLUTION
The conference call proved to be fruitful.
“After the conference call was completed, we all had an idea of what we wanted to do,” remarks Brown, “we confirmed our plans of using a large I-beam (waler beam) to support the duct bank the whole width of the system and how to maneuver and install Slide Rail panels above and below the duct bank with the engineer. Once we got the ‘OK,’ we got the equipment loaded and sent up to the jobsite the next day.”
THE RESULT
With all the major problems resolved, the Slide Rail System was able to be installed. As with many of Pro-Tec Equipment’s Slide Rail projects, a Slide Rail site consultant is sent to the project to aid crews with installing and removing the Slide Rail System in the fastest and safest possible way. For the Sault Locks project, the site consultant was Carl Leonard.
“I have been on a lot of different Slide Rail projects,” mentions Leonard, “but on this project, the horizontal change in soil conditions was a first for me. It (the soil) went from crushed lime stone, which was very hard until you broke the surface of it, to large sandstone blocks that were discarded to this location when the locks where built. Other than the soil changes and the duct bank situation, the job went really well. The Bacco crew was easy to work with; especially given that this was the first time they had used the Pro-Tec Equipment Slide Rail system.” ■
For More Information:
For more information about the Pro-Tec Equipment’s trench shielding and shoring equipment, call 800.292.1225, or visit www.pro-tecequipment.com.
_________________________________________________________________________
Modern Contractor Solutions, August 2013
Did you enjoy this article?
Subscribe to the FREE Digital Edition of Modern Contractor Solutions magazine.
Between The Locks
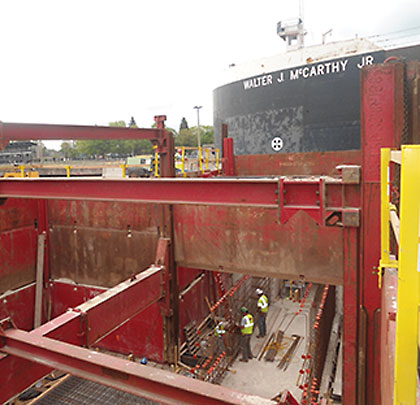