By Andrew Mayer
Originally, rivet busters were manufactured to cut and form metal rivets in building construction and dismantling, and industrial applications. At the beginning, rivet busters were quickly known for being a powerful and portable tool. Today, there remains a strong need for the tool, but not exactly what the tool was originally intended for.
Today, rivet busters have evolved and are primarily used for concrete demolition and dismantling steel girders on bridge projects. These versatile and portable tools can provide a lot of utility over the course of many years if maintained properly. These tools hit the ground hard, which can cause wear and tear if not properly maintained.
MAINTENANCE CHECKLIST
In order for contractors to keep the rivet buster up to its full potential, they should keep a maintenance checklist. For starters, follow this:
- Use a compressor of the right capacity (CFM)
- Blow the air-line down
- Properly lubricate the tool
- Only use clean, sharp chisels and points
For every shift, maintenance points a contractor needs to check over:
- Any damage to compressed air hose and couplings
- Proper lubrication of the tool
- Wear to the sleeves, bumpers, springs and tool steel shank
UNDERSTANDING PSI
The optimal pounds per square inch (psi) for most handheld pneumatic tools is 90 psi. Important production capacity is lost when pressure fails to reach more than 70 psi.
Low Pressure. Low pressure can be caused by a few different factors and could be a symptom of a larger issue with the air compressor, hoses or the rivet buster itself. Check for these three factors:
- The air compressor is unable to deliver the required air volume at the correct pressure
- Hoses and couplings choke the flow so much the pressure becomes insufficient
- Bad leakages in the systems
High Pressure. Conversely, and equally detrimental to a piece of equipment, too much pressure (over 100 psi) will quickly deteriorate bushings and other important components at a rapid rate. Over-pressurized pistons can also be damaged.
Dry Firing. Another common practice to prevent is dry firing. This puts a lot of unnecessary stress on the retainers and sleeves. Proper lubrication and going over the key maintenance points before every use will alleviate this issue.
CLOSING THOUGHT
Rivet busters are designed to work in challenging environments, but like any other machine, they need a preventive maintenance plan. Treating the tool with care and avoiding the most common operational errors enables the rivet buster to be one of the most reliable and versatile tools in a contractor’s toolbox.
about the author:
Andrew Mayer is the business development manager, light equipment at APT. APT Rivet Busters: APT closed-nose cylinder captivates the piston and adds an extra layer of safety. The tools offer a choice between two handle styles: pistol-grip style handle with outside trigger or classic “D” handle with inside trigger. Available in three stroke sizes: 6 inches, 8 inches, or 11 inches. For more, visit www.apt-tools.com.
Modern Contractor Solutions, June 2020
Did you enjoy this article?
Subscribe to the FREE Digital Edition of Modern Contractor Solutions magazine.
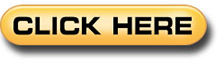