Harnessing the power to drive productivity
By Dan Heinemeier
The stats are becoming as well-known as they are grim. Since the 1960s, we’ve seen a doubling or better of non-farm labor productivity and efficiency in every sector except one: building and construction, where productivity has remained flat or actually fallen over the past 50 years. What we lose in this situation is more than just the opportunity to do better. Billions of dollars evaporate annually as nearly three-quarters of building projects come in over budget and/or are delivered late.
Thankfully, there is a growing chorus of voices offering innovative solutions to what McKinsey & Company has termed the construction productivity imperative. A 2018 Fortune magazine article, for example, highlighted the value of technological innovation, such as Building Information Modeling and virtual reality. Meanwhile, The Economist explored leveraging the public sector’s substantial clout to drive improvement.
But whatever tactical paths we choose to enhance productivity, our strategy will only be successful if it is grounded in a culture of continuous improvement that optimizes the whole, minimizes waste, focuses on process, and is centered around respect for people. Indeed, the best, quickest, and most reliable path to increased productivity is the broad-scale adoption of Lean principles and practices. For the past 6 years as the executive director of the Lean Construction Institute, I’ve seen firsthand—and through the testimonials of our more than 220 corporate members—how transformative this approach can be for projects, companies, and individuals alike.
ENHANCED COLLABORATION
At its core, Lean directly counteracts the organizational barriers unique to the construction industry that hinder productivity in the first place, eliminating information silos from project inception. Bringing together members from each sector in the early stages of a project leads to better designs and a better flow of information from the design team to the construction team, and on down the line. For instance, if project teams talk earlier about electrical gear, including loads and sizes of transformers and feeders, it allows the long procurement effort to start much earlier in the process. Even making decisions about lighting and hardware early on allows more time to ensure materials are available before they hold up the project in the final hour. There are a host of similar examples of better project outcomes that flow from a structured approach to enhanced collaboration early in the project lifecycle.
Other gains can come from observing and planning the work of each trade. The project team learns to see waste, to make direct observations of the work and any impediments to productivity—supplies piled in the way, materials too far from the install area, inefficient delivery schedules or practices, etc.—and can suggest adjustments. Initial resistance to what may seem like extra work is overcome when workers begin to see benefits that enhance ease, safety, and quality. And, when this is done for every significant project task, you begin to see real impacts across a project.
BENEFITS BEYOND THE JOBSITE
In many cases, Lean projects are completed well ahead of schedule, yielding benefits that ripple out far beyond the construction site. For instance, consider the hospital that was completed 2 months ahead of time. Not only did this allow the construction team to move on to other work more quickly, it became a huge benefit to an entire community, as Lean practices resulted in critical healthcare services being made available well before anticipated. In other successful cases, employing Lean construction techniques has meant that children and teachers get into new schools earlier, factories can get their products to market sooner, and companies can get their services into the marketplace faster.
Cost savings can be equally significant. Techniques like video studies enable analyzing specific tasks to determine how much time is spent on actual installation compared to waiting, walking, prep work, measuring, cutting, and material handling. This allows revisions to the process, helping to reduce waste and increase the time spent generating value.
On the business side, with the increased efficiency and higher work quality that comes from embedding Lean thinking into projects, companies tend to develop stronger relationships with client organizations and more repeat business. In some cases, customers are so satisfied with the progress on a current job that they award another project without the usual competitive bidding process.
THINKING LEAN
Though Lean construction practices have been most fully embraced by specific sectors, there is still ample opportunity to bring Lean design and construction to a wider range of projects, and to integrate it at a deeper level where it’s already being used. This means applying Lean thinking to how the building will be used to ensure the design meets all user needs. The highest-performing teams understand this—that is why they put together full-scale cardboard mockups and let people practice delivering their services so that they can see what pre-construction design changes can be made that will ultimately improve processes and minimize waste even after the building is complete. This thinking is beginning to take hold in office environments, too; for instance, insurance and financial institutions are embracing structured processes to help them think through the quality and design challenges of workspace and how it impacts customer satisfaction.
Ultimately, Lean helps to harness people’s innate desire to feel proud of contributing to a job well done—which includes helping others succeed, too. Better planning, open communication, and systematic elimination of inefficiencies all adds up to a smooth-flowing, less contentious performance process. Many teams even report experiencing the best F-word on projects: FUN! For owners and superintendents alike, this means they can move projects forward without spending their days firefighting suddenly urgent problems.
CLOSING THOUGHT
From the time an owner decides they need a new facility until the day they move in, Lean processes properly applied can lead to better outcomes in every phase, and a more productive design and construction industry as a whole.
About the author
Dan Heinemeier joined the Lean Construction Institute as executive director in 2013. A 30-year veteran of trade association management, his expertise includes strategic planning, new program development, and initiatives driving growth and ROI in associations. For more, visit www.leanconstruction.org.
Modern Contractor Solutions, September 2019
Did you enjoy this article?
Subscribe to the FREE Digital Edition of Modern Contractor Solutions magazine.
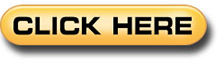