All construction delivery methods have characteristics that may make them appealing, depending on the project’s needs and the owner’s desires for cost control, schedule, and risk. It is important to note that, no matter what construction delivery method is selected for a project, the owner still maintains responsibility for costs and risk. A properly chosen project delivery method, along with a thorough, owner-friendly contract document, will help the project be successful.
IDEAL SOLUTION
One method that has emerged as the ideal solution in many cases is design-build. Design-build is a method to deliver a project in which the design and construction services are contracted by a single entity. In contrast to a more traditional approach (design-bid-build) that involves design, bidding, and then construction, design-build utilizes a single point of responsibility contract, which is used to minimize risks for the project owner because no matter the nature of the fault in the project, the contractor is responsible. While the traditional model involves the selection of a designer and a contractor that are often at odds, the design-build method changes the work sequence. Design-build serves to meet the longstanding wish by owners to have a single-point of responsibility in an attempt to reduce risks and overall costs.
In design-build, the owner hires a design-build company which handles the entire process—from the initial design through the construction of the project. This company is responsible for the design, construction, demolition, repair, or reconstruction of the project. The architect, general contractor, and all the specialty contractors are part of this integrated delivery system. With this system, the potential for construction problems can be uncovered early in the design phase.
A single price is quoted for the entire project. In this process the same parties are involved from beginning to end, so there is intimate knowledge of all phases of the project, allowing for smooth coordination of the process.
For example, on a traditional project, the design engineer may be paid a fee based on a negotiated percentage of the overall project cost or a flat fee, therefore giving very little incentive to meet the budget. In contrast, fees on a design-build project are established up front and if money is unused in a project, it is passed along as savings to the owner or the team, depending on the contract. Overall expectations are outlined in a more transparent manner and the owner has a lot more control over the project, while still benefiting from a single source of responsibility.
The method also offers the opportunity to reduce the duration of the project schedule as the design and construction phase of the project overlap. Simply, time is money. Using the design-build method gets the structure to the completion phase much faster, so it is available to be used as intended by the property owner. Parallel work shortens lead times. Although it isn’t a good fit for all projects, it should certainly be considered.
The method has gained great acceptance in commercial construction sectors during the last decade, and more recently it has made huge inroads with public officials as it has become legal by most states for infrastructure projects.
CLEARED FOR TAKEOFF
Fort Lauderdale–Hollywood International Airport (FLL) in Broward County, Florida, is a major airline hub, serving more than 23 million annual passengers. In 2003, the county began planning an expansion to meet increasing demands. This Airport Expansion Program covers a wide range of activities, including the extension of the southern runway, Runway 9R-27L, to accommodate larger commercial jet aircraft.
The project is designed to extend the boundaries of the airport by raising one of its runways up and over a major highway and rail line. One part will expand an existing 5,300-foot-long landing strip into a new 8,000-foot-long south runway that sits on a 60-foot-high, man-made embankment. Additionally, perpendicular to the new runway, two concrete bridge structures will separately support the new runway and taxiway. The runway support structure measures approximately 584 feet long and 800 feet wide, while the taxiway structure is approximately 422 feet wide and 724 feet long.
The Airport Expansion Program is using 1,732 D.S. Brown Versiflex™ Elastomeric Bearings—a total of 1,065 bearings for the runway structure and 667 bearings for the taxiway structure. In general, D.S. Brown’s Versiflex™ Elastomeric Bearing Assemblies can be custom-molded using neoprene or natural rubber, and they can be non-reinforced, laminated, or sliding bearing assemblies.
As a design-build project, the D.S. Brown Engineering Department needed to coordinate extensively with the structural designer in order to ensure proper design, fit, and function of the bearings with the rest of the structure. On January 7, 2013, D.S. Brown started molding bearings, and on January 25, 2013, D.S. Brown was released for full production on all the runway bearings.
Since a great deal of time was spent in the design stage, the production schedules were extremely tight. A well thought out, detailed production plan was necessary. The D.S. Brown operations team and supply chain manager kept on top of the orders to ensure that the steel, Teflon, and stainless steel were received in a timely manner.
The majority of the runway bearings are Type 4 mobile bearings. The project required 805 bearings in a very short time frame, so all areas of production had to be on track. This included machining, shim cutting and prep, load build, molding, vulcanize patching, load testing, cutting and dimpling of Teflon, epoxy bonding, stainless steel shearing, stainless steel welding, and metalizing.
The construction on FFL is ongoing and scheduled to be completed in September 2014. ■
For More Information:
Founded in 1890, The D.S. Brown Company manufactures an extensive product line providing solutions for the most challenging infrastructure applications. Its high-quality engineered products are available worldwide for new construction and rehabilitation of bridges, highways, airfield pavements, and parking structures. Visit www.dsbrown.com for more information.
_________________________________________________________________________
Modern Contractor Solutions, March 2014
Did you enjoy this article?
Subscribe to the FREE Digital Edition of Modern Contractor Solutions magazine.
Benefits of Design-Build
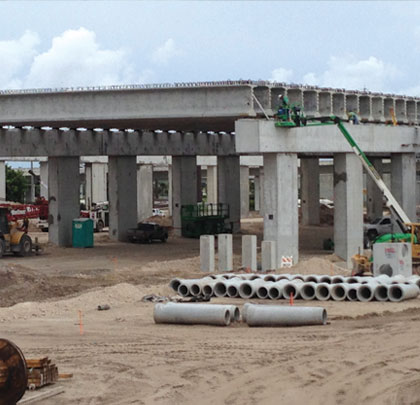