There are many routine maintenance tasks that fleet maintenance professionals perform every day, and changing oil is arguably the most important and frequently performed of them all. Fresh oil better lubricates and regulates the operating temperature of the engine, thus protecting the most expensive internal piece of most construction vehicles and equipment. Changing oil is a tedious and messy task that is time consuming, poses a health and safety risk to the technician, a risk to the environment, and introduces the potential for technician error like stripped oil pans or cross threaded plugs.
DEALING WITH CONTAMINANTS
Maintenance manuals always recommend bringing the engine to normal operating temperature before changing the oil. The benefits of changing hot engine oil is that the oil becomes more viscous allowing waste particles, that may otherwise find themselves at the very top or bottom of cold waste oil, warmly suspended in the hot oil and properly eliminated along with the hot engine oil when it’s drained. Hot oil flows freely, and quickly, allowing for the most effective and complete oil change.
Oil contaminants enter oil through a variety of ways, the most common being metal shavings released from the engine during regular wear and tear. Having these shavings circulating through the engine causes slight abrasions that can cause significant engine damage over time. Another source of contamination is a host of debris that sneaks in past the air intake. Additionally, combustion byproducts are a naturally occurring waste particle as a result of a regular running engine. Although unavoidable, the damage caused by these contaminants can be reduced by regular hot oil changes.
CAUTION WITH HOT OIL
Although hot oil changes are preferred, they are not with not without their faults. The running temperature of an engine is extremely hot, and touching a hot oil drain plug or pan can cause severe burns to a technician’s skin, even through gloves. Hot waste oil flows quicker and is more prone to splashes and spills, creating an opportunity for environmental damage in the field or creating a mess in the shop. Furthermore, as metal is heated, the oil pan and drain plug expand, making traditional drain plugs difficult to remove, increasing the chance of crossing threads or stripping an oil pan, resulting in an expensive repair.
SIMPLE, SAFE SOLUTION
A simple solution that pays for itself is using a No-Spill™ oil drain product that keep maintenance technicians safe, protects the oil pan threads, and keeps the waste fluid contained, thus eliminating burns and spills while allowing the hottest of oil changes.
The No-Spill Systems drain plug replaces the existing oil drain plug without the need of special tools or fittings to install them. It is a simple two-minute installation: just remove the old drain plug, clean equipment threads, thread in the No-Spill Systems plug by hand until snug, and finally tighten the No-Spill Systems plug to torque specs. The No-Spill drain plug contains an internal valve that, once activated by the drain tool, lifts to allow the quick, clean, and safe draining and transfer of fluids.
No-Spill Systems is an American-made clean oil drain plug that allows for the clean drainage and transfer of waste fluid while protecting technicians from hot oil pans and other potential risks. No-Spill Systems has been in the business of fluid draining technology for more than 30 years, manufacturing the highest quality products that make changing fluids easier, safer in addition to helping our environment by preventing oil spills.
ACCOMMODATES FLEET NEEDS
No-Spill Systems offers three different system designs to accommodate many different types of fleets and their unique waste fluid needs. The Standard Design drain plug is the most commonly used style of drain plug. Once installed, it stays in the oil pan and requires a thread on No-Spill drain tool to drain the oil. The Compact Design drain plug design is a low-profile version that is used where space may be an issue. The Compact design plug also has its own unique a thread-on drain tool. The third product is the Speed Click™ design drain plug. It is a quick connect version where the drain tool connects to the plug in much the same way as a hydraulic quick connect fitting would; clicking on and clicks off for the ultimate speed and efficiency. All three product designs are compatible with both gravity and suction draining, and will reduce spills and save valuable time and money.
GOOD ON MANY FRONTS
Many industries are embracing environmentally responsible behaviours, and supporting products that promote their sustainability and safety goals. No-Spill Systems strives to help minimize these environmental and health concerns in the construction industry. By using No-Spill Systems for changing oil or transferring fluids, maintenance teams are saving time and money by eliminating costly spills and stripped oil pans. They’re also improving their engine life and performance of their equipment by draining the oil hot. They’re avoiding costly cleanup costs and caused by unnecessary oil spills, and reducing health and safety issues caused by burns from handling hot engine oil.
SUMMARY
No-Spill Systems produces more than 500 different sizes of drain plugs to fit all types of equipment and applications such as engines, transmissions, hydraulic systems, and radiators. No-Spill’s sales team has product specialists with decades of experience in fitting the exact thread pitch for all types of equipment in every unique fleet.
As the longest running drain plug company in the world, No-Spill Systems uses exclusively American-sourced materials and manufacturing to the strictest engineering tolerances. No-Spill drain plugs have the most accurate thread pitch, magnets that are designed specifically to endure the high temp/cooling cycles of an engine, and a hex design that makes our drain plugs exceptionally easy to install. No-Spill products are the perfect solution for companies looking for a faster, cleaner, and safer way to change fluids.
For more information:
For more than 30 years, No-Spill™ Systems, the drain plug professionals, has been supporting its network of more than 2,000 dealers throughout North America and South America. Using the best quality brass in the world (Ohio brass), all No-Spill Systems plugs and accessories come with lifetime warranties on all parts and workmanship. For more information, visit www.nospillsystems.com.
Modern Contractor Solutions, January 2019
Did you enjoy this article?
Subscribe to the FREE Digital Edition of Modern Contractor Solutions magazine.
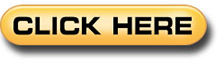