On a recent project to expand H.L. Sonny Callahan Airport in Fairhope, Alabama, contractor John G. Walton Construction Co. was given 280 calendar days to clear, grub, excavate, level, compact, and grade the 250-acre site, then create a complex storm drainage system. All of which was simply a precursor to constructing a series of new taxiways and aprons. With that roughly 9-month window ever looming, several record-breaking rains conspired to worsen matters.
While a scenario like that might wreak havoc on the timelines of many other companies, Walton’s team, staunch proponents of GNSS technology for nearly a decade, took it in stride. Using the machine control solutions which had always served them, the company has overcome those obstacles and is today looking at an on-time—possibly even early—completion.
BOOM TIMES IN BALDWIN
Improvement and expansion work at the Sonny Callahan Airport was brought on by significant growth in Baldwin County, the larger area that includes the airport’s Fairhope, Alabama, location.
“This is definitely a growing region, so the airport has seen an increase in traffic over the years,” says Dewayne Anderson, Walton’s project superintendent. “This area is convenient to Mobile, to Gulf Shores, to Pensacola—it’s central to all of them.”
The $3.1 million construction effort began in October, 2016, and is the third phase of ongoing expansions and upgrades which will open up the eastern portion of the airport property to future expansion and development. In fact, the airport already has commitments for large hangers to be built as soon as runway access is available.
EAST SIDE STORY
Work on Phase 3 of the expansion began with a clearing and grubbing of the entire site being developed, followed by a sizeable earthmoving effort. Anderson says that, while the majority of dirt was moved around onsite, there was still a decent volume of soil being imported from a nearby pit.
“We have six trucks working the airport job, and on 10-hour days, we are averaging about 150 loads per day,” he says. “So, that’s about 3,000 yards of dirt being placed in 12-inch lifts; in all we will be bringing in about 150,000 cubic yards of soil. For every 1,000 yards we put in, we need to have a density test performed and the area has to compact to 98 percent or higher. Similarly, moisture content, which can vary depending on the area of the pit the material comes from, can be no higher than 14 percent.”
While there has been a fair amount of cutting needed onsite—more than 13,000 yards of soil was moved to create a drainage levee, for example—getting the project to grade has largely meant dealing with some extensive fill areas. In some parts of the job, depths ranged anywhere from 5 feet to 13 feet of fill. “And, again, every 1-foot lift had to be followed by compaction and testing,” says Anderson.
INTELLIGENT CHOICE
Though there are no utilities to be installed on this particular facet of the job, Walton is handling construction of an impressive drainage system, several retention ponds, and more. Placement and movement of all that soil is being handled by a single Komatsu D51-PXi intelligent dozer.
“We are fortunate, as a company, to have invested in GPS technology back in 2009,” says Anderson. “And since then our Topcon dealer, Earl Dudley and Associates, has been great in seeing that our needs are always met. They helped us first make the transition to the new technology back then and have always kept us abreast of changes as they’ve become available. All that effort is paying off in a big way out here. The amount of staking we would have needed on the retention ponds alone could have been extremely time-consuming. Instead, the Komatsu dozer, equipped with Topcon 3D-MC2 machine control, did it all.”
To verify grade, Walton’s crew conducted periodic checks using a Topcon HiPer SR base/rover and Tesla data collector (also from Topcon)—finding elevations to be dead-on each time. According to Anderson, their operator, Carl Paul, was apprehensive at first about making the switch from a traditional grading approach to one that used GNSS technology. “But within 2 days he had really taken to it, learning the vocabulary, getting comfortable with the system and the format,” he says. “After that, it was a whole different world for him. He no longer had to wait for me to stake out in front of him or verify that I had something right. Everything was laid out for him on screen and he could just keep moving along. For us, the 3D-MC2 system took the performance of an already-good finish operator and made it even better.
AFTER THE DELUGE
Seasoned professionals like John G. Walton Construction are adept at coping with just about any eventuality in business. There are some things, however—like weather—that are simply out of their control. Late in 2016, as the airport job was in its early stages, Mother Nature threatened to mess with progress on the job, dropping massive amounts of rain in a short period of time.
“We had about 8-inches of rainfall in a couple of days—a lot even by this region’s standards,” Anderson says. “That series of storms flooded the pit from which we were getting material pretty bad. So, our hauling effort was halted for several days while we waited for things to dry out. And that wasn’t the only time, either; in one 65-day stretch, we lost about 15 days of hauling due to rain. That can put a serious hit on a schedule for most companies.”
Anderson is quick to point out however, that they are not “most companies” and that having a GNSS capability was key to keeping things on track.
“Previously, on rainout days when it was too wet to haul, we’d use a transit and rod to set grade stakes, trying hard to stay ahead of our fill crew. Now, because machine control has virtually eliminated all staking, we can perform other tasks in that ‘down-time,’ including using it for layout work. We regularly use the system to determine edge of asphalt, shoulder, etc.—even lay out a 4-acre retention pond—and do so very accurately.” ■
About the Author:
Larry Trojak is president of Trojak Communications, a Minnesota-based marketing communications firm. He has written for the construction, recycling, demolition, scrap, and aggregate processing industries.
_________________________________________________________________________
Modern Contractor Solutions, October 2017
Did you enjoy this article?
Subscribe to the FREE Digital Edition of Modern Contractor Solutions magazine.
Beating the Odds
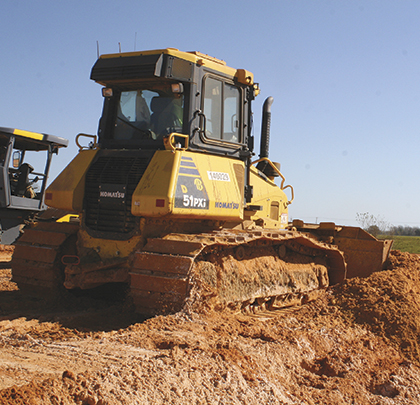