Innovative water tanks minimize financial and safety risks
By Josh Swank
Successful contractors know multiple factors contribute to their profitability, from minimizing their trucks’ cycle times to ensuring their crew’s safety. Even support equipment, such as water trucks, can’t escape their analysis—or at least they shouldn’t.
How equipment operators haul and apply water can significantly impact overall productivity and safety. Though water trucks appear basic in application and design, several factors have a significant impact on efficiency, from the challenges of water movement in the tank to the steel used in the tank’s construction. All of these factors impact uptime, maintenance, efficiency, and safety. The key to a productive and safe solution lies within the truck’s water tank design.
HIP TO BE SQUARE
Rounded water tanks are the most common. They get the job done, but not without challenges. The tank’s curved sides raise the water’s center of gravity, making the truck less stable when navigating haul roads. To mitigate instability, operators often avoid filling their tanks completely. This means they need to refill more frequently, contributing to added downtime and increased fuel consumption as they backtrack to the water source.
Additionally, rounded tank designs contribute to water churning since there are no corners, edges, or obstructions to slow the water’s momentum. This constant, and sometimes rapid, water movement poses a safety risk for the driver and people nearby since the water can shift the center of gravity and cause the truck to become unstable.
Alternatively, water tanks with square corners minimize churning and have a larger capacity by simply not rounding off the sides of the tank. They also maximize productivity and operator safety due to their box-shaped structure, water baffles, and water metering systems. The design also lowers the unit’s overall center of gravity, enhancing stability and allowing drivers to safely fill the tank to capacity. The box-shaped structure makes it possible to haul about 20 percent more water than rounded tanks, resulting in considerable time and cost savings.
BAFFLINGLY HIGH SAFETY
A water tank’s internal baffling system is another key element that affects safety and efficiency. Baffles inside the tank help minimize water from surging side-to-side and front-to-back. Almost all water tanks feature baffles, but many have large holes cut out to provide maintenance personnel access to the individual compartments. These openings allow water to surge between compartments, limiting surge protection and increasing the risk of the truck tipping or being involved in another type of accident.
To minimize surging, some tanks feature sophisticated water control systems that use baffling that runs from floor to ceiling as well as along the complete length and width of the tank, resulting in full compartmentalization of the water. Within the outer compartments, some manufacturers install side-surge stabilizers along the walls to prevent water from rolling or churning. The number of compartments can vary between tanks.
To offer the best level of water compartmentalization, these baffles require holes to allow water to flow freely throughout the tank, but they need to be small enough to prevent water from surging during use. To address this, some water tanks feature access doors that are about as tall as an average-size worker to provide a more advanced solution than simply a hole near the ground in the baffle walls. These baffle doors, which technicians walk through easily, practically eliminate the need to crouch down while they maintain the tank, and the doors remain shut while the water tank is in operation. With access between multiple compartments, technicians have minimal concerns about working in confined spaces.
To allow technicians into the tank for maintenance, some manufacturers incorporate external doors, which can provide fresh air and natural light throughout the tank after opening all of the external and baffle doors.
LET IT LOOSE
Having complete and easy control over their tank’s water output gives water truck drivers control over their safety on haul roads. For instance, individually controlled spray heads help water truck drivers optimize their water usage as well as minimize the chance of oversaturating haul roads, which can create slick driving conditions. Inside the cab, operators can turn on the individual spray heads—and in some systems, program a spraying interval. This optimizes water usage, so operators cover more surface area with minimal risk of making haul roads too slick for other equipment. Additionally, the added control and metering means they spend less time backtracking to a wellhead than a truck with a traditional water tank control system.
CLOSING THOUGHT
The unsung hero of any dusty jobsite or quarry is the water truck. Controlling dust is as much as an environmental issue as a safety issue. Dust control measures help meet safety, health, and environmental requirements and apply to any jobsite where there is the potential of airborne pollution traveling across the site and out of the boundaries of the project. Keeping the dust down via water spray reduces emissions and protects employees.
About the author
Josh Swank, vice president of sales and marketing for Philippi-Hagenbuch, oversees the aggregates, refuse, and mining industry sales group. Celebrating its 50th year in business, Philippi-Hagenbuch Inc., located in Peoria, Illinois, has been building equipment for off-highway haul trucks since 1969. For more, visit www.philsystems.com.
Modern Contractor Solutions, August 2019
Did you enjoy this article?
Subscribe to the FREE Digital Edition of Modern Contractor Solutions magazine.
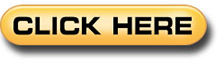