By Larry Trojak
On a jobsite in Abbottsford, British Columbia, about an hour from Vancouver, a bit of construction equipment history is being made. There, an excavator is trenching for utilities in support of a new industrial park. While that is obviously not trailblazing, the fact that the machine doing the trenching has been equipped with a GNSS-based automatic excavator system—the first in a utility application in Canada—is. The company heading up the project, Regehr Contracting, reports that using the new solution has already helped them realize significant savings in time, manpower, and material, and sees a wealth of uses for it as they move forward. The results, at the risk of yielding to an obvious play on words, have been truly groundbreaking.
UTILITY PLAYERS
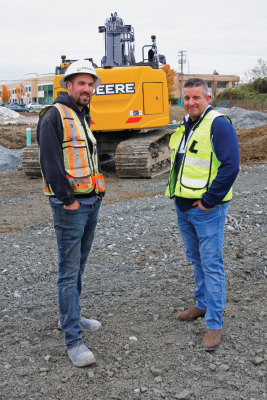
Despite its current position at the forefront of cutting-edge technology, Regehr Construction’s roots are humble ones. When Kenton Regehr first started his company, he was focused on hourly work; digging house basements and performing miscellaneous agricultural projects. Since then, the company has evolved into one with more than 50 people, four separate divisions, and a breadth of expertise in everything from demolition to mobile aggregate processing to stream restoration and more. One of those strengths is in utility installation, which is where the new solution was introduced according to James Cucheran, one of Regehr’s supervisors.
“Our civil/residential group handles this type of work,” he says. “The site, a 2-acre parcel located on Great Northern Avenue in Abbotsford, will be the home to three different tilt-up structures—all part of a future industrial complex. We were installing roughly 300 meters of storm, sanitary, and water services for the complex, a process that can be tricky for accuracy at times and almost always involves two men in addition to the machine operator.”
The traditional approach to which Cucheran refers starts with a surveyor laying out the direction of travel for the utility by either spray painting a line on the ground or using a theodolite to make certain the excavation is maintaining the proper line. Then, once excavation begins, a rod man must also be present in the trench to ensure a proper and accurate grade on which aggregate will be placed and the pipe will set by another worker. A visit from Cory Luck, territory manager for Brandt Positioning, made them aware that an ability to trim that workforce—while at the same time improving efficiency and accuracies—could be possible with an X-53x Automatic Excavator system from Topcon Positioning Systems.
“Regehr was already a customer of ours for other GPS technology and they were looking at machine control for the excavation facet of their projects,” he says. “I showed them what the new solution could do for them and they just happened to have the Great Northern job coming up. The timing could not have been better.”
NEXT STEP EXCAVATION
While machine control for excavators has been around for a while, the control they provide has typically been limited either to showing where the operator’s bucket is (an indicate-only system) or directly targeting grade via a digital model, onboard sensors, and an in-cab display (3D GPS). The system that Regehr added to its John Deere 345G takes that control to the next level, presenting the operator with an option to let the machine do the excavation itself—once again based on a digital model.
“Our interest in the Automatic Excavator system was based on the promise of what we felt it could do for us,” says Cucheron. “The fact that it could reduce the size of our trenching crews was attractive, as was the accuracy it could deliver—both in direction and depth. When placed in ‘Auto’ mode, the system is designed to automatically excavate down to the grade that is loaded into the model—no more, no less. My operator can cut his subgrade and be consistently within 1 to 2 centimeters without anyone needing to check it with GPS or a laser behind him. So, between that and the streamlined layout function, we can now use that rod man and one surveyor elsewhere on site.”
Minimizing material overages was a benefit from the new solution that Regehr had not foreseen, but it has already proven to be the case. According to Cucheran, that, too, stems from the system’s ability to get material to grade quickly and accurately.
“Being able to set grade in aggregate for our pipe has been a huge difference,” he says. “In Auto mode, my operator can get a perfect grade every time, so the gravel savings is substantial. We’ve found that we can save about 10 tons of material on a 100-meter stretch. At today’s prices for aggregate, those savings can be substantial.”
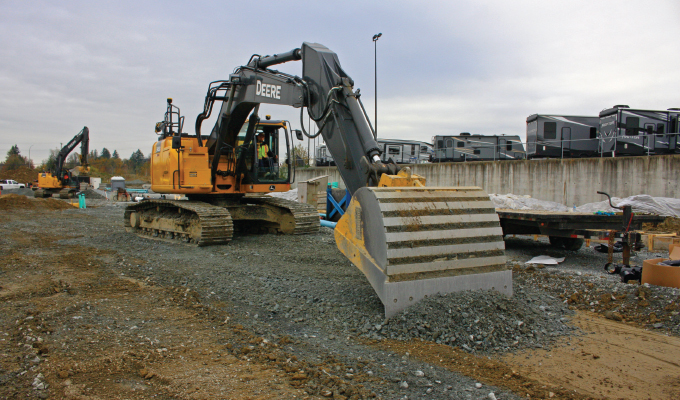
A LEARNING EXPERIENCE
The unique nature of the new solution is evident right from the calibration phase in which a robotic total station, working through a tablet- or PC-based app, tracks a prism located behind the machine’s antenna and measures the various positions of the machine. The process is designed to improve the unit’s accuracy.
The total station and the geometry app are both connected directly to the system’s controller. Each time the operator measures a point during calibration, it is stored directly into the machine, eliminating the need for retyping. Using the total station, accuracies to .05 centimeters can be gained in automatics. In addition, the calibration app for the valves also connects to the controller and brings a machine-learning capability to the calibration.
In that last scenario, the operator performs some movements with the machine—bucket out/bucket in for example—enabling the system to learn how to react to and calculate for different circumstances. After three or four calibrations, it will average that feedback data and know how to react to different conditions such as hard soil, soft soil, etc.
Despite all the complexities taking place inside the system, getting up to speed with the new solution was no problem at all, according to Regehr’s operator, Derek Molnar.
“Prior to getting the new system on this machine I had no real GPS machine experience—I’d only used a data collector,” he says. “But it was easy to learn and, despite being a little leery about the newness of it all, I got to love it very quickly. The fact that I don’t have to wait for anyone else is a huge plus for me. Most mornings I’m in the machine and working while the other guys are still getting tools. I’m probably 30 percent more productive with the new solution—this is a whole different realm of operating.”
EFFICIENCY ON A STICK
Regehr’s move to the automated excavator system was made simpler through the addition of custom—and customizable—joysticks, which place complete functionality of the system literally at the operator’s fingertips.
“The joysticks make it much easier to operate because all the buttons for automatic operation are on top,” says Brandt’s Cory Luck. “They can get the bucket into a certain position and lock it and it will stay at that angle, or they can set it to follow the design, match grade, and so on. The bottom line is that, in automatic mode, the machine is doing the bulk of the ‘thinking’ for the operator and they’ve taken to that nicely.”
CLOSING THOUGHT
Regehr has taken nicely to a whole lot it seems. Since going all-in with the new system, they’ve dedicated an in-house person to build their digital models; they are considering a second GNSS excavator system and see the automatic system playing a key role in other projects as they move forward.
“Obviously, we know it excels in utility work like this,” says Cuchern. “But we can see it performing well in other areas such as bulk excavating, site preparation, fine grading for asphalt in front of the grader, curb prep—the possibilities are endless and Brandt has been great in helping us get up to speed. We’re not the biggest player in the Vancouver area, but this was a huge step for us. The advantages the new technology brings will allow us to bid projects more competitively than ever before, which bodes well for future work.”
About the author:
Larry Trojak is president of Trojak Communications, a Minnesota-based marketing communications firm. He has written for the construction, recycling, demolition, scrap, and aggregate processing industries
Modern Contractor Solutions, March 2020
Did you enjoy this article?
Subscribe to the FREE Digital Edition of Modern Contractor Solutions magazine.
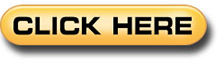