A pioneer in atomized mist technology helped a government contractor comply with strict military concrete quality and dust emission standards during the construction of an airfield tarmac. By providing a consistent humidity level in a high-heat desert environment, the DustBoss® DB-30™ (manufactured by BossTek) helped Southwest Concrete Paving Company (SWCP) maintain the proper moisture levels needed for high-grade concrete production. In addition, the mobile misting cannon offered dust suppression during the demolition of the previous tarmac and storage of dusty material. The result of the 9-month, multi-phase contract was a premium quality 87,000-square-yard concrete tarmac that passed inspections the first time while adhering to all workplace dust standards throughout the project.
PROPER CONCRETE CURING
The consequence of not meeting the required standards can be ripping out entire sections of the project to create a compliant product. The lifecycle of a normal road is 15 to 20 years, whereas the lifecycle of an airstrip apron is 40 to 60 years. Due to the point loads of jets and other aircraft, proper curing is critical, thus engineers meticulously test for slump and moisture content every step of the way.
Paving crews in arid conditions generally work through the night to control surface temperature and slump. Critical factors include ambient temperature, concrete temperature, wind speed, and humidity. As the concrete mix temperature increases, slump will decrease approximately 0.8 inches for every 20-degree Fahrenheit rise in temperature.
“The night temperatures fluctuated, but often remained above 80-degrees Fahrenheit,” explains David Rath, QCQA manager for SWCP. “In those conditions, the relative humidity across the curing slab has to consistently stay above 40 percent. If the surface conditions aren’t precisely controlled, the concrete surface will be prematurely exposed to tensile stresses that it cannot withstand before the hydration of the cement has passed a certain stage. This causes small cracks known as plastic shrinkage, which can significantly reduce the life of the concrete.”
PRECISE MOISTURE CONTENT
Once the sun went down, the atomized misting cannon was moved to the front of the paving machine to lay an even surface of moisture across the base layer. When pouring, the moisture content of the concrete mixture is precise, but the dry ground can draw the moisture out of the meal, increasing the chances of cracking.
Due to the need for mobility, SWCP secured the DustBoss DB-30 to the back of a flatbed truck with a 250-gallon water tank and a portable generator to create a completely mobile and autonomous unit, designed for conditions that lack adequate access to water and power.
The water cannon could be removed and placed on a hydraulic forklift as high as 40 feet in the air. This allowed improved targeting of the atomized mist sprayed over and around the newly poured concrete to provide the humidity and surface moisture needed for proper finishing. Using the variable height and the DB-30’s adjustable 0- to 50-degree vertical angle settings, operators were able to control the humidity levels and coverage area, while compensating for wind.
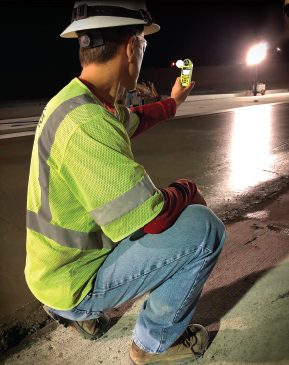
EVENLY DISTRIBUTED DROPLETS
Water from the tank is forced through a circular stainless-steel manifold with 30 atomizing spray nozzles at the front of a heavy-duty cone-shaped barrel design. A powerful 7.5 hp fan at the back of the cannon, producing 9,200 cfm of airflow, launches millions of tiny droplets in a 100-foot cone. With 180-degree horizontal oscillation, the unit has a coverage area of 17,000 square feet. Using only 9.8 gpm of water, the unit raises the humidity of an entire area with evenly distributed droplets between 50 to 200 microns in diameter (approximately the size of fine dust), while minimizing pooling or runoff.
The unit is designed to be set up by a single worker and operated autonomously without further attention. Able to be operated by remote control, the DB-30 also has a touch screen panel for adjusting the settings (oscillation, pump settings, etc.). The panel is encased in a NEMA 3R cabinet to protect it from the harmful elements of outdoor operation such as dust, rain, and contaminants.
ADJUSTABLE TO THE JOB
The mobility and adjustability of the DB-30 allowed crews to reposition and recalibrate the settings of the atomized mist cannon to raise the humidity above the paved surface and prevent water from being sheared away by high winds.
“Some of the wind conditions would have stopped construction cold in the past,” says Rath. “Positioning the DustBoss upwind, allowing the air to carry the humidity with it, kept us up and running on several occasions. Otherwise, we might have had to go back, rip out what we poured, and start again.”
Wrapping up the finishing touches of the project, core samples of the concrete taken by inspectors demonstrated high quality, with no compliance issues. The meticulous planning, technical skill of the staff and use of modern technology allowed SWCP to complete the project on time and on budget with no major downtime.
CLOSING THOUGHT
The atomized mist technology has proven to be applicable across several segments within SWCP’s business, from road construction to military and public airports. Enhanced control over the finishing process helped improve the outcome and extend the life of the finished product. This attention to detail and quality has become a hallmark of SWCP projects.
For more information
BossTek is a global leader in dust and odor control solutions for the storage and handling of clinker, petcoke, coal, rock and aggregate, as well as controlling air quality during port unloading, recycling and scrap processing, mining, earth moving, and construction demolition. For more, visit www.bosstek.com.
Modern Contractor Solutions, May 2020
Did you enjoy this article?
Subscribe to the FREE Digital Edition of Modern Contractor Solutions magazine.
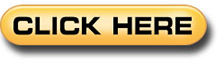