The National Asphalt Pavement Association (NAPA) and the Federal Highway Administration (FHWA) held their first survey of asphalt mix producers in 2009. At that time, mix producers only used accepted reclaimed asphalt pavement (RAP) in 56 of the 67 million tons of mix. The U.S. had not yet standardized warm-mix asphalt (WMA) pavement. As NAPA gained more WMA research, it began pushing for WMA as a standard. The survey numbers changed drastically from 2009 to 2013, possibly due to NAPA’s push combined with the need for safer working conditions, safer environmental products and processes, and a more sustainable product. In 2013, mix producers used 67.8 of the 71 million tons of RAP in asphalt mixtures and 106.4 million tons of WMA were used overall; an increase in the use of WMA greater than 533 percent from 2009.
ASPHALT INDUSTRY PAVES THE WAY IN RECYCLING
Recycling asphalt pavements at a rate of over 99 percent, the asphalt industry is the U.S.’s number one recycler. In 2013 alone, the U.S. saved $2 billion by reclaiming and reusing RAP and RAS (recycled asphalt shingles). Companies aren’t just recycling asphalt, though. Also on the recycling list are ground tire rubber, steel and blast furnace slag, glass, and foundry sand. In 2013, U.S. companies used about 1.2 million tons of these materials in more than 6.6 million tons of asphalt pavement mixes. “Now we are looking to focus research and engineering on using warm mix in combination with greater levels of recycled materials to make our long lasting, high-performance asphalt pavements even more sustainable,” says NAPA president, Mike Acott.
WHY WARM-MIX ASPHALT IS A COOL COMMODITY
Numbers don’t lie. Mix producers clearly have something good to say about WMA pavements. Even NAPA is backing WMA and warm-mix thin asphalt overlays as though they’re going out of style. The name of the game here is sustainability. In an October press release, NAPA chairman and president of Maryland Paving Inc., Bill Ensor, states, “The use of warm-mix technologies, as well as recycled materials, helps us improve both the quality and sustainability of asphalt pavements. Furthermore, warm-mix technologies and recycled materials combined with the ability to engineer asphalt mixes save not only money, but product as well.”
Recycling and sustainability—those are part and parcel of the WMA package. But what does WMA mean for the environment? To start, WMA uses less energy to fuel the burners than hot-mix asphalt (HMA), reducing fossil fuel consumption. WMA production emits less carbon dioxide than HMA because of the lower temperature at which the mix is produced, which reduces its carbon footprint. Of course, increasing recycled materials used in the mix will decrease use of virgin aggregate.
WARM MIX IS SAFER FOR WORKERS
Another major benefit of working with WMA is the reduction of both production and placement temperature. This means lower hazardous chemical emissions, reducing worker exposure to asphalt fumes both at the plant and during construction. Workers can rake and compact WMA easier because of the lower temperatures. Less fatiguing conditions leads to a less hazardous work environment. There is also the possibility of increased profitability, depending on whether the worker can safely perform extended amounts of work.
FOUNDATION OF INFORMATION
There are certain wells of information from which a curious individual can pull; NAPA’s research being one and the European Asphalt Pavement Association (EAPA) being another. Europe has been engaged in the WMA setup for a handful of years more than the U.S. and NAPA’s findings are in agreement with EAPA’s. The research is clear—WMA is more sustainable, more industrious in the recycling department, better for the environment, and safer for workers than HMA. ■
For More Information
For more information about asphalt pavement, visit NAPA’s website: www.asphaltpavement.org.
Modern Contractor Solutions, December 2014
Did you enjoy this article?
Subscribe to the FREE Digital Edition of Modern Contractor Solutions Magazine!
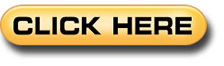