Working smarter with compact loader technology
Product development and technological advancements are making today’s worksites more efficient and productive, but only if the right equipment is used in the most intelligent way. Bobcat Loader Product Specialist Mike Fitzgerald discusses how to increase work potential with new loader technology.
[h2]SIMPLER OPERATIONS[/h2]
New usability functions are making compact loaders more sophisticated and intuitive. “New control options are allowing owners to match operator preferences to jobsite needs. Joystick-type controls are quickly becoming a popular category of controls for their ability to put loader maneuverability and attachment commands at your fingertips,” says Fitzgerald. “Operators of all ages are gravitating to them because they provide enhanced functionality with less fatigue.”
Some of these controls also have built-in features that manage horsepower, so operators can match engine torque to the specified workload for increased efficiency. “Such systems also allow operators to manage their travel speed for more precise control of the machine,” says Fitzgerald. “For jobs that involve multiple operators, many manufacturers’ control patterns can alternate between ISO and H-Pattern hand controls to match a particular operator’s preference, which also plays a key role in maximizing comfort, efficiency, and profitability.”
[h2]INSTRUMENTATION MAKING LIFE EASIER[/h2]
The incorporation of simple-to-use instrumentation inside the loader cab lets operators monitor activities from diagnostics and major loader functions to more in-depth machine and operator performance metrics. “Some current instrumentation systems can capture user data and statistics that allow job productivity and resources to be precisely calculated for each operator. For example, some loaders now offer mechanisms that track individual fuel usage, real-time fuel consumption, and idle time intervals,” says Fitzgerald. “With this data, owners and fleet managers can assess a particular type of job and more accurately estimate what aspect of a job requires more fuel. If used routinely, it’s also a tool that can help owners manage labor discrepancies.”
Machine diagnostic and management technologies can also be integrated into some instrumentation systems to monitor engine temperatures and pressures, along with attachment productivity. “For instance, operators can consult their display panels to view job clocks, and cumulative hour meters can compute usage on high-output attachments, such as planers and wheel saws,” says Fitzgerald. “Certain systems can also equip owners to track parameters like bit life, maintenance, and total life of an attachment to assist with future purchasing or rental decisions.”
Another benefit of instrumentation systems is their ability to help owners minimize the risk of loss due to theft or unauthorized use of a machine. Security features of many loader control technologies include the use of a numeric keyless pad. “Only operators with pre-assigned passwords can start and run the machine,” says Fitzgerald. According to the National Insurance Crime Bureau, U.S. business owners lose $3 million in stolen compact equipment daily. The use of keyless start systems may secure discounted insurance premiums on certain coverage plans.
[h2]REDUCING CARBON FOOTPRINT[/h2]
Compact loader manufacturers continue to take steps toward complying with Environmental Protection Agency (EPA) diesel engine emissions standards, such as the interim Tier 4 (iT4) and Tier 4 stages. “To meet the EPA requirements, new engine components like high-pressure common-rail fuel systems are used to maximize fuel delivery efficiency,” says Fitzgerald. “Electronic control units have been incorporated to regulate fuel pressure and injection timing. These changes combined with after-treatment systems including diesel particulate filter systems and diesel oxidation catalysts are helping manufacturers meet these new regulations and changing the world of compact loaders like no other time in their history.”
Another outgrowth of iT4 and Tier 4 emissions implementation is the development of new oil specifications to lubricate these higher-performance engines. “The CJ-4 oils and additive packages available on the market today are designed to reduce ash and help loader engines achieve a longer service life. Their impact on compact loader maintenance will be seen as loaders begin to operate longer between changes, further reducing operational costs,” says Fitzgerald.
Increased machine performance and efficiency, along with improved operator comfort, will be at the forefront of compact loader development. “More efficient engines, hydrostatic drive, and hydraulic systems will be used throughout the industry. Collectively, we’ll continue to focus on developing technologies that increase your utilization, cut operating costs, and enhance your productivity. In this day and age, you should expect it,” says Fitzgerald.
■ ■ ■
[divider]
For More Information For more information on Bobcat products and how they can provide quality solutions for your next project, visit www.bobcat.com.
Modern Contractor Solutions, MAY 2014
Did you enjoy this article?
Subscribe to the FREE Digital Edition of Modern Contractor Solutions Magazine!
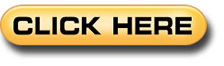