By Tony Hufford
It’s no secret—construction jobsites are busy, sometimes chaotic places with many tasks happening at once. Keeping work on track across the operation is critical to meeting project deadlines.
Numerous factors affect the ability for contractors to keep projects on schedule, including minimizing rework and downtime and keeping employees safe and productive.
Throughout the welding process, there are several techniques and best practices when cutting and grinding that can maximize performance and help reach these goals.
SAFETY TRAINING IS KEY
Step one in proper use of abrasive tools is training. Contractors and their teams should have an understanding of how abrasive products are designed to be used and any limitations of each product.
Different abrasive tools may require different techniques for safe use. For example, a cutting wheel should be used at a different angle and orientation to the workpiece than a grinding wheel.
Using abrasive tools as they are intended can help prevent injuries to the operator and others working nearby. In addition, following proper safety practices can help decrease downtime for injuries or rework, reduce the potential for workers’ compensation, and minimize turnover and training of new operators. All of these factors play a role in reducing costs and improving productivity for the operation.
TIPS FOR SAFE USE
There are two common safety pitfalls—both stemming from misunderstanding and improper use of the products—that can cause hazards when using abrasives. Follow these two tips for safe use:
- Watch the pressure. Using too much pressure results in more friction and heat—breaking down the abrasive at a faster rate. And more pressure doesn’t typically provide better performance. Operators may feel like they have to push harder to get the performance they want from an abrasive product. But often, this means they are using the product incorrectly or using the wrong product. Instead, consider whether a different abrasive is the answer.
- Use proper orientation and angle. Each abrasive product has a specific profile that affects how it should be oriented to the workpiece. Flap discs are designed to be used at lower grinding angles, closer to parallel to the work surface, while cutting wheels should be used at a 90-degree angle to the workpiece. Using the products at an angle or orientation they aren’t designed for can affect performance and damage the disc or wheel—and pose safety hazards for the operator.
IMPACT ON PRODUCTIVITY
Safe and proper use of products plays an important role in productivity on the jobsite. When an abrasive is used safely—and in the manner for which it was designed—it optimizes the performance and efficiency of that product.
When it’s used improperly, it can reduce the durability or cut rate of the abrasive and can result in time-consuming and costly rework. Reduced cut rate and durability can result in more frequent product changeover that increases downtime and takes away from tasks like cutting and grinding.
Proper use of abrasive products also helps reduce the potential for operator injuries that could result in downtime or worker turnover.
A common issue that affects productivity is not understanding how long an abrasive product can and should be used. More often than not, operators discard abrasives well before they are fully depleted. Understanding how abrasives wear and how to long they can be used reduces waste and cost of use.
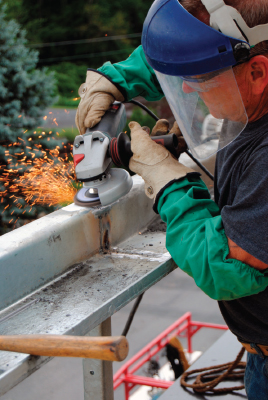
IMPACT ON QUALITY
The quality of the finished work is improved by using abrasive products safely and as they were designed. For example, problems such as heat discoloration, burr formation or gouging of the workpiece can occur when an abrasive product is used with too much pressure or at an improper angle.
Reducing these issues with proper product use may even help contractors eliminate additional steps that may otherwise be required to fix problems or repair the base material. This not only helps improve quality, but it also plays a role in overall productivity by reducing the time spent on the task.
Following some common best practices for abrasive products can help reduce quality issues and increase productivity. When grinding, for example, always enter the workpiece on a pull stroke rather than a push stroke to reduce the risk of damage to the base metal.
CLOSING THOUGHT
Following safe practices on the jobsite is critical to keeping projects on track and on budget. Safe and proper use of abrasive products helps reduce the risk to operators while also delivering better performance, efficiency, and extended product life. Consult an abrasives manufacturer about training in the safe and proper use of these products; it can provide contractors and their teams with the basics to help improve results.
About The Author
Tony Hufford is a category manager, metal fabrication, with Weiler Abrasives. For more, visit www.weilerabrasives.com.
Modern Contractor Solutions, June 2021
Did you enjoy this article?
Subscribe to the FREE Digital Edition of Modern Contractor Solutions magazine.
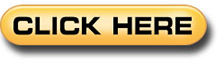