Whether you’ve won a bid for a short-term project that may not justify the purchase of a wheel loader, or you’ve exhausted your annual capital expenditure budget completely, rental is an avenue that can help you put the machine you need on your jobsite. Renting can also help you determine how a wheel loader’s maneuverability and efficiency, as well as its versatility, can match up to your typical job conditions and fit into your fleet for the long haul.
“Today, the decision to rent or own is largely driven by a finance perspective,” says Aaron Kleingartner, Doosan segment application marketing manager. “Contractors have to ask themselves—do they want to lock into a purchase? Or do they want a short-term, known fixed cost on a machine for a particular project, returning the machine when it’s no longer needed?” says Kleingartner. “They may also consider the possibility of purchasing the machine later if it will be needed for an extended period of time. Renting provides business options, and it lets them see how a certain wheel loader meets their needs, without long-term risk,” he adds.
MATCHING THE MACHINE TO THE JOB
Similar to a purchase, when choosing to rent a wheel loader, it’s important to let a dealer or a rental store know how you plan to use the machine. Perhaps you are a landscape contractor doing winter snow removal for 4 months. You might be an infrastructure contractor with a large fleet, but you need an extra wheel loader for a specific loading task. Or, you may not even have a wheel loader in your fleet, but you’re moving material with compact equipment and need more capacity.
Typically, wheel loaders are called upon to perform a variety of tasks, including loading, carrying, and stockpiling. All of these functions require a right-sized bucket to handle the type and volume of material for a particular project. One of the most common mistakes with wheel loaders, however, is incorrectly sizing buckets.
“There is a tendency for contractors to just rent the machine size they think they need and use a standard bucket,” says Shane Reardon, Doosan wheel loader product specialist. This can negatively impact productivity. “Before you even select a machine, it’s important to first determine daily production targets, then look at the density of the material, and match it to the size and capacity of a bucket,” says Reardon.
Heavy-equipment dealerships that rent wheel loaders, as well as some select rental stores, will generally have a variety of buckets in their inventory from general, all-purpose material handling buckets, to heavy-duty or rock buckets for more serious applications.
ATTACHMENTS MULTIPLY VERSATILITY
While rental needs vary widely—from loading aggregate to moving snow—they typically center on a very specific purpose that most often involves a bucket. However, if there’s a need to rent a tool carrier or a machine configured with a hydraulic quick coupler, several more attachment options may be available.
Wheel loaders can also be fitted with pallet forks and grapples. Brooms and snow blades multiply wheel loader productivity in the winter.
MAXIMUM MANEUVERABILITY
Evaluating cycle times and being able to complete a wheel loader’s various tasks with machines that are fast and nimble in challenging terrain are additional rental criteria. “The more efficiently they can move from one spot to another while they’re loading, the more productive they will be,” says Kleingartner.
Wheel loaders are constantly moving around the jobsite, driving into piles, reversing, lifting, and dumping, which makes visibility an important characteristic. An operating station that provides good visibility in all directions and the assistance of a rear-view camera can make operation significantly easier.
HANDS-ON TRAINING
Most rental transactions will provide some level of operator training for the machine and attachments. Rental customers also need to evaluate the amount of training that will be necessary for proper daily maintenance. “While it might only be there a short time, customers need to understand simple maintenance like where to check the oil, how to grease the machine—and generally make sure they’re maintaining it to the best of their abilities,” Kleingartner says.
FLEET MANAGEMENT
Many equipment manufacturers and dealers are equipping their machines with GPS-based fleet management systems that can be very beneficial to rental customers. These built-in satellite-based systems allow dealers and rental customers to strategically monitor critical machine information, manage maintenance requirements, and speed up theft recovery by tracking the unauthorized movement of heavy equipment.
By assessing your financial position and your project’s timeline, you can begin to begin to determine if renting a wheel loader is the solution that meets your short-term needs. With further evaluation of a particular machine’s features, capabilities, and efficiencies, you can make a fully educated decision that can result in high productivity rates. ■
For More Information:
Article courtesy of Doosan Infracore Construction Equipment America. For more information about Doosan wheel loaders, visit www.doosanequipment.com.
_________________________________________________________________________
Modern Contractor Solutions, May 2013
Did you enjoy this article?
Subscribe to the FREE Digital Edition of Modern Contractor Solutions magazine.
Renting Wheel Loaders Makes Good Business Sense
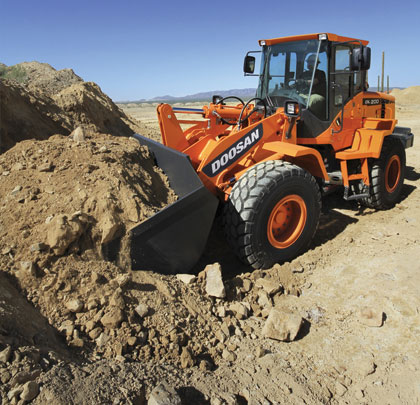