Years ago, between college semesters, I worked in trenches in front of a track hoe laying sewer pipe. The work was high stress and physically exhausting. But what I remember most was the smell. Sewer and diesel exhaust. It is said a smell can give you instant memory recall. To this day the pungent smell of diesel exhaust puts me instantly back into that mud-filled trench. One hot day I complained about the stench, prompting an old timer to say “Hell man! That’s the smell of money!” Thank goodness times have changed.
When it comes to public preventive health strategies, few can match the commitment to cleaner air. This is good news for those who earn their livings “in the trenches.” The stench of diesel fuel was an inescapable part of the whole construction experience. The same could be said for all those who, drive, repair, or sleep around anything with a diesel engine.
Not cleaning out the fuel before a high temperature bake cycle could cause onboard fuel to ignite and heat to near or above the melting point of the DPF substrate, causing glass glazing (permanent damage).
CLEANING UP DIESEL PARTICULATES
Starting in 2007 new trucks were built factory equipped with Diesel Particulate Filters (DPF) and Diesel Oxidation Catalysts (DOC) that trap and incinerate diesel particulates. Within 5 years, the same filters became standard equipment for new off-road construction, mining, and agricultural machinery. In California, older diesel equipment was retrofitted with exhaust filters to become compliant with that states stringent air quality laws.
Today the air is much cleaner because of this “sophisticated garbage can” known as a DPF. Like any garbage can, the DPF requires some timely attention to keep it operating at peak condition. The difference is you could buy about 20 household garbage cans for the average price of a single DPF.
If your equipment is fitted with an expensive DPF, here are five tips for managing the upkeep of your DPF investment and avoiding trouble.
Know the difference between soot and ash. Both load a DPF. Soot usually gets oxidized (incinerated) completely. Ash is the remains of engine oil that builds steadily and cannot burn off but fills in space intended for soot storage and regeneration. Ash causes restriction of exhaust flow through the filter, which translates to reduced power and fuel efficiency. After about 600 hours, ash trapped in the DPF makes up over 1/3 of the material. If left it will cause more forced regens, raising the potential for substrate cracking, melting, and hardening of the ash.
To clean the DPF of ash accumulation, get the DPF off your equipment and cleaned before the ash has time to harden into a solid block. For off-road applications, this usually means no less than every 2,000 hours operation between cleanings. Select a reputable cleaning service with the correct cleaning tools and inspection process to do the cleaning.
Make sure the cleaning service you choose performs careful visual inspection and flow and pin gauge testing to certify that a complete cleaning has been done. All DPF are different in the cell size geometry and amount of ash on board. Some DPF require more time in cleaning than others. For this reason, the cleaning process itself must be visible to the operator in order to judge when the cleaning is complete. You may as well not even clean a DPF if it’s not going to be cleaned correctly and completely. If you come home from work some evening and find the garbage can you rolled out to the curb that morning still partially full of last week’s garbage, how are you going to feel about your garbage pickup service? A DPF is a “sophisticated garbage can.” When ash garbage is left behind, it will turn into a solid, making it impossible to clean out later.
Never allow anyone to “bake” your DPF in a kiln at high temperature without first putting the DPF through a thorough pneumatic airknife cleaning that strips as much soot and ash out of the DPF as possible. Not cleaning out the fuel before a high temperature bake cycle could cause onboard fuel to ignite and heat to near or above the melting point of the DPF substrate causing glass glazing (permanent damage).
Insist on a dated data sheet that summarizes the “before” and “after” cleaning condition of your DPF. Tracking the condition of your DPF and recording it is critical to managing the frequency of future cleanings. If a small hardened ash island has appeared in your DPF, it’s a clear indication you should shorten the DPF maintenance intervals and get the ash removed earlier (before it hardens and becomes uncleanable). Too long of a time between cleaning causes hardened ash. Hardened ash increases the chances for unplanned downtime. Unplanned downtime takes longer and is far more expensive than periodic maintenance. Hence the diesel tech maxim “To PM is cheaper than to repair!”
DPF CLEANING
Techs that pay attention to the DPF cleaning process can tell if the cleaning is to completion or not complete. No doubt, every DPF cleaning machine gets filters cleaner, but is that clean enough? The cleaner you can get your DPF the longer it lasts. The worst thing you can do is to reinstall a DPF you think is clean only to find out after 20 hours of troubleshooting everything else that your DPF was not completely cleaned and a lot of ash was being left behind by your chosen cleaning service or method. Good DPF cleaners have a visible process for knowing when you’re finished. Good cleaners are run by conscientious techs that take pride in their work and take the time to do the job right. ■
About The Author: Drew Taylor is the director of global sales with FSX Equipment Inc. For more information, visit www.fsxinc.com.
_________________________________________________________________________
Modern Contractor Solutions – February 2016
Did you enjoy this article?
Subscribe to the FREE Digital Edition of Modern Contractor Solutions magazine.
Managing Your “Investment in Clean Air”
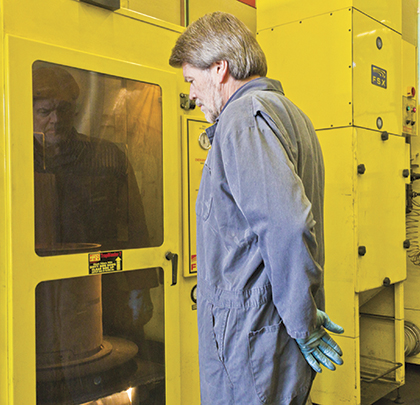