For one of the largest heavy construction firm in North Carolina, getting a handle on inventory control and standardizing maintenance procedures are the keys to future growth and competitiveness. These challenges pressed S.T. Wooten to transform its business through inventory and maintenance control processes and systems to make it more competitive and profitable. These improvements were part of the company’s Total Process Reliability (TPR) efforts.
SYSTEM PROCESSES
Utilizing MEA data, S.T. Wooten began the process of revamping the inventory and maintenance aspects of the company under the direction of logistics manager, Kelly Webb. This began with the creation of process flow diagrams for inventory and parts, which showed step-by-step procedures. In addition, the company expanded existing process guides with greater detail and created RACI charts to identify the responsibility and accountability roles in maintenance and repair process completion under the guidance of Raleigh-based TBR Strategies LLC.
The company vetted its E360 Computerized Maintenance Management System (CMMS), along with other options for ideal compatibility of present and future needs. The E360 was the ideal choice. S.T. Wooten worked with the provider to create customized KPIs; tracking and measurement of a wide variety of equipment, inventory, and maintenance parameters for creating detailed reports; and software for use in the asphalt and concrete plants to track repairs based on component tracking.
CULTURAL SHIFT
The cultural shift of moving away from an entrenched laissez-faire approach to inventory, maintenance, and repairs was challenging. A significant portion of the company’s workforce has been with them for 20-plus years. That brings a great many positives, but also challenges in changing a business’s operational culture in unfamiliar ways.
To foster a culture of inclusiveness, information sharing, and feedback, the company initiated structured communication about the upcoming process changes via email, newsletter, and word-of-mouth for initial information sharing. This structured outreach effort included formal meetings among departments, divisions, and crews to provide information and solicit feedback and questions.
INVENTORY CONTROL MANAGEMENT
Inventory management would begin with the equipment division’s two main rolling stock locations, which are its Wilson, North Carolina, Equipment Division, and its Sims, North Carolina, truck shop. The Sims location is the company’s heavy on-road equipment shop and home base for dump trucks and concrete trucks from three manufacturers. The Wilson location handles the majority of light fleet vehicles, as well as heavy off-road equipment.
In the approach to inventory management, analysis revealed inventory space at the Wilson location to be too small to hold sufficient stock to meet needs. Although the company explored several solutions, it decided to remodel a large office space at Wilson to create a primary inventory location. It also converted a small warehouse at the Sims location to create a secondary inventory location.
One of the first steps was for all the inventory control personnel to attend Marshall Institutes 3-day inventory control training, then a 3-day advanced MRO inventory control program by TBR Strategies. S.T. Wooten invested considerable time upfront in developing flow charts and process guides to serve as standardized operating procedures.
After remodeling the space, the company brought parts personnel into the process to gather all parts from their various locations. A parts vendor representative assisted parts manager, Andy Holcomb, in identifying and categorizing all parts as being good, obsolete, no longer relevant to rolling stock, or nonreturnable, in addition to other identification parameters.
While the company sold unusable parts for scrap, it returned a significant percentage of the unusable stock with value for refunds. Part numbers identified the remaining parts, enabling the inventory team to classify, label, and group them by truck type. After putting the parts into a spreadsheet, the inventory team simultaneously put them into bins, on shelves, and organized them.
After completing the process of finalizing spreadsheets, S T Wooten completed the final stage of entering the data into the CMMS for tracking with both the Sims and Wilson parts inventory locations in September 2015. The next phase will be to do the same at all six of their satellite locations, where parts and inventory are stored for maintenance and repairs.
THE MAINTENANCE PROCESS MIX
On the maintenance and repair side of the equation, the team developed PM, corrective maintenance, and emergency maintenance repair categories as the basis for assigning incoming repair incidents. As for emergency maintenance, the goal was to have critical spares on hand to eliminate the significant cost and subsequent lost production time associated with express shipping of parts for critical need repairs.
The company divided PM protocols into five categories with different levels of performed maintenance to ensure the changing of all oils and filters within a 2,000-hour cycle. These cycles become structured, scheduled maintenance intervals, which occur every 125 and 250 hours of service for rolling stock. The 125-hour is condition inspection.
This is all set up in the company’s eCMS EPR software system based on hours of service, which allows PMs to coincide with the meter readings on the equipment. The system automatically makes weekly update checks for equipment reaching a 40-hour threshold of the 250-hour mark (210 to 250 hours). It sends an alert to the CMMS for the PM planner or scheduler to order the filters and parts needed for a PM1, 2, 3, 4A, or 4B.
They can then schedule the maintenance at the best time for the jobsite and the operator. Once scheduled, the PM planner or scheduler can assign a technician to one of three new PM trucks to perform the PM as part of their full-time functionality.
Predictive maintenance is next on the rollout schedule, which will enable them to anticipate and prepare for scheduled parts replacements using the system’s lifecycle tracking data based on hours of use. ■
Check out the conclusion, Part 3, in the next issue of MCS as S.T. Wooten shares the final steps taken for the inventory and maintenance control overhaul and lessons learned in the process.
About the Author: E. Victor Brown is a freelance writer specializing in technology, data, and processes with an emphasis in healthcare, business, manufacturing, and industrial sectors. He can be reached at evictb@gmail.com.
_________________________________________________________________________
Modern Contractor Solutions – January 2016
Did you enjoy this article?
Subscribe to the FREE Digital Edition of Modern Contractor Solutions magazine.
S.T. Wooten Transformation: Part 2 of 3
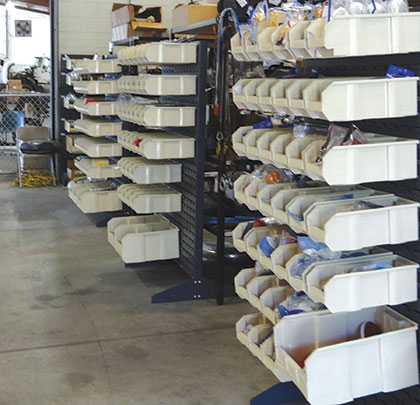