When precast and prestressed concrete manufacturers have sought predictable form curing—protected from unpredictable weather and fluctuating conditions—they have traditionally had to choose between two sub-optimal options.
They could construct an expensive new clear span building or building extension, potentially costing millions. To achieve the required temperature and humidity levels, they would still have to tarp the concrete forms within the building. Or they could manually tarp at the jobsite, engaging a crew to cover and uncover the precast girder or structural forms multiple times during various stages of the process.
Unfortunately, in addition to the manpower required, tarps tend to be inefficient covers that can inadvertently lose valuable heat, steam, or humidity required for proper and efficient curing. This is particularly true if the tarp tears, increasing the risk of product damage. A single bridge girder, for example, can cost tens of thousands of dollars to replace if it has to be scrapped due to quality concerns.
RETRACTABLE ENCLOSURES
Instead, to improve their process, proactive precast and prestressed concrete manufacturers across North America are increasingly turning to retractable enclosures that can provide a controlled environment superior to tarps, as well as building-like protection and curing predictability at a fraction of the cost and footprint of permanent structures.
These lightweight, modular, retractable enclosures essentially serve as both a building and a tarp, at sizes as large as 60 feet wide and 25 feet high with no length limit. With a rolling framework made of aluminum or steel, they typically have a telescoping aluminum frame, are designed for indoor-outdoor use, and do not require motors but can be motorized. The most rugged have a tear resistant, flame-retardant, UV protected vinyl shell with seams that are welded, not sewn.
Unlike typical tarps, retractable enclosures are specifically custom designed to meet the needs of a rugged, industrial environment. They not only protect precast concrete forms or curing areas from sun, rain, snow, and wind, but also enable precise control of humidity and temperature within a weatherproof, vapor-proof barrier. This enables more predictable form curing times and higher quality final product with virtually no stress cracks or imperfections, significantly reducing the reject rate.
With retractable enclosures, significant savings can be achieved for a number of reasons. Since they can eliminate the need to construct a permanent building, capital expenses are drastically reduced. Retractable enclosures also reduce employee time spent covering and uncovering products, as one or two employees can typically operate the retractable enclosures by hand without additional equipment.
Since retractable enclosures also offer full overhead and side access when retracted, this allows a crane to hoist oversized forms, such as girders, when curing is complete, saving time and labor over permanent structures where this is not possible. Because they can be used indoors or out, they can be used as a mobile plant near the worksite of a project, if needed, minimizing product transport.
Production downtimes are also reduced since the retractable enclosures facilitate production virtually year-round, enabling consistent pouring and curing in hot and cold weather.
Since retractable enclosures also offer full overhead and side access when retracted, this allows a crane to hoise oversized forms such as girders when curing is complete, saving time and labor over permanent structures where this is not possible.
IMPROVING QUALITY AND EFFICIENCY
When Prestressed Systems Inc. (PSI), an Ontario, Canada-based architectural and structural precast company, sought to implement a new prestressed concrete curing standard required by the Ministry of Transportation of Ontario (MTO), it turned to a retractable enclosure by Chameleon Innovations, a Montreal, Canada-based manufacturer of custom retractable enclosures.
PSI was confronted with the challenge of not only applying a tight enclosure around their girder forms but needed a reliable method of enclosing them that would meet stringent temperature control requirements. A simple tear or gap in a tarp could throw off temperatures enough to render the product unacceptable.
“With the Chameleon retractable enclosure, we not only eliminated the need for a permanent building addition, but also improved our product quality and efficiency,” says Collavino. “Now one person can open or close the retractable enclosure by hand, which frees up three laborers and a crane for other work.”
Previously with manual tarping, PSI found that steel molds could become very hot outside in the sun. When pouring concrete into potentially hot molds, flash concrete setting could occur, according to Collavino.
“With the ease of opening and closing our retractable enclosure, we eliminate potential flash concrete setting,” says Collavino. “This is because we were able to significantly reduce the temperature of the steel mold outside, keeping it and our production crews out of the sun and in the shade.”
ADDED BENEFITS
One of the main benefits of using a retractable enclosure has been virtually eliminating production downtime due to bad weather, according to Collavino.
“On cold, windy, rainy, or snowy days, our production crew could extend the enclosure and work under cover, with transparent roof panels allowing enough natural light to clearly see the molds without indoor lighting,” adds Collavino. “In 99.9 percent of all extreme hot or cold weather, our crews could work and the retractable enclosure helped to maintain regulated temperature. This helped our bottom line.”
Collavino credits the retractable enclosure for bringing added safety to his precast operation. “Once we fully retract the enclosure, we can easily see the product, open our mold, and spot the crane as it moves product out of the way. “We’re not hindered by temporary walls or tarps that may reduce visibility, be in the way, or present a safety concern.”
Because of the success of the retractable enclosure, PSI purchased ten more in the past 5 years for use with panel beds, second stage curing, and aggregate storage. It uses them to produce precast products from bridge deck slabs and bleacher seating to parking structure components and apartment building sheer walls. ■
About The Author Del Williams is a technical writer based in Torrance, California. For more information about Chameleon Innovations, call 888.695.3382, or visit www.chameleon.ca.
Modern Contractor Solutions, October 2014
Did you enjoy this article?
Subscribe to the FREE Digital Edition of Modern Contractor Solutions Magazine!
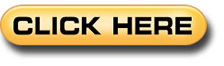