For decades, industrial facilities have measured the effectiveness of a coating by its ability to prevent corrosion, which, of course, is its fundamental purpose. However, with the increasing awareness of the dangers of traditional organic-based coatings and the serious health risks posed to coating contractors, many facility safety managers are specifying safer, inorganic options that now exist on the market.
THE RISKS
Coating contractors regularly engage in one of the most hazardous jobs in a plant. Published OSHA accident reports available on the United States Department of Labor website read like tragic news headlines: “One Killed, Two Injured When Paint Vapor Explodes;” “One Employee Dies and One is Burned in Painting Flash Fire;” “Three Employees Asphyxiated by Paint Fumes.”
The risks are further exacerbated within confined spaces such as tanks, vessels, silos, storage bins, hoppers, and vaults—common steel structures desperately in need of corrosion protection found in most industrial facilities. Confined spaces are not only known to accumulate toxic, flammable, and even explosive fumes and dust, but the very act of application of traditional coatings presents its own serious risks.
The problem stems from the application of carbon-based coatings, which include commonly-used polymers, polyureas, and urethanes. These coatings off-gas hazardous VOCs and Hazardous Air Pollutants (HAPs) during, and after, application, which can cause irritation of eyes, nose, throat and/or respiratory tract, headaches, nausea, lightheadedness, memory impairment, or even unconsciousness to exposed personnel or contractors.
Furthermore, when applied with a spray gun, atomized coatings that have low flash points can create a fire or even explode. Given that plural component spray equipment utilizes electrical elements as well as heat, the equipment itself can pose a risk in such an environment.
“Spraying typical coatings inside a tank is dangerous,” says Tony Collins, an industrial contractor for 30 years. “Spraying atomizes the toxic, flammable coating material, which can have a flashpoint as low as 70 degrees F, the working temperature inside the tank. This means that if a tool is dropped or a metal object is dragged across the tank and a spark occurs, the fumes can ignite and explode. I’m astonished that it’s legal.”
The risk is not limited to a single job, unfortunately. Coating contractors consistently exposed to VOCs over time can develop chronic health issues ranging from liver, kidney, and nervous system damage, to asthma and certain types of cancer.
To address the many risks and improve worker safety, confined space work is regulated by OSHA’s Code of Federal Regulations 29 CFR 1910.146. Tragically, as investigation of new accidents continues to illustrate, many of the safety precautions are not followed adequately.
NEW, INORGANIC COATING OPTIONS
Fortunately, in the past decade coating technology has changed dramatically. A new category of inorganic Chemically Bonded Phosphate Ceramics (CBPCs) has been formulated that emits no VOCs or HAPs during or after application, has no flashpoint, flame spread, or hazardous waste disposal requirements.
Some of these coatings, such as EonCoat, available from a company of the same name, contain no toxins of any kind that could cause distress, whether touched, consumed, or inhaled.
The EonCoat ceramic coating consists of two, non-hazardous components that do not interact until applied by a plural component spray gun. Since the components are not mixed and do not meet prior to application, the need for VOC-generating ingredients in the formulation is completely eliminated, as are HAPs.
Ceramic coatings generate no smoke and have a flame spread rating of zero, which means that flames will not travel across the surface. In fact, an intense flame can be directly exposed to the coated surface and the substrate will not catch fire unless enough heat is generated to make the substrate behind the coating self-ignite. With no flashpoint, EonCoat cannot ignite or explode during spray application as well.
As for its corrosion resistant properties, ceramic coatings more than pass the test.
In contrast to typical polymer coatings that sit on top of the substrate, EonCoat bonds through a chemical reaction with the substrate, and slight surface oxidation actually improves the reaction. This makes it virtually impossible for corrosion promoters like oxygen and humidity to get behind the coating the way they can with ordinary coatings.
The corrosion barrier is covered by a true ceramic shell, which resists fire, water, abrasion, chemicals, and corrosion.
With the availability of new, safer, inorganic options such as EonCoat on the market, coating experts, as well as industrial asset and safety managers, can now specify an alternative to traditional carbon-based coatings that will dramatically increase safety without sacrificing corrosion protection.
“If you look at how safety and environmentally conscious the industry has become, there is no excuse for using toxic, flammable materials where there is another option,” states Collins. ■
For More Information:
For more information about EonCoat, call 252.360.3110; email jim.mcbrayer@eoncoat.com, or visit www.eoncoat.com.
_________________________________________________________________________
Modern Contractor Solutions, March 2014
Did you enjoy this article?
Subscribe to the FREE Digital Edition of Modern Contractor Solutions magazine.
Safety First for Industrial Coatings
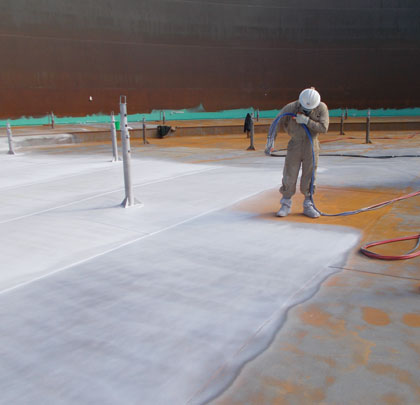