You change your oil not because you want to, but because you have to, or risk premature wear and untimely mechanical failures. You need more than good quality oil and standard oil filters to extend component life and time between oil changes.
The philosophy of changing oil at a prescribed interval has changed substantially in recent years. With today’s availability of affordable and accurate oil sample analysis, one can quantitatively monitor contamination levels, oil condition, and wear trends within a component. This valuable tool allows one to prolong oil life while achieving targeted rates of mechanical wear. Oil degradation is caused by many factors including heat, working environment, as well as the rate and type of oil contamination. More importantly, the type of filtration used to filter the oil, is the single most important factor determining the life of the oil and the component it lubricates.
The oil filter is an important component of any lubrication system, and is essential for enhancing longevity and performance. Filtration is the process of separating insoluble particulate matter from the fluid by forcing the fluid through a filter element, trapping the contamination in the media. The density and volume of the media, and the rate of flow, will determine; the size, rate, and type of contamination removal. “Bypass” filters are designed to remove “ultra-fine” contamination and water that is normally missed by existing filters, dramatically extending the life of oil and the component it lubricates.
FULL-FLOW VERSUS BYPASS FILTRATION
Bypass filtration is often referred to as a “kidney loop” oil filter. It is designed to pass small volumes of oil through a dense filter element media at a slow rate of flow, typically filtering less than 10 percent of a primary filter. Conversely, the majority of existing OEM primary oil filters are “full-flow” and are designed to protect the component from larger particles in the oil, preventing failures by filtering large volumes of oil required by the component, through a coarse filter element—they are not designed to polish oil or remove high concentrations of silt, soot, or water. To put it into perspective, human hair is typically 75 microns in diameter, and the human eye can see particles 25 microns in size. The standard diesel engine oil filter is rated at 25 microns, while many hydraulic filters are 10 microns, both being full-flow, limit their ability to remove ultra-fine particles from the oil. These ultra-fine particles account for the majority of contamination associated with diesel engine and or hydraulic pump wear. In addition, full-flow oil filters do not efficiently remove the water produced in the combustion process in an engine, or condensation that is accumulated in a hydraulic oil tank. Only trace amounts of water are required to form acids in oil. Acids accelerate the depletion of additives and increases corrosive action within a component. Full-flow filters alone cannot keep oil constantly clean, reduce engine wear, or prolong oil. A primary filter’s main function is not to polish or prolong the oil. Over time these ultra-fine particles accumulate to create a sandblasting effect throughout the system. Compounded with the presence of water and the formation of acids, the system is subjected to accelerated erosion, abrasive wear, adhesive wear, cavitation, fatigue, oxidation, varnishing, gum and sludge formation, decreasing the life and efficiency of the engine, hydraulic system, or transmission.
BYPASS FILTERS COMPLEMENT FULL-FLOW FILTERS
The rate at which contamination enters a system is greatly underestimated. Likewise, the ability of full-flow filters to effectively remove metal contaminants is greatly overstated. When a primary full-flow filter is accompanied by a secondary bypass filter, the latter removes the ultra-fine contamination and water typically missed by the primary. The use of both will dramatically increase the time between oil and main oil filter changes, protect the component, and reduce mechanical wear. Standard full-flow filters are designed to remove larger particles and trace amounts of water. Some bypass filters, such as
Generation 2 Filtration™, are designed to remove particles down to 1 micron as well as free-standing and emulsified water from oil. A bypass is designed to filter small volumes of oil at low pressure, enabling the oil to pass slowly though a dense but fine paper media, trapping contamination and water missed by the primary. By efficiently removing water and ultra-fine wear particles from the oil, contamination levels and associated mechanical wear are dramatically reduced, minimizing downtime, and your need to replace the oil. It is an industry standard that 80 percent of all hydraulic failures are due to contaminated oil. To reduce wear and untimely failures, one could replace oil frequently, or instead use bypass filter technology, and reap the economic and environmental benefits of keeping the oil clean and healthy for extended periods of time.
The cost-effective benefits of bypass filtration are immense and measureable. Most bypass filters can easily be installed on diesel engines, hydraulics, and transmissions. The addition of bypass filter technology will greatly improve oil quality, and the overall health and life of a component, and its effectiveness and cost-saving benefits can easily be evaluated by third-party independent oil sample analysis. ■
About the Author:
Preston Ingalls is president and CEO of TBR Strategies, LLC, a Raleigh, North Carolina-based maintenance and reliability firm specializing in the construction and oil and gas industries. Preston can be reached at pingalls@tbr-strategies.com, or visit www.tbr-strategies.com.
_________________________________________________________________________
Modern Contractor Solutions, January 2014
Did you enjoy this article?
Subscribe to the FREE Digital Edition of Modern Contractor Solutions magazine.
Bypass Filtration
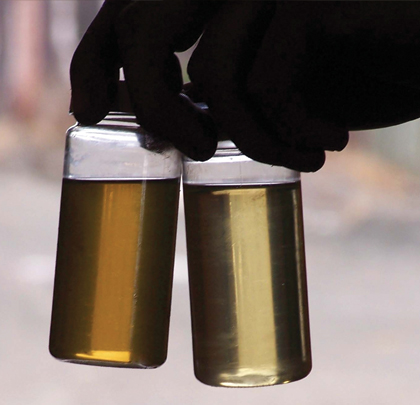