The building industry and the green movement are, by this point, fairly well acquainted, and undoubtedly, there are real benefits attainable for builders who have an eye toward sustainability as they undertake new projects. An environmentally friendly building can realize cost-savings related to energy consumption, and other areas, but what’s the right path to take on your road to a greener future?
Given recent economic fluctuations, builders are increasingly reluctant to spend money unless they can justify it. No matter how much cache might come from using a certain green building rating system, builders are aware that the generalized metrics inherent in these programs don’t always make good sense from a financial, or even true sustainability, standpoint when applied to an actual project within its unique paradigm. This is the biggest problem with the current systems.
A HISTORY OF GREEN
Leadership in Energy and Efficiency Design (LEED) was introduced by the USGBC in 1998, and has since been adopted industry-wide as the go-to sustainable building rubric. LEED has become the de facto authority for “green” construction and certifies 1.5 million square feet of building space each day in 135 countries. LEED is used regularly in the building industry and stands up as a thorough and robust grading system, but like anything else, it comes with its idiosyncrasies and limitations.
The LEED program contains some broadly applied metrics, such as recycled content, regional material, and rapidly renewable materials. The process by which credits are awarded for these metrics puts certain projects at an unfair disadvantage. As an example, one of these metrics dictates that manufacturing and natural resource extraction must occur within a 500-mile radius of the project to qualify for the corresponding credits. This criterion is highly prohibitive for material, such as steel, because iron ore is extracted only in certain places and recycled material can be difficult to trace due to the comingling that has to occur to meet the ASTM material requirements. This severely punishes steel as a green option even though the steel industry has a highly efficient transportation system in place to move this material. Because this criteria is so general, though, no credit for that system is given. The metal industry does a good job of manufacturing components within 500 miles of a project, however, so as we consider the element of transportation, these projects would seem to qualify as “sustainable.” But because of the way the extraction criteria are spelled out, metal projects are rarely applicable for this credit.
A NEW APPROACH
The sustainable building industry is evolving, though, and there are new green building standards and systems being introduced that promise to mitigate the inequities seen in previous models. During the past few years, Life Cycle Assessment (LCA) has emerged as an alternative to the LEED Materials and Resources credits and replaced several credits in the newest version of LEED.
An LCA is a scientific method applied to the selection of building materials or assemblies. As the name implies, this methodology examines the impact of building material starting with its creation through its disposal or recycling. A properly scoped LCA considers the energy used and emissions caused in the raw material procurement of a product, as well as its manufacturing, delivery, deployment, use, deconstruction, recycling, and disposal.
Following the process of combining LCA of compatible scopes for different materials and assemblies allows professionals to look at the building’s impact as a whole and take a more “big picture” approach to sustainability. It measures the tradeoffs between products in terms of energy use, greenhouse gas emissions, air quality impacts, water quality impacts, and solid waste (landfill) impacts. LCA differs from traditional LEED credits, which can encourage builders to go for individual materials that don’t necessarily work well together.
TOMORROW’S RATING SYSTEM
The stage has been set for something of a divergent evolution, where the rating systems evolve into more complicated and holistic scientific models in which computers will do most of the number crunching. At the same time, much of the simpler criteria that are currently in green building rating systems will appear as requirements in high performance building standards (a.k.a “green codes”). Some will even find their way into traditional building codes to be adopted on a local or state level as a matter of compliance, rather than performance.
In fact, we are already seeing signs of this change in commercial construction. LEED v4 (currently in beta and due to be launched later this year) will be a traditional rating system, but it will have credits that evaluate environmental performance using the more holistic model of LCA. Meanwhile, many of the original LEED requirements can be found in a tweaked form within documents like ASHRAE 189.1, and the International Green Construction Code (IgCC).
Much like an energy model simulates building energy systems, LCA tools simulate material and energy flows to determine the environmental impacts throughout the entire building lifecycle. In LEED v4, this is limited to building creation but it will naturally grow to include use of phase effects, including energy, and can go through deconstruction and disposal/reclamation as well. With quite a bit of additional development, the LCA model has the potential to swallow up the entire scope of LEED as it exists today. ■
About the Author:
Bob Zabcik is NCI Building Systems’ director of research and development. He is a LEED accredited professional and a registered professional engineer with more than 20 years of experience. He serves on several professional committees, such as the MBMA Energy Committee and Sustainability Committee, as well as several task groups of those committees. He is also on the Board of the Cool Metal Roofing Coalition and serves as the director of their technical committee. To learn more about NCI Building Systems, visit www.ncilp.com, or to contact Bob: bobz@ncigroup.com.
_________________________________________________________________________
Modern Contractor Solutions, October 2013
Did you enjoy this article?
Subscribe to the FREE Digital Edition of Modern Contractor Solutions magazine.
Putting "Green" Under the Microscope
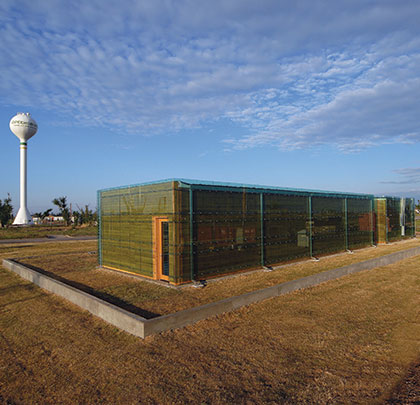