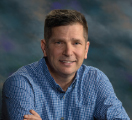
Steve Warfle
CEO
InSite Software Inc.
Over the past year, we have seen the grading industry continue to navigate complex challenges while embracing innovation. Labor shortages have been a persistent issue. Instead of simply trying to recruit more workers, many companies are turning to technological solutions that can enhance productivity and accuracy.
Today’s earthwork professionals face intense pressure to deliver precise estimates. This challenge is compounded by the fact that data is often collected from multiple sources, including PDF, CAD, Drone, Google Earth, Data Collector, etc. Leveraging cloud-based platforms like Google Earth and drone technology has become crucial for success. These technologies allow smaller teams to manage more complex projects with greater precision and speed.
At ConExpo 2023, we introduced Elevation Pro, a cutting-edge earthwork takeoff software platform designed to address the evolving needs of modern estimators. Our development journey began with comprehensive research, including extensive collaboration with customer focus groups and strategic partnerships. We figured out what features today’s modern earthwork estimators require to increase production and minimize the wages spent on takeoff and modeling. Elevation Pro is the only software that can open multiple documents simultaneously.
One example: The software can export KMZ files to Google Earth. Cut-and-fill depth contours can be seamlessly overlaid on PDF documents, enabling real-time communication and collaboration among field staff using any GPS-equipped phone or tablet.
Combining industry insights, customer feedback, and technological advancements, we continue to take a forward-thinking approach to earthwork takeoff. The ongoing challenge remains to find the right balance between technological investment and human expertise.
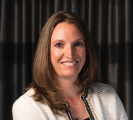
Kim Spahn
CEO
Concrete Masonry Checkoff
Concrete masonry units (CMU) are often associated with sheer strength, but that’s just the beginning. In fact, CMU offers a host of economic and environmental advantages, particularly in disaster-prone areas. Best of all, these benefits come without compromising style or versatility.
So, what’s changed?
Today’s CMU is light-years ahead of the block from your grandfather’s generation. Modern innovations have transformed concrete masonry, incorporating recycled materials and even carbon dioxide to reduce reliance on traditional cement. Life Cycle Assessment (LCA) studies reveal CMU’s unique ability to sequester carbon: The calcium hydroxide in the block reacts with CO₂ to form calcium carbonate, a stable mineral that locks in carbon indefinitely. This natural process helps offset the carbon footprint of new construction.
Lightweight CMU has also become an increasingly popular option which is 30 to 40 percent lighter than traditional block and nearly as strong. These units are made from clay, shale, or pumice versus traditional gravel or sand aggregates. Work crews are also increasing productivity by utilizing robotics and exoskeleton technology to safely move material with less physical strain.
Modern CMU delivers enhanced thermal and acoustic insulation, greater strength and durability, and an astonishing array of textures, colors, and finishes—proving that function and form can coexist beautifully.
Be on the lookout next year for more information about our new Block Design Collective, a virtual destination where designers and contractors can access complimentary design services and expert CMU support. For more information, visit www.beautyofblock.com.
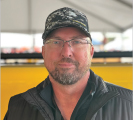
Rob Handson
Southwest Territory Manager
Ligchine
Trends in 2024 include skilled and willing labor shortages; investments in technology and equipment; and large machines utilized on small projects.
With today’s competitive concrete market, many business owners are looking into equipment and technology to get the job done. The ever-changing landscape of the concrete industry has forced companies to look at equipment and technology to fill the voids of skilled and willing labor shortages.
Kole Calvert, owner of North Rock Construction in Ogden, Utah, is one of many contractors preparing for the future by utilizing equipment. This investment will save on labor costs and provide a better workplace for his employees by looking out for their long-term sustainability. Kole Calvert had this to say about how investing in equipment changed his business “I have more confidence in bidding larger jobs, and getting mud on the ground quicker and flatter is a lifesaver”.
Laser-guided concrete screeds are not only being used today on large slabs and warehouse placements. Many companies besides North Rock Construction are finding ways to use laser-guided screeds on their smaller commercial floors and paving projects. Some jobs are as small as 4,000 square feet. The days of hand screeding will most likely never completely disappear. Still, companies that look to move forward with technology and equipment will continue to lead the way in today’s competitive market.
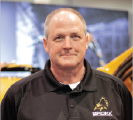
Jeff Keeling
Vice President of Sales and Marketing
Brokk Inc.
Each year, hundreds of injuries and even deaths occur from decaying infrastructure. In the coming years, the Infrastructure Investment and Jobs Act will invest nearly $27 billion into repairs. Along with that, labor shortages are affecting contractors’ abilities to keep up.
As a result, more are turning to technology such as remote-controlled demolition machines and hydrodemolition robots. These modern solutions provide more safety, productivity, and efficiency for removing concrete around rebar than handheld tools, mini excavators, and backhoes.
Hydrodemolition robots can remove as much as 800 square feet of bridge deck at a depth of 4 inches in just an hour, a fraction of the time it would take a crew of workers with jackhammers.
Unlike handheld tools and excavators, hydrodemolition robots virtually eliminate the possibility of unintended damage during bridge repair. The 20,000-psi water jets target the bridge deck surface, quickly removing layers of concrete but leaving rebar unscathed and clean. This method also causes no vibrations, eliminating the microfracturing that could threaten bridge stability.
Alternatively, a remote-controlled demolition machine equipped with a breaker attachment and controlled by an operator and one spotter can break up 2 square feet of bridge deck concrete in 15 minutes. The same area in the same amount of time would require three workers with handheld tools.
Remote-controlled machines drop labor costs by 33 percent. Plus, it’s a lot easier to recruit young workers to run remote-controlled machines and robots as opposed to handheld tools. The contractors that prepare, plan, and incorporate technology solutions will be able to successfully, efficiently, and profitably address bridge repair needs.
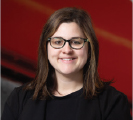
Julie Portillo
Product Marketing Manager
Bobcat Company
The commercial construction industry has continued to grow and evolve with 2024 being another year of advancements and new developments.
An influx of first-time buyers has spurred industry growth. As construction projects become more diverse and specialized, smaller contractors and new entrants are increasingly investing in compact equipment. These machines offer versatility, maneuverability, ease of use, and cost-effectiveness, making them an attractive option for those looking to enter the market or expand their capabilities.
Another critical development is the industry’s response to labor shortages by leveraging compact equipment to supplement, or in some cases, replace manual labor. The construction sector has faced challenges in finding skilled labor, and compact equipment offers a viable solution. Compact equipment can perform tasks such as digging or hauling materials that would otherwise require multiple workers and manual labor. Not only can compact equipment help mitigate labor shortages, but it also enhances productivity on job sites, as machines can operate in confined spaces and perform tasks with greater precision.
Bobcat has increasingly expanded its product portfolio over the past several years, growing into new industries and empowering customers to accomplish more, in more ways, than ever before. The construction industry is a key focus for Bobcat, and looking forward, our organization will further enhance, advance, and grow our construction equipment and technology offerings to support customers’ toughest challenges and greatest opportunities.
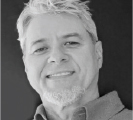
Matt Weber
Editor
Modern Contractor Solutions
In 2024, new technology has been shaping commercial construction in more ways than ever with the advent of artificial intelligence and advanced software programs. Not only does centralized project management software facilitate better communication between construction teams, but it increases the accuracy of reports to generate usable real-time information that principals can use to economize time and labor, improve maintenance routines, and monitor safety procedures. This usable data can also be implemented by artificial intelligence to automate processes that formerly required manual data entry, further saving time and labor costs while reducing error.
Modern construction technology benefits the workers in the field as well as the project managers. GNSS (Global Navigation Satellite System) technology, which has long been used for fleet tracking and equipment security, is appearing on more and more construction machines to offer grade-control. Not only can an automated system fine-grade the subgrade for roadwork, but GNSS machine-guidance modules are now available for compact track loader buckets, making such equipment even more versatile with a single solution for layout, grading, and leveling.
Plus, this new technology appeals to younger workers in an era when the construction industry needs new talent. Young workers tend to have more experience with technology than with hands-on construction skills. As a result, modern construction applications that make use of cutting-edge software, labor-saving robotics, and remote-control operation have greater appeal to tomorrow’s workforce as a viable career path.