Walmart is taking a significant step toward the future of retail construction with a first-of-a-kind project with Alquist 3D, a leading innovator in 3D concrete printing (3DCP). The undertaking has led to the printing of one of the largest freestanding, 3D-printed commercial concrete structures in the United States—a nearly 8,000-square-foot, 20-foot-high addition to its store in Athens, Tennessee. This expansion, dedicated to enhancing Walmart’s Online Pickup & Delivery (OPD) program, marks the first time Walmart has utilized 3D printing technology at this scale. The work accomplished by Alquist in Athens has led to a second project with Walmart in the near future.
“This is the first such facility of its kind and it’s just incredible that it is a reality; this is going to play a major role in the advancement of 3DCP technology,” says Zachary Mannheimer, founder and chairman of Alquist 3D.
VISION AND EXPERTISE
Walmart chose Alquist 3D for this project after considering several companies in the field of innovative construction technology. Alquist 3D stood out for two primary reasons: its proven expertise in delivering complex projects and its unique ability to partner with industry leaders such as SIKA and RIC Technology. These partnerships have equipped Alquist with the necessary knowledge and resources to meet the challenges posed by this ambitious project.
“For Walmart to see the value in this project demonstrates how forward-thinking the leadership of this organization is,” says Mannheimer.
“The knowledge gained on this project will accelerate our work on residential units to fulfill the mission of Alquist,” says Patrick Callahan, CEO, Alquist 3D. “In order to improve, we tackled the most challenging project we could find and completed it with excellence.”
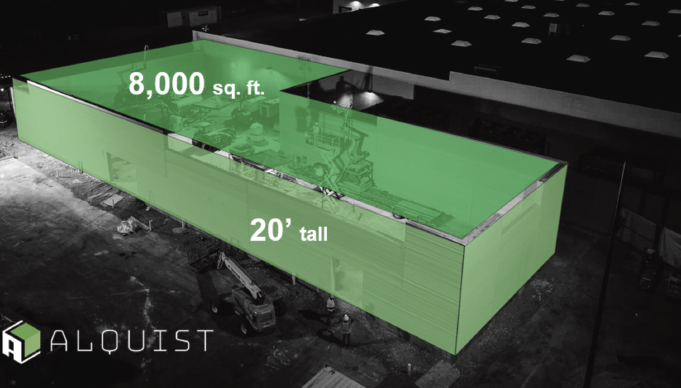
GREENER FUTURE
Walmart’s decision to use 3D construction printing aligns with its broader goals of becoming more environmentally friendly, leveraging cutting-edge technology to attract customers, and accelerating the construction process. This project represents the integration of advanced construction techniques into Walmart’s infrastructure.
“Walmart is always looking to innovate and leverage developing technologies, and we looked at several new building methods and companies for this project,” says Mike Neill, VP of new construction for Walmart. “Alquist presented the best ability to work with due to their deep knowledge of 3D materials, robotics, and desire to take on an ambitious and unique project.”
LEARNING AND GROWTH
The project has offered invaluable insights for the Alquist 3D team. Key lessons include the importance of managing material temperatures during summer, achieving faster print times, and successfully constructing vertical structures up to 20 feet—a first for the company.
Collaboration with students from Aims Community College has also proven to be an effective training pathway for future projects. The experience gained from this project will be crucial in future endeavors, including residential and commercial construction, as well as potential infrastructure projects. The company views this commercial endeavor as a strategic move that will not only advance its construction capabilities but also contribute to addressing larger societal challenges, such as the housing crisis.
Alquist 3D is a 3D-printing construction company that uses cutting-edge technology to create homes, buildings, and other structures aimed at decreasing the cost of homes and solving the housing crisis. Alquist is conducting R&D to build new public and private infrastructure using 3D-printing technology. For more, visit www.alquist3D.com.