Some construction companies use dedicated schedulers to produce project schedules, a practice that can exclude the perspective from those in the field responsible for delivering the project.
Flintco, a full-service construction company with eight offices throughout the South and Southwest U.S., does things a bit differently. Nearly all of Flintco’s project teams develop their project schedule with input from everyone involved on the job. According to Melanie Gilbertson, director of production support at Flintco, the project teams offer a perspective that is unique to their position.
“Being out at the job site, the project team is in a far better position than anyone to understand all of the nuances of a project, as well as the risks and challenges,” she says. “These are the people responsible every day for what’s going to be constructed. Consequently, they bring certain insights to the job that no one else can.
“While we don’t have dedicated project schedulers, we have a team of corporate schedulers who provide portfolio support to the onsite team,” she continues. “They can help work through problems that the team is unable to solve or offer advice on how to remedy a project delay. But as far as creating, updating, and maintaining the schedule, the buck starts and stops with the folks out in the field.”
THE NEED FOR SCHEDULE QUALITY
Skill levels vary between project teams when it comes to schedule development. The need for consistent, company-wide schedule quality convinced Flintco to examine the available tools for schedule analysis.
The committee got wind of a program called SmartPM, a cloud-based platform for analyzing schedule data and producing reports that would identify potential delays, overruns, missing logic ties, and overoptimistic milestones.
“We were aware that there was a program out there that could take individual project data and identify key metrics associated with the project,” says Gilbertson. “When we heard that SmartPM had made an update to the platform’s dashboard, we felt it was time to check back in and at least watch a demo. We really liked what we saw.”
What piqued Gilbertson’s interest was the platform’s ability to compile deep insights about the project schedule without resorting to a very technical, hard-to-use program. Flintco began a trial using it on three or four projects for a six-week period at the end of 2022; the platform’s features, including its intuitive interface and ease of use, convinced them to move forward with a 10-project pilot.
After just six months of use on those 10 projects, it clearly enhanced Flintco’s ability to monitor schedule data while saving time and reducing manual data input. Flintco implemented the platform company-wide. Now, once an initial schedule is created, it is fed into SmartPM for rapid evaluation; the team also relies on the platform to generate updates on whatever basis they are needed. At Flintco, project teams are expected to update schedules weekly, a timeline that is now more realistic.
“For whatever reason, we weren’t always getting the weekly updates,” recalls Gilbertson. “That has changed, since SmartPM can analyze the schedule instantly, which is far simpler than using our previous system to run through the schedule line by line. And since some of our project schedules contain 5000 or more line items, the time savings is dramatic.”
Meeting the goal of producing weekly updates is also critical because Flintco’s policy calls for the use of data that is a maximum of seven days old; making the weekly reports a consistent practice ensures that this policy is maintained. What’s more, current data and timely updates are required elements of Flintco’s Lean2.0 program, the company’s signature approach to Lean construction that supports on-time completion.
QUALITY CHECKER IS APPEALING
The platform’s Quality Checker is a particularly appealing feature to Gilbertson and Flintco. It provides a fast yet accurate snapshot of the initial project schedule, based on standard practices and guidelines established by the Construction Specifications Institute (CSI). While it can provide feedback in various formats, Flintco prefers the letter-grading system.
“We stuck with letter grading, since it’s a system that is familiar to everyone—like going back to school,” she says. “What’s more, the report generated from the Quality Checker highlights the activity causing the problem, so team members know exactly what they need to do to improve their perceived letter grade.
“Now, if team members are not sure of how to remedy a problem, they can turn to our scheduling team for assistance. Since our scheduling team no longer has to handle the ‘nitty-gritty’ details of scheduling each individual project, they’ve got the bandwidth to focus on helping teams address the issues that SmartPM has identified.”
Teams don’t need to turn to the corporate schedulers as frequently, given the utility of the tools that the software platform provides. For example, if someone has a question about a specific item, they can use their mouse to hover over the item, at which point the program will offer tooltips or other resources that help the user solve the problem on their own.
Presentation of the key metrics uncovered by the program was also a priority. Changing to a more user-friendly and readable presentation format had been on the company’s radar for some time.
“We had a very convoluted Excel sheet to present the information,” recalls Gilbertson. “A big process for us was converting it to a more collaborative platform, where we still had to make a lot of manual data entry points.
“We saw SmartPM as a tool that presents the most pertinent points in a way that everyone can understand,” Gilbertson notes. “SmartPM enables senior operations leaders to quickly review the key metrics at the top of the page and immediately see what has changed since the last update instead of endlessly scrolling through lines of information that are not relevant to them.”
For More Information:
Flintco, founded in 1908, maintains eight full-service offices and offers preconstruction, construction management, design-build, project and program management with the capability to self-perform inclusive of concrete, miscellaneous steel and excavations for foundations. For more, visit www.flintco.com.
Modern Contractor Solutions, May 2024
Did you enjoy this article?
Subscribe to the FREE Digital Edition of Modern Contractor Solutions magazine.
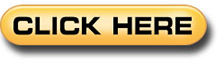