By Ara Eckel
Need help determining the proper size and configuration of the right aerial lift for your application? In some industrial facilities, limited space, obstructions, and overhangs make it challenging to safely reach and service elevated equipment. In other cases, facility managers simply need help determining the “best fit” machine for their needs.
Whatever the situation, augmented reality (AR) technology, like JLG’s app, can offer you a tool to simplify these decisions by showing what a variety of accurately sized aerial lifts would look like and how they would move through an actual work environment.
It does this by superimposing 3D representations of its mobile elevating work platforms (MEWPs) and telehandlers on top of live video of the facility, captured by a smartphone or tablet camera. For example, app users can “drop” a machine in a specific location in its stowed configuration and then perform a simulated lift. This enables them to make accurate decisions about the machine’s maneuverability and reach the exact working environment—something that would be impossible to do with just the measurements alone.
REAL-WORLD USES
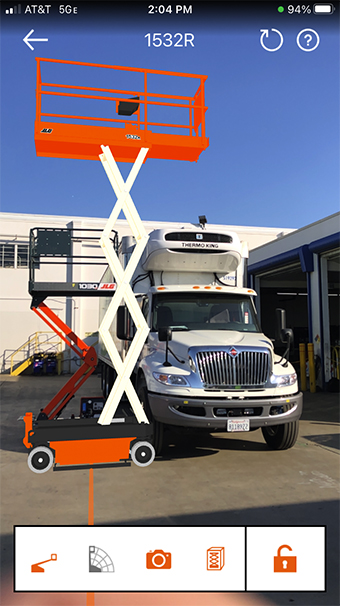
JLG’s West Coast strategic account manager, Ed Padilla, has been an early adopter of the AR app. He has watched it evolve from a cool piece of new technology to a powerful tool that makes a tremendous difference to the industrial facilities he visits.
“Some of them are replacing ladders with low-level push-around lifts, scissor lifts, boom lifts, and other types of lift equipment. But they need a lot of help understanding what’s best for their work environment,” he explains.
“Other times, they don’t have measurements for their ceiling heights. Or, they may not know exactly how high a piece of equipment can reach,” he adds. “With the AR app, we don’t need to know that. We can simply experiment with different sizes and configurations of JLG machines to determine the best reach and fit for their needs.”
Here are two real-world examples where JLG’s AR app made a big difference for Padilla and his customers.
1. SOFT DRINK DISTRIBUTOR
A soft drink distributor utilizes a fleet of rigid-frame trucks with refrigeration units mounted over the cab to deliver soft drinks to retail locations. The company’s service technicians must remove the covers of these refrigeration units to perform periodic maintenance checks on them. Historically, they have used ladders to do this work. However, they had to reach out from the side of the ladder to perform this work, creating a potentially unsafe situation for workers.
Using the JLG AR app, Padilla was able to show that a scissor lift equipped with an extension would enable a service technician to lift the work platform to a height just above the roof of the cab and then deploy the extension to reach the refrigeration units. This would better position them to do their work more easily.
2. DECK MANUFACTURER
A manufacturer of composite deck materials experienced a big increase in business during the last 2 years because many homeowners decided to add or repair decks to their homes during the pandemic.
To meet this demand, it installed additional casting and cutting equipment and conveyors within its existing facility. This caused the production area to become more crowded, making it harder to inspect and repair elevated conveyors and other machinery.
In some locations, motors, belts, piping, and conveyors occupied the space where maintenance workers were formerly able to use a scissor lift. Other areas were only accessible via ladders.
The facility also owned a 60-ft boom lift. Before the installation of additional production equipment, there was enough open floor space to position the base unit farther away from the machinery and use the boom to perform maintenance on it. But that is no longer possible with the current, more crowded production setup. In other words, this boom lift was now too large for this more crowded space.
Using the JLG AR app on a tablet, Padilla was able to experiment by virtually placing a variety of machine types and sizes in various locations on the production floor to determine which model and configuration would work best.
FIND SOLUTIONS FASTER
One of the biggest advantages of the JLG’s app is that it enables Padilla to play “What if?” with a variety of machine sizes and configurations in their work environment. He can easily envision fit and reach in ways that measuring the space and comparing those numbers to a traditional spec sheet can’t.
“In the past, I was restricted to demonstrating the machine that I towed behind my truck. Now, I’m able to show them a whole range of options and help them identify the best lifting solution for their needs. For me and my customers, digitizing the whole experience — from equipment demo’ing to project documentation — has been a game-changer,” Padilla emphasizes.
CLOSING THOUGHT
After he leaves the facility, the customer’s team members can download the AR app and continue experimenting with it on their own. “They can explore machine types and options on their own, including many of our newest models. It’s very empowering,” he concludes.
About the Author:
Ara Eckel is director of product management, connected solutions with JLG. For more, visit www.jlg.com.
Modern Contractor Solutions, November 2022
Did you enjoy this article?
Subscribe to the FREE Digital Edition of Modern Contractor Solutions magazine.
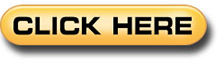