Millions of tons of recycled asphalt pavement (RAP) are used in asphalt mixtures each year, and the popularity of the product is only increasing. It makes sense. Virgin aggregate isn’t cheap, and there’s a ready supply of RAP just waiting to be used.
After it’s milled from the road, taking advantage of RAP requires special processing before it can be incorporated into asphalt mix. An important step in RAP utilization is screening to the correct spec. However, the nature of the material can present challenges such as inefficiency, blinding, and stuck-together material. High-vibration screen media can combat those issues by improving stratification, solving screening problems and reducing downtime.
Here are three key benefits of high-vibration wire screens for screening RAP.
1. GREATER EFFICIENCY
Like most aggregates processes, RAP must be sent through a crusher before it can be screened. Crushing isn’t cheap, so it pays to optimize the screening process to ensure all right-size pieces make it through the screen rather than being returned to the crusher.
High-vibration wire screens can improve screening efficiency and cut crushing costs. Some manufacturers bond the wires with polyurethane strips instead of weaving them. This allows the wires to vibrate independently under material contact, better spreading the material over the decks and improving overall stratification.
2. REDUCE BLINDING
One reason for the high value placed on RAP is because it retains much of the oil required to bond asphalt, reducing the need to add binders to create a final product. However, that beneficial feature for the final mix—combined with the fact that RAP stockpiles often absorb large amounts of moisture—translates to an abrasive and sticky product for screening. The tricky agglomeration of RAP fines leads to blinding of screen media openings. This is particularly true in warm weather.
Because of its high vibration qualities, high-vibration screen media is ideal for virtually eliminating blinding issues in most applications. The independent movement of the wires dislodges blinding material, optimizing open area for better screening.
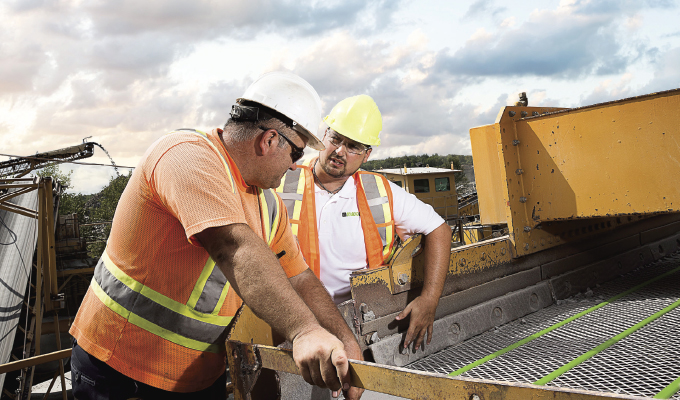
3. DISLODGE STUCK MATERIAL
Similar to the blinding problems, the sticky nature of RAP often results in material that has been crushed to size, yet sticks together. On traditional screen media this might cause pegging or improper stratification, allowing already-sized material to get kicked back to the crusher. High-vibration screen media solves this problem. The high vibration of the wires, combined with the vibration of the screen box itself, breaks apart the stuck material to be sized and sent on to the next step in the process.
CLOSING THOUGHT
RAP has a lot of potential advantages, but it takes the right equipment to get the most out of it. With screening being an important part of the process, it pays to give careful consideration to screen media choices. Plus, consider partnering with an OEM to ensure the selected screen media is the best fit for the operation.
About the Author:
Lars Bräunling is the director of screening technology with MAJOR, an innovative global manufacturer of wire screens for the aggregate, mining, and recycling industries. FLEX-MATˇ, the company’s renowned line of distinctive lime-green high vibration screens made with OPTIMUMWIREˇ ™The longest-lasting wire∫ sets the standard in lowering cost of production per ton by dramatically increasing throughput and wear life while eliminating blinding and pegging. MAJOR masters wire quality, screen manufacturing and the screening process, and provides on-site screening performance assessment and training seminars on screen maintenance and screening efficiency to help producers increase their screening performance and profitability. MAJOR is a Haver & Boecker company. For more, visit www.majorflexmat.com.
Modern Contractor Solutions, September 2022
Did you enjoy this article?
Subscribe to the FREE Digital Edition of Modern Contractor Solutions magazine.
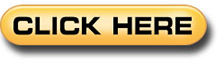