A construction project consists of multiple moving parts and customers. One change in the project’s timeline or budget can cause significant delays, making both a less than satisfied customer and construction crew. Delays in projects can cause cost overruns for the construction company and their customers not to mention the financial impacts of lost uptime.
Over the last 20 years, the telematics industry has steadily grown to meet the needs of fleets and operators by communicating real-time information and tracking specific data tied to construction trucks, including dump trucks, cement mixers, and concrete pump trucks. Gone are the days of paper-based processes.
Telematics technological advancements in the original equipment manufacturing (OEM) industry have created opportunities for solutions to some of the biggest challenges affecting construction tools and projects. Autocar has taken our advanced telematics solutions to the next level by integrating the technology with our customer experience—helping keep fleets, contractors, and their customers happy.
ADVANCED TELEMATICS TECH
The overall goal of Autocar’s advanced telematics data is for owners and operators to stay abreast of their truck’s health. For example, consider a vehicle with low tire pressure. The Autocar telematics system will alert the operator and owner via a desktop or mobile app as well as a dashboard alert that the truck’s tire pressure needs attention. The owner or operator can then take steps to solve the issue.
Additionally, Autocar’s advanced telematics provide:
- Real-time updates: Constant updates and real-time notifications such as tire pressure, spark plug malfunction, and other mechanical matters, enabling owners and operators to proactively address pressing issues
- Improved decision making: Comprehensive data analytics facilitate informed decisions regarding location, usage, routing, and other operational metrics
- Improved operator performance: Owners can track an operator’s driving behavior, which can help with increased safety measures to improve operator performance and accountability
- Proactivity: Predictive failure modeling and prognostics derived from leveraged data such as location, usage, and diagnostics
ADVANCING TELEMATICS USE
Integrating telematics into construction and other severe-duty vocational trucks aims to help trucks and their operators experience maximum uptime, reliability, and durability. In addition, fleets and construction companies using the appropriate technology can reduce the complexities associated with jobsite logistics, help improve employee productivity, and streamline day-to-day operations.
Historically, the telematics data was only worthwhile if the operator and customer monitored it. For most, the customer was responsible for ensuring they had the proper hardware and software to take care of all the data. When a problem arises, they had to handle the repairs and maintenance. This created an enormous burden on the operator and customer.
Because Autocar, LLC prides itself on its dedication to customers and its best-in-class support directly from the Autocar factory, it knew that it could offer a solution to this burden.
SPARKING AN IDEA
The idea to integrate customer experience and telematics began during a routine visit to a customer’s shop when the customer identified an issue with one of their trucks. The problem was quickly resolved after the customer was directed to submit a ticket with our direct factory support, Autocar Solutions. However, it left us thinking if there was something more we could do on our end to simplify this process by identifying and resolving the problem without the customer having to do anything.
This led to the research and development of the post-sales customer experience, including an in-depth look at ways to proactively identify trucks experiencing downtime or an issue. After identifying a code with our advanced telematics system, Autocar created a plan to use the truck’s data as a proactive servicing tool.
TELEMATICS EXPERIENCE
Telematics is seen as an essential tool for fleet managers to help them in their job, but it also opens more opportunities for customer experience. So, over the last year, we have worked to be the first OEM to take telematics a step further as a proactive solution. In turn, proactive diagnosis helps customers experience maximum uptime, improved productivity and performance and a truck that lasts to fit the construction industry’s needs.
The customer experience strategy takes the power of real-time telematics communication and offers an additional benefit to the system. Autocar’s telematics’ code can alert operators and fleets of mechanical issues with the construction truck in real time, so issues can be quickly addressed, reducing downtime. In addition, it helps to alert Autocar technicians to fix the issue across the board.
BENEFITS OF INTEGRATION
The goal of a contractor is to keep their customers’ projects on time and happy with the results. So, with telematics, customers enjoy the benefit of having a team proactively looking for ways to solve issues.
In addition, construction equipment is a significant investment for companies, so optimizing telematics is crucial for construction companies. Telematics can help construction companies manage their fleet more efficiently, allowing them to communicate with workers and track assets and resources in real time. A telematics system designed with the overall customer experience in mind has the potential to save construction firms money as well as improve their services.
CLOSING THOUGHT
Vocational truck manufacturers must tailor their offerings to the needs of their customers, including the post-sale experience and ever-changing customer demand. OEMs that already have a telematics system engineered for the best performance can take advantage of it by transforming it into another benefit. The customer experience will continue to evolve, and telematics will remain at the forefront of driving that evolution.
About the Author:
Craig Antonucci is chief experience officer with Autocar, LLC, manufacturer of severe-duty vocational trucks carrying the first specialized truck brand in North America, the only American-owned and operated original equipment manufacturer (OEM) of trucks. Autocar collaborates with customers to build trucks to their exact specifications and needs. Autocar’s purpose-built severe-service truck lines include ACMD and ACX cab-over trucks, the ACTT and its all-electric E-ACTT terminal tractors and the DC-64 Class 8 work trucks. For more, visit www.autocartruck.com.
Modern Contractor Solutions, August 2022
Did you enjoy this article?
Subscribe to the FREE Digital Edition of Modern Contractor Solutions magazine.
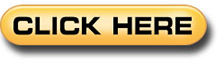