By Kevin Koberg
This article details the process Connelly Crane Rental Corp., used to choose FiberMax Crane Pads and why they decided to do so, rather than options their team previously used for ground support, including wood mats, steel crane pads, and steel plates.
THE CUSTOMER’S BUSINESS
Connelly Crane Rental Corp., Detroit, Michigan, is a 75-year-old regional crane rental company serving Michigan, Indiana, and Ohio. Its fleet includes boom trucks, RT cranes, AT and truck cranes, and crawler cranes. For years, the company had used timber mats for ground support under its larger cranes but were looking for an improved solution.
“It is important that cranes with outriggers be set up on some type of pads,” says Joe Estep, operations manager. “When it comes to crane accessories, outrigger pads are fundamental.”
CRANE PAD SOLUTION
When the company purchased a 265-ton Liebherr LTM 1220-5.2 all-terrain crane, Estep considered his options for ground support materials that would be longer lasting, easier to move, and would eliminate the need to spend $3,000 to $4,000 every few years for new mats.
For cranes the size of Connelly’s new Liebherr, DICA helped Estep understand the advantages and disadvantages to timber mats, steel crane pads, and steel plate compared to DICA’s FiberMax Crane Pads.
Wood is an organic material that easily breakdowns and needs frequent replacement: Wood mats and pads degrade, or rot, over time and the structural strength decreases as they decompose. Because of this, engineers have no way of knowing if the mats or pads are good quality or not. Wood outrigger pads must be replaced frequently. Both wood and timber cribbing are increasingly being limited by site managers. OSHA is paying closer attention to crane pads and foundation setup. OSHA has said that cranes must be setup on firm ground that’s been sufficiently drained and graded, while also using supporting gear like blocking, pads, and crane mats. For more, see OSHA 1926.1402. Using an engineered outrigger pad with known properties, although not required, makes communication with compliance officers much easier.
Steel is strong and rigid, but its primary drawbacks are weight and corrosion: Increased weight means increased transportation and labor costs. Loading out a single truck with a set of 4 steel pads is typically not cost effective. Internal welds on steel crane pads are susceptible to corrosion and fatigue and are not easily inspectable. In addition, overstressed steel can yield and suffer permanent deformation.
THE DECISION PROCESS
Estep says contractors are becoming increasingly aware of the importance of proper crane setup.
“They may not fully understand the dynamics behind it, and often request solid matting, when blocking or cribbing would suffice. However, there seems to be a trend that customers prefer to see solid mats under the outriggers,” he says.
Estep performed a cost-benefit analysis between FiberMax Crane Pads and timber mats. Because wood breaks down quickly, Estep typically replaces the timber mats every 2 to 3 years at a cost of $3,000 to $4,000 each set. In the last 15 years, he has replaced the timber mats used with the company’s larger 360-ton Liebherr at least seven times.
“That’s $25,000 to $30,000 just on wood mats, not considering the labor to configure them,” he says. “Over a 15 to 16-year span, I figured I would spend the same amount on replacing timber mats as I would on investing in the FiberMax crane pads. Plus, I will save on labor and transportation costs since the FM8x5x10 Mega Duty crane pads weigh less than 1,300 lbs, about 60% less than what we had been using previously.”
THE SOLUTION
Based on the crane’s maximum outrigger reaction force of 265,264 lbs, a 10-inch FiberMax Pad with a rated capacity of 325,000 lbs was the ideal solution. To determine the pad area our team worked with Joe to understand their typical use, ground conditions, and customer requirements. Ultimately, Connelly Crane selected the FiberMax 8ft x 5ft x 10-in (40 square feet) crane pad. Based on the pad area, their average Ground Bearing Pressure would never exceed 6,600 psf, which aligned with their objectives.” explains Kris Koberg, DICA CEO.
Benefits of FiberMax over Wood and Steel Crane Pads: Made of engineered materials, FiberMax Crane Pads will not rot, delaminate or degrade with use or exposure to the environment, have a 20+ year lifespan, and are as strong as steel. The bi-directional shear web design was originally developed for vehicle and pedestrian bridges. This innovative design allows FiberMax Pads to distribute concentrated loads over large areas and effectively reduce ground bearing pressures.
CLOSING THOUGHT
The new crane outfitted with the FiberMax Crane Pads has completed several jobs within the first month of delivery. One of those was lifting a 150,000-lb piece of machinery out of a steel factory in Dearborn, Michigan.
“The operator and crew couldn’t be happier,” says Estep, primarily because the FiberMax crane pads are easier to handle—they weigh half as much as wood and steel plate, which makes them easier to set up. The crew also says they have confidence in their setup and like that the crane pads look professional.
Based on the performance and cost savings of the FiberMax product, “This was the first set of FiberMax crane pads we’ve purchased, but they won’t be the last,” says Estep.
About the Author:
Kevin Koberg is the Marketing Director for DICA. He leads marketing and brand development in domestic and international markets. DICA is a family owned and operated company that specializes in building high performance engineered outrigger pads, crane pads, cribbing blocks, and magnetic sling protectors that are lightweight, easy to use, and long-lasting. DICA products are proudly made in the USA, ASME B30.5 compliant, and used by operators on all seven continents and 40+ countries around the world. The company delivered its first outrigger pads in 1988 and has continued to lead the way in outrigger pad product innovation since. With 30+ standard models in its product line, DICA is able to fit equipment with lifting capacities up to 500 tons or more, anywhere in the world. For more, visit dicausa.com.
Modern Contractor Solutions, September 2021
Did you enjoy this article?
Subscribe to the FREE Digital Edition of Modern Contractor Solutions magazine.
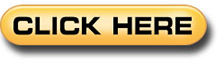