By Seth Ulmer
Adding a new tool to your fleet can be just as risky as taking on a new employee. Both require a great deal of research, time, and a monetary investment. But just like adding a new employee to the team, a new tool can also bring with it the potential for new and expanded business.
Hiring an employee who excels in a certain area of the business can increase the opportunity for success. Their expertise opens doors to jobs that the rest of the team may not have been comfortable doing. That same approach applies to construction equipment, specifically the curb and gutter market. After researching and investing in a new machine, the doors to new jobs open. By finding the right piece of new equipment, curb and gutter contractors can expand their specialties and do more work themselves without subcontracting out the work.
When looking for the right tool to expand business, it’s important to consider the cost vs. benefit of adding the tool and service. Beyond the initial expense, consider potential revenue, maintenance costs, and required employee training. In the concrete business, a walk-behind curbing machine could be the perfect solution.
WEIGHING THE OPTIONS
Like any construction endeavor, curb and gutter can be tackled with several methods. While there are many options—including large slipform pavers and hand-forming—there is rarely a one-size-fits-all approach. Contractors without experience or heavy equipment can find it difficult to track down experienced labor to sub out the job. If they do find a reputable curb company that specializes in curb and gutter work, the options may be pricey.
Dedicated contractors may have access to a large, drivable curb machine. While this efficient equipment is great for significant curb and gutter jobs, it is not economical for jobs less than 1,500 linear feet. A slipform paver can lay up to 4,000 linear feet in an 8-hour workday, but it can only be run by a highly skilled operator. Pair that with the cost of transporting the large equipment, and the costs often outweigh the benefits for smaller jobs.
On the smaller end of the scale is the hand-forming approach. Hand work is suitable for small jobs, but is slow compared to heavy equipment. Quality control is also more difficult with this method. Plus, this approach is often paired with physical strain and back-breaking labor.
In between hand-forming methods and large slipform curbing equipment lies a mid-size option: the walk-behind curbing machine. This easy-to-transport, simple-to-use option is a logical addition for contractors looking to handle curb and gutter jobs themselves and avoid the complications of subcontracting out the work.
THE PERFECT FIT
Walk-behind curbing machines provide productivity without the extreme physical labor or need for large machinery. This class of equipment provides enhanced productivity in a product that is easy to learn and simple to use, as well as being an economical option.
Unlike the larger drivable machines, walk-behind curb rollers offer ease of transport and a small footprint. The system consists of a handle, attached to a metal drum run by a hydraulic power source. The single-operator machine takes most of the back-breaking work out of curb and gutter, while producing a consistent, high-quality finished product. The equipment is intuitive to use, making it accessible for workers who might not have as much experience.
With low initial investment and minimal maintenance, a walk-behind curbing machine offers a fast ROI and a quick way to boost profits. Whether a contractor is looking to take on new jobs or improve the efficiency of current offerings, the equipment can be a smart addition to a fleet.
SAVING TIME & MONEY
Most common in curb and gutter projects ranging from 50 to 5,000 linear feet, a walk-behind machine can help a crew accomplish curb forming work up to 50% faster than by hand. With hand-held tools, crews can pour and finish up to 600 feet in an 8-hour day. However, with a walk-behind machine, they can pour and finish up to 2,000 feet in a day. Plus, a crew can accomplish the job with half as many workers and with less physical strain on the crew. These factors allow a walk-behind curb roller to pay for itself after just 1,200 feet.
Taking on curb work in-house can save tremendously on the margins of subbing out the work. Besides that, and perhaps more importantly, it gives companies the ability to self-perform this previously tedious curb and gutter work and keeps the job moving without holdups. Many jobs only allow for a certain number of days to complete the work, and any time over results in a penalty. By self-performing all aspects of the job, there is no need to wait on an additional crew and face the potential risk of paying a daily penalty for incomplete work.
Contractors can save on the cost of subcontracting and open the door to potential money-making opportunities by taking on curb and gutter work with an in-house crew. The cost of installing curb and gutter varies by city. If 200 feet of 6-inch-by-18-inch concrete curb costs $2,500 in labor and materials, five 200-foot jobs in a month would equate to $12,500. That can either be considered as profit from new opportunities, or savings from not having to hire a subcontractor.
Utilizing their existing crew, contractors can save on labor costs by using a walk-behind curb roller. When compared to a manual method or face forming, crews can pull curb and gutter twice as fast with half as many workers. And because of the intuitive, straightforward operation, it only takes a few minutes to train them on the equipment. Some machines of this kind feature an ergonomic design and a pivoting handle to provide a comfortable offset tailored to the height of the operator. The operator then walks outside of the framework parallel to the form while pulling the concrete.
Another benefit to a walk-behind curb forming machine is the flexibility when working with concrete. Having a fast-moving process is important because of the slump requirements for curb work. The walk-behind drum option lets the workers control the speed of the machine, making it easy to keep a close eye on the concrete itself. This also allows a worker to add water if the slump is too low and the concrete is too dry. On the other hand, if the slump is too high, a skilled concrete worker will know to let the material sit to dry out for a while before forming. Because of the slump calculations that a curbing machine requires—usually 3- 4-inch slump—it offers a longer time of workability and allows for finish work or touchups.
Additionally, a walk-behind curbing machine is easy to clean and requires almost no maintenance. Unlike larger equipment that might require a significant amount of time spent on cleanup, curb rollers can be simply rolled in the grass and wiped down. Its lightweight nature makes it easy for two workers to lift the equipment into a truck bed, eliminating the need for additional transportation accommodations like a trailer.
CLOSING THOUGHT
Whether a contractor is looking to expand their equipment offerings from large to smaller or vice versa, a mid-size piece of equipment like a walk-behind curbing machine can be a smart choice. From the largest company to the smallest two- or three-man operation, the equipment allows for expanded profits each time crews take on a curb and gutter job. Similar to the hiring process, selecting the right equipment to fit the bill requires time and research, but the increased job potential and ROI make the effort worth it.
About The Author
Seth Ulmer is the sales manager at Curb Roller Manufacturing, a world leader in shaped concrete roller screeds. Ulmer joined Curb Roller Manufacturing after spending over a decade in the concrete and construction industries. For more, visit www.curbroller.com.
Modern Contractor Solutions, May 2021
Did you enjoy this article?
Subscribe to the FREE Digital Edition of Modern Contractor Solutions magazine.
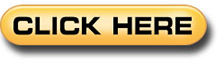