C & H Paving Inc. has been operating a granite quarry in Sparta, Georgia, for less than one year. As a paving company requiring a steady source of aggregates, C & H Paving recently decided to produce its own material. By removing the need for an external supplier and leveraging Metso’s mobile, tracked equipment, C & H Paving has been able to drastically reduce costs and grow new business.
Around 6 months into his new quarry operation, Benji Cranford, owner of C & H Paving, recalls the decision to be his own aggregate supplier for his full-time paving company. The opportunity to remove the middle man, cut costs, and work at a faster pace all aided in his decision.
“I was wanting to keep most of my profit at home and to try to save more money internally,” Cranford begins. “So far, it’s been a good decision on my part.”
Working with his Metso distributor, Yancey Bros. Co., Cranford describes the easy decision to choose Metso Lokotrack® for his growing operation: “Every piece we bought is portable, and that was a big deal for me. We started crushing in the pit, and now we’ve moved out of the pit up here where we are now, so just being mobile was a big key for me.”
END-TO-END PROCESS
The rock is first moved out of the pit, onto a truck, and hauled to the crushing site. Then, the rock is moved into a Lokotrack LT106™ jaw crusher. From the jaw crusher, the material is fed into an ST2.8™ scalper screen. From the scalper screen, the material goes into a Lokotrack LT200HP™ cone crusher, and then to a Metso ST4.8™ mobile screen with washer attachment for cleaning. After cleaning, the screen separates the rock into three different forms. The overs move to a second LT200HP™ cone crusher, which circles around back to the screen.
Jason Cash, crushing crew foreman for Cranford, explains the varied classifications of materials produced from the quarry: “Our finishing products are 89s, which we use an abundant amount in asphalt. We use the M10s, the W10s, the 57s—we break those down into 5s, 6s, and 7s.”
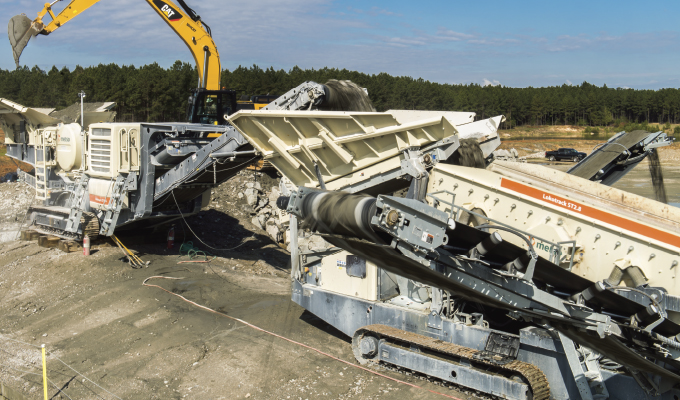
AUTOMATION TECHNOLOGY
As a business owner needing easily movable equipment, Metso’s IC™ Series automation technology adds a layer of ease as well as precision. The automation technology provides single-button startup and interlocks Metso mobile plants with each other, so that the material flow remains stable.
“Everything talks to one another, and it just makes more production. And at the end of the day, it saves labor and time for everybody,” explains Cranford. “You don’t have any clogs or backups. It just makes everything simpler to manage and keeps all of the equipment moving.”
“My experience with Metso equipment is that it’s pretty much hands-on, it’s easy to use,” agrees Cash. “The whole process of operating the equipment is much easier than other brands that I’ve used.”
HANDS-ON EQUIPMENT
Being able to start a crushing and screening operation quickly and reliably was possible with Metso Lokotrack®. Now, the operation will continue with dependable support from Metso and the distributor Yancey Bros. Co. Cash explains, “The call response is so fast. Parts ordering is on time, every time.”
CLOSING THOUGHT
A complete portable crushing system can make all the difference for projects where materials can be recycled and used versus being hauled off as waste
For more information
For more information about Metso and its portable crushing solutions, visit www.metso.com.
Modern Contractor Solutions, October 2019
Did you enjoy this article?
Subscribe to the FREE Digital Edition of Modern Contractor Solutions magazine.
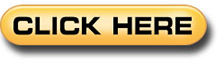