Part 1: Lessons learned using insulating concrete form construction
Samer Chaya recently constructed his first building using ICF’s (insulating concrete forms). It’s a medium-size (10,000 sf) building, office space for his own company, Royalton Homes, a residential construction contractor in Collingwood, Ontario, Canada. Royalton will occupy 25 percent of it, and lease out the rest. Chaya, vice president of Royalton, was closely involved with every phase of the project and he’s ready to share what he learned about ICF construction.
WHY ICF’S?
ICF construction is essentially a cast-in-place concrete building that is formed using blocks of expanded polystyrene (EPS) foam, which stay in place after forming and insulate the building.
The benefits that attracted Royalton most were the energy savings due to the high insulating value of the form, the air-tightness of cast-in-place concrete construction, and the solidity and durability of a concrete building.
As an owner, he not only wanted those properties, but was prepared to pay extra for them. He initially estimated that it would cost 30-percent more than wood frame construction. It later turned out to be only 15 to 18 percent.
The high energy-savings come partly from using a new ICF product that features thicker insulation than conventional ICF’s. Plus 3-30 block—made by Amvic, one of the leading North American ICF manufacturers—feature 3.25 inches of expanded polystyrene (EPS) on each side of the concrete, as compared with the usual 2.5-inch blocks that have dominated the industry until now. The doubled 3.25 inches of foam achieve an insulating value of R-30, as compared to the industry standard R-22.
THE PROJECT
The project is a two-story building with a relatively square footprint. The foundation was excavated, but after construction it was backfilled inside and out, so there is no basement and the first floor slab is on grade.
The foundation was formed using conventional 2.5-inch ICF blocks (also from Amvic). These were only used for the basement level, up to the brick ledge block at grade level. Above-grade walls were formed using a new, thicker 3.25-inch block.
ICF’s consist of two molded slabs of EPS, joined into a hollow-center block by strong webs of plastic. The EPS pieces have patterns of bumps on top that mate to indentations on the bottom for solid stacking and correct alignment. There are straight block, corners, and a few specialty shapes, such as brick-ledge.
The basics are simple. Blocks are stacked up to build walls. Rebar is inserted vertically between the webs, and horizontally across them. Then concrete is poured in. When it cures, it is a solid, continuous concrete wall with 3.25 inches of continuous foam insulation on both sides. Exterior and interior finishes can be applied directly to the block.
CHALLENGES
Chaya discovered that the main construction challenges had to do, in one way or another, with the weight and pressure of wet concrete.
The main budget challenges sprang from improper planning for the specifics of the ICF system, a pure problem of inexperience.
Royalton’s building had already been designed when the decision to use ICF was made. Looking back, that’s the first thing Chaya would do differently.
“I would design to the dimensions of ICF blocks, so I’d have less cutting.” He cites several examples.
ICF blocks are 16-inches high. The height of the original windows didn’t work out to an exact number of blocks, so they’d have to cut blocks to make the wall meet the window, with a lot of waste. They changed the window height slightly so they could cut blocks in perfect halves, and save money by using the other half on another window.
Blocks are normally stacked with staggered joints to increase the strength of the form, like brick construction. The length of Royalton’s building walls didn’t work out in whole-block lengths, though, and they ended up with a straight (not staggered) joint all the way up the wall.
This is a situation where the weight of concrete comes into play. Concrete weighs about 140 pounds per cubic foot, more than twice the weight of water. While it’s fluid, it applies a lot of pressure to the forms. ICFs get their strength from the thickness of EPS and the rigid plastic webs embedded every 6 or 8 inches in both blocks, that hold the EPS slabs together.
Staggered joints interlock the layers of block and can bear the load of concrete. Along a straight joint, there is nothing to hold adjacent blocks together, so the wet concrete would push the building apart.
The joint needed to be braced with 2 feet of plywood screwed into the ICF’s. Braces, as well as wall finishes, are screwed into the ends of the webs for solid anchoring. After the concrete was poured and cured, they removed the plywood.
If he had designed the building with ICF in mind, says Chaya, “I would have made the building 6 inches longer, or 6 inches shorter, to avoid having that kind of joint. Use the dimensions of the block you’re buying to guide design.” ■
Look for Part 2 in next month’s issue featuring more lessons from Royalton’s first ICF project.
About The Author:Steven H. Miller is an award-winning writer and photographer, and a marketing consultant specializing in issues of the construction industry. He can be reached at steve@metaphorce.com.
_________________________________________________________________________
Modern Contractor Solutions, April 2013
Did you enjoy this article?
Subscribe to the FREE Digital Edition of Modern Contractor Solutions magazine.
Take it from me…
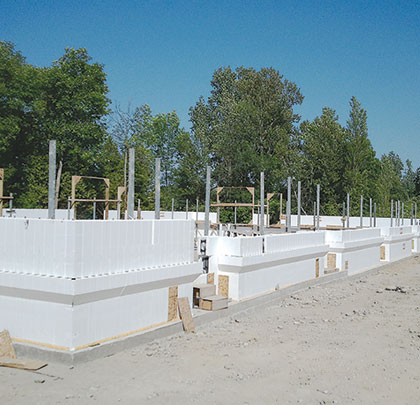