Arkansas highway project shows potential for automated grade control throughout entire pavement cross-section
Starting in late summer 2012, Weaver-Bailey Contractors, El Paso, Arkansas, began constructing a four-lane, 6-mile stretch of Highway 67 near Cash, Arkansas. The contractor trimmed an average of 4 inches of topsoil from the subgrade, constructed a 6-inch layer of Cement Stabilized Crushed Stone Base (CSCSB), had a 1-inch-thick asphalt bond-breaker installed to prevent overlay cracking, and planned to overlay the bond-breaker with a 10-inch layer of concrete pavement.
The new stretch of Highway 67 is replacing “Old Highway 67” between Cash and the city of Hoxie to the north. The turnkey project, which will see the highway open when all of the bridges and other work are completed, is expected to be finished in late 2013 or early 2014.
MUCH LESS COSTLY
Jamie McAnelly, project superintendent with Weaver-Bailey, noted in mid-November 2012 that the objective was to get the subgrade and CSCSB work completed as soon as possible so as to allow paving without major cold weather delays. By then, 50 percent of the trimming was complete; about 53,000 cubic yards of material would be removed eventually on the entire project area.
Trench Safety & Supply, Inc., North Little Rock, Arkansas, and representatives from Topcon Positioning Systems equipped a Gomaco 9500 dirt trimmer with a Millimeter GPS+ automated grade control system to fine-grade the subgrade.
This was not the first time that Weaver-Bailey had used this automated grade control system on a trimmer, but it was the first time that the contractor had done such trimming work in entirely stakeless and stringless fashion.
McAnelly looked forward to using the system on the Vögele paver to control the CSCSB grade, having seen Weaver-Bailey’s first stringless trimming work. “We have actually used a rod and level to verify some of our grades, and we were within two- to three-hundredths, with many places having dead-on perfect grade,” he says.
To McAnelly, time is money when it comes to minimizing paving time. “It’s not just materials,” he says. “The stringline, you don’t think that’s very expensive, but that’s a consumable that you no longer have to purchase. That and pins—there are a ton of pins. We’d be putting the pins in every 30 feet for 6.5 miles—that’s a lot of pins and lot of expense right there in itself.”
When it comes to employing stakeless, stringless automated grade control systems, system quality control takes on increased importance, McAnelly notes. “There’s a phrase we use a lot out here when using this equipment: garbage in, garbage out,” he says. “If your control points aren’t properly set, if your lasers aren’t properly set up, if the numbers on your machine aren’t properly set up, you’re going to get an improperly done product.” Checking these items can result in less downtime overall, he adds.
Ensuring system reliability can impact the bottom line in a big way, McAnelly contends. He estimates that the use of stakeless, stringless technologies reduces labor hours by at least 40 percent on a project like Highway 67. It’s a case of technology allowing professionals to focus their efforts on managing outcomes rather than manual labor routines.
MORE EFFICIENT PAVING
Weaver-Bailey also planned to use the dual-antenna automated grade control system on a two-track Gomaco PS-2600 Placer/Spreader and a Gomaco GHP-2800 four-track slipform paver while placing the concrete overlay, starting in late 2012 or early 2013. The system controls both pavement elevation and steering on the machines.
To maintain a high level of productivity, Weaver-Bailey planned to use dump trucks to place fresh concrete from an on-site plant onto the CSCSB, ahead of the placer/spreader, which places the material to a “rough” elevation using its pan and an auger to spread it on either side of the machine to maintain a pavement width of 26 feet, allowing for 12-foot lanes, plus 2 feet of shoulder on the outside of the right lane. The concrete has a better workability by the time the paver processes the material a few seconds later using two machines.
Roger Weaver, paving superintendent with Weaver-Bailey, points out that setting stringline on either side of the machine for pavement in both directions would require about 25 miles of stringline. “That, right there, is a pretty considerable investment in time, manpower, and material,” he says.
The slipform paver provided a finish edge to the pavement and used hydraulic vibrators on the front of the paver, rather than a vibrating screed like that used on the Vögele paver, to eliminate air pockets. The machine also placed dowel bars every 15 feet.
“If everything is working right, we have to pause at about 1,500 linear feet without any problems on a good day,” he says. “If we did it the old way, we’d do less than half of that and it wouldn’t be nearly as close
to grade.” ■
About The Author:Don Talend, Write Results Inc., West Dundee, Illinois, is a print and e-communications content developer specializing in covering construction, technology, and innovation.
_________________________________________________________________________
Modern Contractor Solutions, April 2013
Did you enjoy this article?
Subscribe to the FREE Digital Edition of Modern Contractor Solutions magazine.
Full-Depth Grade Control
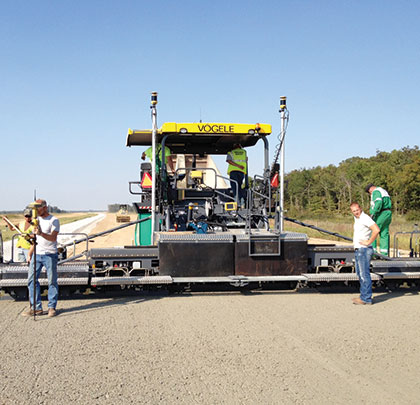