Cleveland, Ohio’s award-winning Great Lakes Brewing Company (GLBC) produces a variety of year-round and specialty “seasonal” beers which are very popular around the Great Lakes region and, where available, throughout the rest of the country. Indeed, the brewery’s annual, much-anticipated release of the highly sought-after Christmas Ale attracts droves of consumers who quickly buy up all available supply as soon as it goes on sale. The high demand of GLBC’s top selling brews prompted the company to invest in an expansion.
GLBC has been growing in profit by leaps and bounds, so they made the decision back in late 2013 to undertake a $7 million expansion of the brewery’s tanks to take place in 2014. “The decision was based on our 20 percent growth in 2013, plus future plans to expand to new markets, while meeting growing demand in existing markets,” says Greg Lemermeier, manager of engineering and technology for GLBC. With such an expansion, the company could better serve its growing customer base.
MEETING PROJECT CHALLENGES
The challenge? The brewery is in a tightly packed, urban area, and installation of the four new tanks would take place on the edge of a busy parking lot. There would be close-by buildings, vehicles, and overhead power lines to tackle in this project. The timeframe would be tight due to permit restrictions and GLBC would have to work with neighboring businesses to utilize the parking lot and create a safe working space for the expansion.
The project, handled in phases during the summer of 2014, would take an entire year in planning and execution. GLBC first called on Superior Erection to assist with rigging and setting the new tanks. The expansion began with two new 600 bbl (18,000 gallon) Brite storage tanks, which hold finished beer that is ready for packaging. Each Brite storage tank was twice the size of the brewery’s older storage tanks, literally quadrupling the brewery’s storage capacity. GLBC expects the two tanks to last 2-3 years, depending on future expansion.
For the next phase, GLBC required the installation of four new 600 bbl fermentation tanks. The new fermenters would hold the brewery’s most popular, high-volume beers; these include Dortmunder Gold® Lager, a smooth lager balancing sweet malt and dry hop flavors, and Burning River, a pale ale with citrusy and piney hops.
Because finished beer has to be chilled when stored, and with an increased need for cooling due to the new tanks, the brewery had to upgrade to a new chiller. In order to upgrade, GLBC first had to remove the two old chillers from the brewery’s roof. Superior installed the steel work and rigged the new, massive chiller into place. The new chiller came in at three times the size of the two old chillers combined.
PERMITS, SAFETY, AND COMMUNITY TEAMWORK
To install the new Brites, fermenters, and chiller, the brewery needed to take over part of the adjacent parking lot. Superior and GLBC worked with the lot’s owners on scheduling temporary closure of the lot, including compensation for lost parking revenue during that time. They also had to work around the schedule of the nearby, very popular West Side Market, a destination for locals and out-of-towners, alike.
Because of the size of the tanks and the nature of work to be performed in lifting and setting them into place, GLBC and Superior obtained numerous permits, escorts, and even permission to close nearby roads at times, to ensure safety of visitors, cars, and other businesses in the area. And they were on a tight timeline—the city could only issue permits for a day at a time, so when closures were in place, the team had to work quickly.
For the Brite tanks and fermenters, Superior used a 250-ton Grove GMK crane with a 50-ton Grove TMS acting as an assist crane in lifting and tilting each tank into the upright position with a tight, 125-foot radius. The 250-ton crane then set the tanks up vertically, and lowered each through the roof’s open hatch onto wheeled skates. Once set upright, the crew wheeled the tanks into their final positions.
READY IN THE NICK OF TIME
Everything went as planned, and the brewery proceeded with the rest of the project, including new electrical work and mechanical install of process piping. The new tanks were operational just before Christmas of 2014.
“This was our first time working with Superior. They were recommended by a general contractor and were great to work with,” says Lemermeier. “Through the various stages of the project, they have had several different crews out and all have been professional, efficient, and very flexible with the various changes and surprises that tend to come up on complex projects. They were also very safety conscious, and always followed our safety guidelines. We plan on working with them in the future.”
As GLBC’s popularity continues to expand, the increased capacity has helped ensure that the future is bright for the brewery—and that cold beer flows freely from the taps. ■
For More Information: For more than 50 years, Superior Erection has provided skilled millwright, maintenance, rigging, steel erection, and machinery-moving services to companies requiring precision industrial carpentry services. From machinery repairs to rebuilds, testing or maintenance, Superior Erection’s professionally trained millwrights can maintain or repair virtually any equipment—at your location or on any jobsite. For more information, email sales@superiorerection.com, or visit www.superiorerection.com.
_________________________________________________________________________
Modern Contractor Solutions – January 2016
Did you enjoy this article?
Subscribe to the FREE Digital Edition of Modern Contractor Solutions magazine.
Brewery Expansion
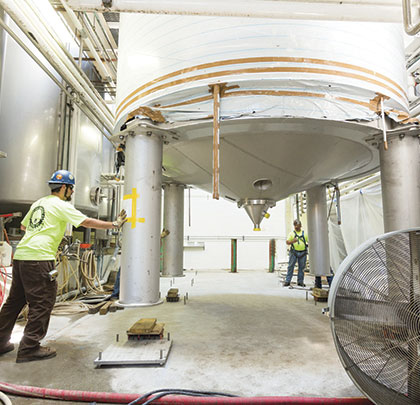