Superior Steel is one of the top steel erectors of its size in the country. Founded in 1978 and based in Knoxville, Tennessee, the award-winning company is uniquely equipped to cater to the precise needs and demands of field superintendents and construction project managers because Superior does it all: engineering, fabrication, and erection.
Superior assists customers with design-build projects and has American Institute of Steel Construction (AISC)-certified fabrication facilities with the capacity to produce more than 18,000 tons of fabricated steel annually. As an AISC-Certified Erector, Superior Steel’s erection division has the equipment to solve most any lifting challenge, whether it’s a 40-ton crane to erect a small project or three 150-ton cranes to simultaneously lift trusses at a C5 hangar or the Kentucky Expo Center. Among Superior Steel’s 150 employees are experienced, full-time personnel who maintain, transport, and set up the company’s cranes, allowing Superior to quickly respond to customer needs.
“We can help customers do whatever they need. We fab our own steel, we erect our own steel, and we detail our own steel. We’ve got structural engineers in-house. We’ve got our own trucking,” Superior Steel general superintendent Robert Human says. “We just do it all.”
MEETING DEMAND FOR LARGE PROJECTS
Superior Steel, at any one time, may be working on 10 or more projects across the country, specializing in large industrial and commercial facilities, such as museums, theme parks, stadiums, aircraft hangars, government structures, universities, hospitals, and churches.
Keeping on schedule with so many large-scale projects makes productivity and efficiency key for Superior Steel, which employs about 40 welding operators. To help meet customer demand and gain a competitive edge in completing jobs—while also maintaining quality to meet weld code requirements—the company, with help from Holston Gases, recently purchased multiple Miller® Big Blue® 800 Duo Pro diesel engine-driven welder/generators. The upgrade has helped Superior increase productivity with fewer machines, reduce costs, and save space on crowded jobsites.
Superior uses the machines for welding and power generation capabilities on structural steel erection jobsites. The welder/generators can be used by multiple operators at once—saving space by maximizing equipment capabilities with fewer machines needed on site. The machine provides 800 amps for a single welding operator, 400 amps each for two welding operators, or it can be used as a three or more arc multi-operator machine with the addition of inverter-based welders that can be powered off the unit’s auxiliary power. Operators can also use the welder/generator to simultaneously power tools such as lights, saws, drills, grinders, and fans—with no arc interaction.
“It saves you money on jobsites when you can have more than one welder working off the same machine. You don’t have to keep purchasing welder after welder,” Human says. “It saves a lot on maintenance, filters, and oil changes—it’s a big savings.”
ONE MACHINE FOR MULTIPLE OPERATORS
One of the main advantages for Superior is the ability to be more productive with multi-operator machines that meet many jobsite needs. It helps the company complete jobs faster, with less equipment on site, and maximizes investment in equipment.
Superior Steel primarily uses the machines with two welding operators simultaneously for stick and flux-cored welding, ranging from quarter-inch fillet welds on a perimeter angle to full penetration welds up to 2-inches thick. A current job involves welding steel columns that weigh 26,000 pounds each, with flanges 2-inches thick. The power capabilities of the machine—800 amps for a single weld operator or 400 amps each for two operators, with 20,000 watts of continuous three-phase auxiliary power and 12,000 watts of continuous single-phase power—are important for the types of critical welds Superior completes.
“That’s the good part about these machines—instead of having two machines for two guys to weld, we’ve got one machine running with two guys working off of it,” says Jack Freytag, superintendent and foreman with Superior. “We might also be running it for external power for grinders, screw guns, and anything else. It doesn’t cause the arc to fluctuate. You’ve got a more constant flow with this machine.”
The power generation capabilities of the welder/generators are important on Superior’s jobsites, which often don’t have available power.
“You’ve got to supply your own power and these welders come in handy because they’ve got their own generators that supply power,” Human says.
It’s important for Superior Steel to meet customer demands, which, these days, often includes shortened time frames for completing jobs. A welder/generator with dual-operator capabilities helps the company get those jobs done on time and remain competitive.
“Having the equipment that will help you to move along and get a better production level, it’s a must,” Freytag says. “It allows us to perform these jobs, bigger jobs, and more complex jobs in a timely manner. You can do the job faster and with less equipment. That’s the end game, is to turn these projects over as fast as you can and move on to the next project.” ■
About the Author: Ben Froland is a product manager, industrial engine drive, with Miller Electric Mfg. Co. For more information, visit www.millerwelds.
_________________________________________________________________________
Modern Contractor Solutions – December 2015
Did you enjoy this article?
Subscribe to the FREE Digital Edition of Modern Contractor Solutions magazine.
Meeting Jobsite Needs
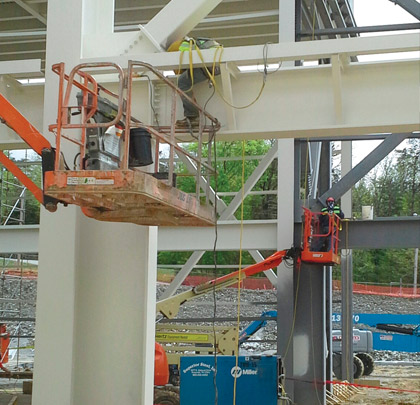