Your HDD operation is only as strong as the tools in your shed. One broken piece in a drill string can stall your job … as time slips away and labor costs continue to mount. However, predicting whether or not a piece of equipment will fail becomes a much easier task when you know what to look for. Here are five telltale signs that your HDD tooling needs to be replaced.
MISSING CARBIDES
Since carbides are literally on the front lines of the job, they’re the first to show wear. Be on the lookout for missing, chipped, cracked, or worn carbides, as well as damage to the steel that holds the carbides in place. This type of deterioration can translate directly into lost income. If only 50 percent of your carbides are present and functioning, you’ll be drilling at half speed. On top of that, missing carbides can expose the metal to more wear. If left unattended for too long, you’ll etch gaps between the cutters that won’t be
DIAMETER SHRINKAGE
Use a micrometer and calipers to measure the diameter shrinkage of the rotating components of your drill string, including drill housings, reamers and drill rods. Be sure to also closely inspect the connector pieces at the base of your drill housings to see if there has been a reduction in size. Make sure you catch thinning early to prevent damage from extending to the body of the reamer or drill bit, which is a much more expensive repair or replacement. Over time, all components will start to experience a narrowing, but anything over 10-15% opens up the possibility of failure.
UNEVEN WEAR
Perform frequent visual inspections of your equipment, looking for signs of uneven wear. Uneven abrasion distribution creates weak points that are prone to breakage. Check the area where your reamer attaches to the starter rod / quick disconnect. Be on the lookout for a belly on the shaft or a circular wear pattern. Measure the diameter with a micrometer: it will be easy to see the difference between where it starts “ganging up” on the metal. Also check the spots between the carbides on drill bits. Worn steel in the gaps will expose more carbide area, increasing the likelihood that they’ll snap off. Check threads on your drill pipe, too, looking closely with a flashlight for flat or galled threads or thread profiles that are sharp. Make sure male and female couplings line up easily, and that there are no chips, rocks, sharp edges or warped shoulders. Others signs that your pipe threads are shot are when pipe won’t break apart easily, or if you see water leakage at connection points.
ERRATIC TOOL BEHAVIOR
Be aware of performance changes in your tooling. When things start acting weird, it’s a sign to stop and take a closer look. For example, water jetting out of a housing in unexpected places can indicate the presence of a hairline crack. Failure to stop the job and swap out tooling could lead to more serious damage to the transmitter inside. Pay close attention to sudden changes in “feel”. If you’re drilling at the same speed without any change in ground condition, or your mixture is unchanged and you suddenly start bogging down or your drill starts jumping, it’s a signal to stop and inspect your equipment. Something has altered the bit or reamer and caused it to malfunction. It’s your job to determine what.
STRANGE NOISES
Your equipment will not only feel different when there’s a problem, it will probably sound different, too. When you’ve lost some carbide cutters, you’ll hear a metaling “tinging” sound down rod as metal connects with rock, instead of carbide-to-rock. Lack of noise can indicate a problem as well. Sudden dropping out of sound could mean that for some reason you’re just rotating and no longer cutting. All sounds that are out of the ordinary indicate that some aspect of your equipment has changed. It pays to take a look.
REPAIR OR REPLACE?
In this line of work, nothing lasts forever. HDD equipment undergoes a ton of stress, so it’s a given that you’ll need to invest in your tooling. It’s just a part of the cost of doing business. When signs of wear or damage start to emerge, it will likely be cheaper to repair first. However, there will come a point when the cost to repair the tool is higher than the cost to replace it. Remember, when calculating your repair costs, take into consideration not just the repair itself, but the time and labor costs you absorb when your crews are idle. Once that threshold is crossed, scrap the tool and invest in a new one.
Continuing to operate with tired tooling always has a consequence. Slower progress equals more time and less money. The more wear you put on a tool before fixing it can mean a more expensive repair job down the line—or may result in the need to replace the tool altogether. Don’t wait until your situation becomes dire. Keep an eye (and ear and grip) on your tools and take a closer look when the first sign of a potential issue becomes apparent. Addressing weak links right away will keep your operation moving forward.
About the authors:
José Mierzejewski celebrated his 20th anniversary with Melfred Borzall this past year. Over the past two decades, he has worked hands-on with engineering some of HDD’s most productive bits and tooling and is now working face-to-face managing the salesforce.
Most of Heath Mellow’s 25 years in the HDD industry are in dirty boots on the ground as a driller and locator. Joining the Melfred Borzall sales team last year, Heath now calls on drillers from central to northern California. For more information, visit www.melfredborzall.com.
Modern Contractor Solutions, December 2018
Did you enjoy this article?
Subscribe to the FREE Digital Edition of Modern Contractor Solutions magazine.
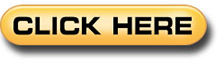