Safety and health programs are recommended for all workplaces—from office buildings and construction jobsites to dairy farms and other industrial settings. These workplace safety programs protect your employees and empower them to confidently complete tasks without fear of injury or death.
Besides the most devastating (and incalculable) cost of a human life, OSHA states that businesses spend nearly $170 billion per year on costs associated with workplace injuries and illnesses. But companies that develop effective safety and health programs can cut those costs by anywhere from 20 to 40 percent. Combine that decrease in costs with the less quantifiable benefits of higher morale, better productivity, and improved reputation, and the benefits of implementing a company safety program become even more compelling.
SAFETY CULTURE
Creating a culture of safety can be difficult, but there are five key elements that must be present for a safety and health program to get off the ground.
EMPLOYEE TRAINING AND EMPOWERMENT
Before you can expect employees to follow best practices, you must educate them and empower them to hold each other accountable. Dedicate a day to safety training when you share safety tips and plan activities that keep your employees interested. There are plenty of online safety training ideas and resources to help get you started.
As far as accountability goes, consider implementing a policy such as stop-work authority, which gives any employee (regardless of job title) the ability to stop a task if it becomes risky. Putting safety in the hands of every worker can help you foster accountability at all levels of your organization.
HAZARD IDENTIFICATION AND CONTROL SYSTEMS
Once your employees are trained, a safety management process must be put in place for them to easily identify hazards and take steps to contain them. For example, if workers will use an aerial lift on a job site, hazards like power lines and uneven ground should be identified and addressed before any work is done.
It’s true that not all hazards can be eliminated, but most can be controlled. For each hazard you identify, try following the hierarchy of controls to ensure you’ve done everything you can to keep workers safe on the job.
FOCUS ON COMPLIANCE
Organizations like the Occupational Safety & Health Administration (OSHA) and the American National Standards Institute (ANSI) were created to keep workers safe and promote jobsite safety. They outline best practices for all types of jobs and, in the case of OSHA, each best practice is actually a law.
Complying with OSHA’s regulations is the best way to ensure you’re doing everything you can to keep your workers safe. They even provide compliance resources organized by industry as well as email newsletters and a searchable database by safety topic.
CONTINUOUS IMPROVEMENT
Safety and health programs don’t fall into the “set it and forget it” category. Not only are new regulations being released all the time, but new employees will join your team. Thus, it’s important to adopt a continuous improvement mindset when it comes to safety.
Hold frequent safety meetings, retrain more tenured employees as you train new hires, and consider doing a full safety and health program audit each year. Also, encourage employees to share their concerns with you. These concerns can most likely be turned into safety topics that will resonate with your entire team.
LEADERSHIP AND ORGANIZATIONAL BUY-IN
For a safety and health program to be effective, there must be institutional buy-in from the top down. Workers will be faced with situations every day that force them to decide between a safe course of action and an unsafe one. Good safety leaders motivate workers to make the right decision even when no one is watching.
Like all forms of leadership, becoming a good safety leader starts with honest, consistent communication. Set high but attainable standards for your team. Offer an incentive for following your organization’s safety management system. And, if an incident that requires disciplinary action occurs, always communicate the “why” along with the “what” when addressing it.
THE SAFETY MANAGER ROLE
Though safety leadership roles may be taken on by various workers, a safety manager is typically the official face of safety within an organization. Safety managers try to minimize workplace injuries and illnesses by training workers, staying up-to-date on current safety news, writing policies, and ensuring compliance.
What is a safety manager’s job role?
The responsibilities of a safety manager vary by industry, but generally they are responsible for:
- Identifying and monitoring health and safety hazards within the workplace
- Training employees to minimize and/or avoid any risks associated with their jobs
- Reviewing health and safety legislation to ensure compliance with the most recent standards
- Performing safety inspections of the workplace environment
- Writing workplace-specific safety policies and best practices
- Coordinating emergency drills and procedures
For more information:
JLG Industries, Inc. is the world’s leading designer, manufacturer, and marketer of access equipment. The Company’s diverse product portfolio includes leading brands such as JLG® aerial work platforms; JLG, SkyTrak® and Lull® telehandlers; and an array of complementary accessories that increase the versatility and efficiency of these products. JLG is an Oshkosh Corporation Company [NYSE: OSK]. This article was originally published by JLG Industries: www.jlg.com.
Modern Contractor Solutions, December 2018
Did you enjoy this article?
Subscribe to the FREE Digital Edition of Modern Contractor Solutions magazine.
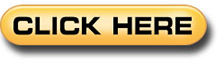