One certainty in our time of technological advances is that things continually change. Fifty years ago, automobiles were built on assembly lines manned by individuals completing particular tasks. Now, robotic equipment controlled by computers occupies many of the same assembly line positions, in some cases completing multiple tasks.
The construction industry is no different and is equally affected by technological advances. Take the predominate use of building information modeling (BIM) in construction today. Twenty years ago, BIM was not a blip on the screen. Some say the same is true for utilizing 3D printing in construction.
The general idea behind 3D printing is rather simple: A CAD model directs the printer to apply successive layers of material, or “ink,” to produce a particular shape. The details are much more complicated and beyond the scope of this discussion. That being said, 3D printing is a technological advancement that potentially provides a new horizon for the construction industry.
3D PRINTING IN CONSTRUCTION
3D printing has been experimented with by some construction industry participants to fabricate pieces of a larger finished product. Recently, a Chinese company named WinSun Decoration Design Engineering claimed to have printed 10 homes in 24 hours. The material used to print the homes was a mixture of cement and glass fibers. The process was completed by printing sections of the walls and ceiling for each individual home and connecting each section in a predetermined configuration in order to create four walls and a roof. What makes the 3D printed walls so unique is that each wall is not one solid unit of concrete. Rather, the CAD model produced wall sections that could accommodate plumbing and electrical components. The walls were also designed to act as the homes’ insulation. WinSun claimed that the cost of 3D printing the homes was about half as much as traditional construction processes.
In other parts of the world, companies are taking on experiments with 3D printing in construction. One Dutch architectural firm has committed to constructing an entire building with a 3D printer. The firm, Dus Architects, suggests that it could print a 13-room building using its 3D printer. Additionally, Skanska and Foster + Partners, in a collaborative agreement with the United Kingdom’s Loughborough University, received a license from Loughborough’s School of Civil and Building Engineering to use its 3D printer to determine its utility in real-world applications. Skanska and Foster + Partners are also collaborating with other parties in the construction industry to develop a 3D printing supply chain.
IS IT GREEN?
Some tout 3D printing options as a greener way to build. It reduces waste and energy consumption because there is little to no unused construction material. Reduced construction waste is the product of the 3D printing process using only what it needs to create the finished product, which reduces a construction site’s impact on local landfills. Energy consumption is reduced because contractors, subcontractors, and/or suppliers are not required to burn fuel to haul in large amounts of construction material, and then haul off the material not incorporated into the project or the resulting waste. Some 3D printing advocates, such as WinSun, claim that the positive impact could go even further by utilizing construction waste from traditional construction processes as part of the 3D printing material. However, what 3D printing has to offer in the way of green building is yet to be seen.
REGULATORY CONSIDERATIONS
Given all the hype about 3D printing’s positives, there are legal considerations that must be taken into account. Note that the location of the 3D printing examples provided above are ventures outside the United States. No American construction industry participant is known to be taking any steps publicly towards 3D printing. That is possibly because government regulations have been a deterrent or obstacle. Most people in construction in some form or another would not disagree that safety is among the chief concerns on a jobsite. Governmental entities, such as the Occupational Safety and Health Administration (OSHA), were created with the purpose of safety in mind, and OSHA’s mandate has a salient effect on the construction industry. Additionally, on the state and local levels, safety is also a main concern. State legislatures pass laws addressing occupational safety issues and equipping state government agencies with the authority to enforce them and promulgate additional rules. And municipalities throughout the country, some more or less stringent than others, dictate the forward procedure of construction at some levels, often the most crucial.
Because 3D printing is an untested and novel idea, its safety is also unknown and untested. Federal, state, and local government oversight is a clear obstacle to the actual use of 3D printing in the construction industry. In addition to the public entities that regulate the construction industry are the private interests that influence them. For better or worse, any change that will be brought on by the utilization of 3D printing in construction will be met with some level of doubt, concern, or outright opposition. Lobby interests will no doubt affect the efficiency with which 3D printing technology in the construction industry will move through the necessary and required legislative and bureaucratic processes.
3D PRINTING IS COMING
It is a safe prediction that 3D printing will be a part of large scale construction in the future. What is not safe is to predict when this will be true. Cost, efficiency, effectiveness, and government regulation are factors that will affect 3D printing’s place in the market. ■
About The Author: JD Holzheauser is a construction attorney with Ford Nassen & Baldwin P.C. (www.fordnassen.com), which is nationally recognized in the industry and is one of the largest construction law firms in Texas. Mr. Holzheauser serves his clients in all construction-related matters. He is resident in the firm’s Austin office and may be reached at jdholzheauser@fordnassen.com or 512.236.0009.
_________________________________________________________________________
Modern Contractor Solutions, May 2015
Did you enjoy this article?
Subscribe to the FREE Digital Edition of Modern Contractor Solutions magazine.
3D Printing in Construction
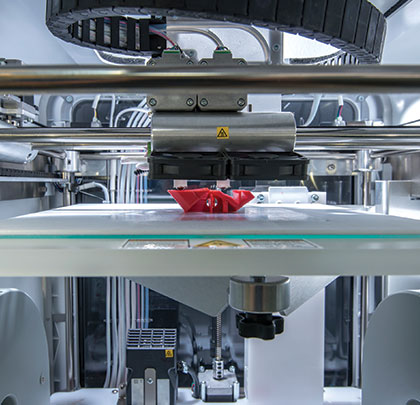