By Simon Bae
There’s no way around it, construction projects produce surprises. Sometimes they’re good, but mostly they’re not—costing money and time and, in the worst cases, impacting relationships between owners and builders, prime contractors, and subs.
Fortunately, there’s been a steady flow of investment in the development of new technologies designed to help eliminate those surprises and keep projects on track.
But here’s the problem: many of these new solutions are focused on just one phase of a building’s lifecycle—whether pre-construction, construction, post-construction, or maintenance and operation.
Make no mistake, virtual online tours, mobile LiDAR, 3D scanners, and 360-degree video-based (or photo-based) documentation—among others—all have their uses and, within the context for which they were designed, can add a lot of value.
The downside is that this piecemeal approach frequently results in huge information gaps between one construction phase and the next, introducing new risks, new complexities, and new costs for owners, property managers, and builders alike.
SUPPLY FOLLOWS DEMAND
This disconnect becomes particularly evident, for example, in the handoff from builders to owners after a massive project, or when property managers take over the maintenance and operation of a building or facility. There’s typically a massive gap in information, making it nearly impossible for owners or property managers to have a clear view of the history of a site, the issues that may have come up, or things they need to watch out for.
As a result of this information deficit and the problems it causes, the construction sector has been looking for comprehensive solutions that reduce cost, save time, and deliver value across the entire building lifecycle—especially during handovers to owners and property managers.
GAP IN THE MARKET
Again, there are all kinds of technologies available to owners, property managers, and builders to help them visualize a construction project before it’s built. There are even some that will help them visualize what’s happening during construction. But almost none of them give you an up-to-date accurate view of what’s happening all the way from initial blueprint to final handoff.
That’s where 3D digital twin platforms come in.
A 3D digital twin platform—one with easy data capture and spatially accurate 3D visualization—delivers value across the entire built-world lifecycle. And that continuity of critical insight before, during, and after a project has been completed is a game-changer.
And, the 3D digital twin platforms that provide the most value are those that enable frequent, easy, seamless 3D site capture, with uniformly high-quality data. After all, what good is a new cutting-edge technology if you can’t use it frequently and easily?
CUTTING-EDGE TECHNOLOGY
For example, until now, the only way to create a truly accurate 3D digital twin of a jobsite was to use a 3D scanner. But it was a time-consuming and expensive option, meaning that creating as-built 3D data scans on a weekly, or even monthly, basis has not been practical. Alternatively, you could use LiDAR or a mobile 3D scanner, or even a 360 camera, but typically you sacrifice accuracy in the spatial data, so it’s nearly impossible to tell where various components and assets are in relation to each other.
Fortunately, with the right 3D digital twin solution in place, it’s now fully practical. Perhaps still more important is the ability for a 3D digital twin platform to work with builders’ existing construction management platform. A solution that requires users to integrate yet more tools isn’t a solution—it’s a time suck and hindrance.
In contrast, the best new 3D digital twin solutions are embedded within users’ existing construction management software, meaning users don’t ever have to “leave” their existing construction management platform or alter their normal operations. Using their current platform, users can remotely “walk through” a jobsite, navigating to the location of RFIs, observations and open items, searching by the location names they already use, e.g., main lobby, atrium, conference room A, conference room B, etc.
Additionally, users are able to review jobsites retrospectively, enabling teams to review iterative progress on a jobsite dating back days, weeks, or months.
CLOSING THOUGHT
While there is no shortage of vendors and technologies who can deliver value on one piece of an overall construction project, a new wave of solutions deliver the real control that owners and builders need—from blueprint to building and beyond.
About the Author:
Simon Bae is CEO and founder of Cupix, a San Jose, California-based leader in 3D digital twin technology for general contractors, owners, and property managers. In a career spanning more than 25 years, Bae previously founded and served as chief executive of INUS Technology and VisPower, both later acquired by 3D Systems. For more, www.cupix.com.
Modern Contractor Solutions, November 2021
Did you enjoy this article?
Subscribe to the FREE Digital Edition of Modern Contractor Solutions magazine.
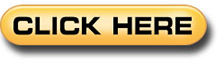