The reasons are endless why concrete contractors are benefiting from Ligchine International’s laser-guided boom screeds. Ligchine International is a young, results-driven, concrete screed manufacturer with offices in Indiana and manufacturing in Wisconsin. With three boom-operated laser screeds to choose from, Ligchine can accommodate ScreedSaver machines for companies of all sizes and lines of work.
The science behind laser-guided screeds isn’t new or overly complex. Historically, boom screed machines have utilized a screed head with two laser receivers attached to masts on each side that process the signal of the construction laser strike to retain precise concrete thickness and levelness as the machine passes through. The technology is simple and very effective but limited to a certain type of finished concrete applications—typically flat, single slope, and dual slope slabs. The reason for its limitation is the laser strike cannot be “bent” across a plane for different contours and will always remain a straight line.
In 2014, Ligchine International partnered with Topcon Corporation to integrate its Millimeter GPS 3D satellite and machine control system into the ScreedSaver lineup. Initial results have been a huge success in the marketplace. The addition of the mmGPS 3D system to the machine allows for full contoured concrete screeding and paving, which further enhances an already versatile and capable machine that is dominating the 2D laser-guided screed market.
INITIAL mmGPS TEST PROJECT
Ligchine International’s manufacturing facility is located in southern Wisconsin near the Chicagoland area, allowing the company numerous opportunities for testing and demonstrating on actual live concrete jobs. The first official trial run for Ligchine with Topcon’s mmGPS proved to be a total success. The mmGPS was installed onto Ligchine’s ScreedSaver MAX model, which is the largest in its machine lineup. The ScreedSaver MAX is a wireless remote-controlled, 35 hp Kubota diesel-powered screed that features front wheel drive, rear wheel steering, and parallel to the pour navigation. The MAX can produce up to 200 square feet per screed pass. The 30,000-square-feet convenience store parking lot in Rock County, Wisconsin, called for 6-inch thick concrete matched up the already placed curb surrounding the perimeter of the area. Water flow lines had to be perfect for proper runoff and to avoid pooling on the pedestrian sidewalks. With the jobsite program loaded into the ScreedSaver, Topcon’s machine control assisted the screed in placing a perfectly contoured concrete parking lot that matched all contours and water flow lines with 1/32 of accuracy. The success of the demo resulted in the contractor’s immediate purchase of a ScreedSaver MAX with full Topcon mmGPS capability.
THE EQUIPMENT
Those unfamiliar with the mmGPS system will find that it is a fairly easy system to learn and operate. With the assistance of Ligchine and the area’s local Topcon dealer, crews can successfully control the system within a few days of training and use. The 3D-guided screed comes equipped with two mast-mounted mmGPS receivers on the screed head that pick up GPS coordinates, as well as precise millimeter elevation readings. The screed leveling system is controlled by the Topcon MC-R3 machine controller and information and job mapping is displayed on a Topcon GX-60 computer. To digitally map the jobsite, the package includes the Topcon GPS Base and Rover receivers, Topcon FC-500 Field Computer with Pocket 3D, PLZ-1 Laser Transmitter for millimeter elevation broadcasting, and a Topcon millimeter rover receiver. Typically, a single point localization jobsite is set up based off of control points plotted for your Topcon GPS Base Receiver and PLZ-1 Laser Transmitter. Using both Topcon GPS and millimeter rover receivers mounted onto a mast with the FC-500 Field Computer, a jobsite is digitally mapped and topo points recorded at specific areas within the project. Once a jobsite project is fully mapped and recorded, it can be transferred to the Topcon GX-60 computer mounted on the ScreedSaver. From there, live data and elevations of ScreedSaver within the created jobsite project can be seen and monitored. The equipment produces an automated concrete screeding process that adheres to the elevations plotted on the jobsite project.
VERSATILITY AND BENEFITS
Ligchine’s partnership with Topcon has yielded additional benefits aside from precise, contoured concrete paving. Topcon’s mmGPS system has long been a highly respected system for grading, surveying, and site preparation. The versatility of using the same hardware components universally for site preparation, as well as contoured concrete screeding, greatly increases the cost-effectiveness of adding 3D capabilities to the ScreedSaver. The addition of the Topcon mmGPS does not limit the ScreedSaver to strictly contoured paving because the system can easily be removed to allow the screed to run its standard 2D system for flat and sloped concrete applications. ■
For More Information: For more information about Ligchine International and its equipment lineup, visit www.ligchine.com.
_________________________________________________________________________
Modern Contractor Solutions, May 2015
Did you enjoy this article?
Subscribe to the FREE Digital Edition of Modern Contractor Solutions magazine.
3D Concrete Paving
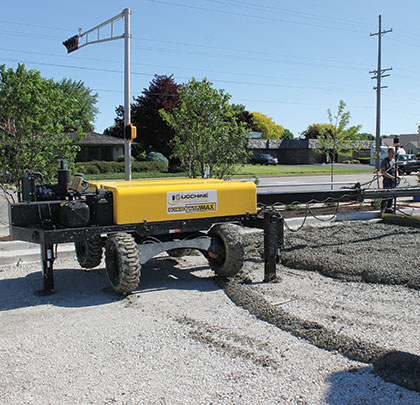